Protect horizontal surfaces
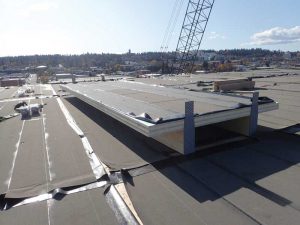
Floors and roofs are at elevated risk of water penetration during construction. However, strategies can be employed for both types of assemblies to minimize exposure.For roof assemblies, a fully adhered membrane installed by the supplier before the panel leaves the production facility can provide protection against moisture during transport and storage (Figure 3).
This membrane can also serve as a temporary roof membrane after the panel has been installed. The author’s firm recommends “designing in” this protection layer in the place of the deck-level air control layer (commonly referred to as the roof vapor retarder) in the finished assembly.
Floor decks may also be exposed to rain for shorter periods during construction but are still subject to saturation of the mass timber and staining of the exposed surfaces (Figure 4).
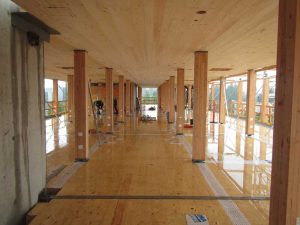
Recommendations for protection for CLT, glue-laminated (glulam) timber, and nail-laminated timber (NLT) floor panels differ slightly. Due to the tightly assembled panel construction, CLT and dowel-laminated timber (DLT) panels are less open to bulk water penetration. A wax-based sealer on the end grain with a low permeance polyurethane coating on the top surface of the panel will generally be enough protection if rain exposure can be minimized. The author’s firm has tested several options and recommends the following:
- apply the coating in the factory, testing if necessary to ensure adequate thickness (avoid site installation).
- apply waxed-based coating to all exposed edges, including internal service penetrations and where fasteners and anchors will be installed.
- observe the coating manufacturer’s installation instructions for moisture content of the wood (often best controlled at the factory) and surface preparation.
- include requirements for construction-phase moisture protection.
Glulam floor panels may need less protection because of the tight wood-to-wood panel construction, and many suppliers use a light sealer to protect the wood during shipping. Onsite taping of panel joints and internal service penetrations is recommended.
With more open joints between parallel laminations, NLT panels require more protection than CLT and glulam. Water penetrating between NLT laminations and absorbing into the wood mid-panel depth is more difficult to dry than moisture adsorbed by the upper or lower surfaces. NLT panels often include a cover layer of plywood or oriented strand board (OSB) on the upper surface and the joints in this layer can be taped after installation to provide a continuous water-resistant layer. Some OSB sheathing products are designed with an integral coating and can provide more resistance to moisture. This type of product could be specified from the outset if construction is likely to occur in a season with high precipitation, or the design and construction team may consider changing to this type of product to enhance moisture protection if the construction schedule moves towards a rainier period of the year. If heavy rain is unavoidable during the construction of the floor levels, a factory-applied coating, sealer, or membrane can be added to the cover layer’s upper surface (Figure 5).
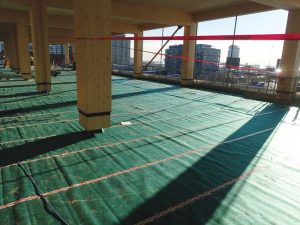
The added resistance to water penetration provided by the steps described above will also help control bleed water from concrete or gypcrete floor toppings. Further, each of these measures provides a built-in protection against accidental exposure to water during operation of the building.When the full construction schedule for a tall building is considered, a reasonable approach to protection for horizontal surfaces is to create multi-story compartments rather than addressing every floor. This allows for “break points” to be planned into the schedule to accommodate weather and schedule delays: construction proceeds to designated levels where a complete water-resistant layer is installed before continuing the build. Weather events affect only the uppermost compartment. This strategy also allows for the air- and water-tight compartments to proceed with interior work, and probably more importantly, have active temporary fire protection systems during construction.
Design assemblies for long-term protection of the mass timber structure
Mass timber structures will have a long service life if kept within stable temperature and moisture conditions—the objective is to create and maintain warm and relatively dry conditions. The author’s firm recommends an enclosure to the exterior of the primary structure that passes over and encloses each floor level. This approach minimizes unprotected structural elements, and, as noted above, also helps address fast weathertightness of the building during construction. The design objective will be to keep all mass timber elements within, and protected by, the thermal enclosure.
Designing mass timber assemblies to allow for in-service drying is an important long-term protection against unexpected water intrusion. Generally, roof and floor assemblies should be designed so that drying is possible to at least one side of the assembly.
Wood undergoes shrinkage as it comes into equilibrium with the conditioned interior environment of the building. Tall wood structures have the potential (depending on framing and the specific products used) to undergo a significant amount of drying shrinkage. Although the overall shrinkage of the structural frame will be considered in the structural design, it is critical to look at how this movement will affect joints and transitions between materials and systems, and special attention should be paid to interfaces with building elements (such as concrete elevator cores) that will move differently over time. It is important to note unexpected wetting during construction may lead to dimension changes as the building dries.