FAILURES
Deborah Slaton, David S. Patterson, AIA, and Kenneth M. Itle, AIA
The exterior walls of structures built in the late 19th and early 20th centuries are usually constructed of multi-wythe solid loadbearing brick masonry. When considering the management of moisture in the building enclosure, this type of solid masonry wall construction is often called a mass wall.
A mass masonry wall resists moisture penetration by shedding bulk water at the surface and by absorbing, storing, and later releasing moisture. In mass wall construction, proper detailing is required so that the wall will shed bulk water. Key details include overhangs that protect the vertical wall below; drips at projecting features such as sills; and sloped skyward-facing surfaces to provide positive drainage. Additionally, mass wall construction relies on proper maintenance to maintain its water-shedding properties. For example, mortar joints in the exterior wythe must be free of voids or cracks, and sealant joints (typically used at skyward-facing surfaces such as the top of copings) need to be intact and well bonded to the adjacent masonry. Even with proper detailing and maintenance, it is anticipated that some moisture will be absorbed by the masonry during rain events. This moisture can be stored within the masonry and later released through evaporation during dry weather without degrading the integrity of the wall. However, if the masonry materials become saturated (as can occur due to improper detailing or lack of maintenance), the masonry may deteriorate over time, and materials at the building interior can be affected.
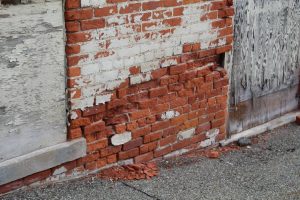
Photo © Kenneth Itle, WJE
The first example is the exterior face of an exterior, three-wythe mass masonry wall built in the 1910s, which has deteriorated due to moisture intrusion. Cracked, open, and debonded mortar joints have allowed increased levels of bulk water from rain and snow accumulation to infiltrate the masonry. Previously applied non-breathable coatings have also limited the ability of the masonry to release moisture. Since an asphalt-paved parking lot is directly adjacent and slopes toward the wall, additional moisture has likely been directed against the bottom portion of the wall from water flowing across the pavement. Other possible contributors to the more significant distress observed near the base of the wall include water flowing down the face of the wall, migration of water within the masonry due to gravity, and effects of deicing salts used on the adjacent pavement. Although much of the wall is performing adequately, the quantity of moisture near the base of the wall has exceeded the ability of the masonry to effectively store and release moisture, resulting in the observed face spalling of the brick, which is largely attributed to cyclic freezing and thawing of moisture-laden brick.
The second example is the interior face of an exterior, five-wythe mass masonry wall constructed in the 1890s. Failure of the copings, and open and debonded mortar joints on the exterior face of the wall, have allowed increased amounts of water to infiltrate the masonry, leading to efflorescence and spalling of the brick on the interior.
Repair of these buildings will include selected replacement of brick with significant spalling, repointing of mortar joints, repair of copings, removal of coatings, and improvements to site drainage. Due to their period of manufacture the bricks themselves may not meet the current performance requirements for Severe Weathering grade brick, as defined in ASTM C216, Standard Specification for Facing Brick (Solid Masonry Units Made from Clay or Shale). However, as evidenced by the condition of the masonry elsewhere in these buildings, the walls appear capable of continuing to provide adequate performance if excessive water entry can be prevented.
The opinions expressed in Failures are based on the authors’ experiences and do not necessarily reflect those of The Construction Specifier or CSI.
Deborah Slaton is an architectural conservator and principal with Wiss, Janney, Elstner Associates (WJE) in Northbrook, Illinois, specializing in historic preservation and materials conservation. She can be reached at dslaton@wje.com.
David S. Patterson, AIA, is an architect and senior principal with WJE’s office in Princeton, New Jersey. He specializes in investigation and repair of the building envelope. He can be reached at dpatterson@wje.com.
Kenneth M. Itle, AIA, is an architect and associate principal with the Northbrook office of WJE, specializing in historic preservation. He can be reached via e-mail at kitle@wje.com.
What about using a waterproofing agent like Evonik’s PB100 that allows moisture to migrate out of the wall but act as a rain screen. The other thing I have noticed that the top of the parapet will allow moisture into the wall. The other thing I have seen is the vortex on the inside of the parapet pulls the mortar out of the joint, allowing moisture into the wall