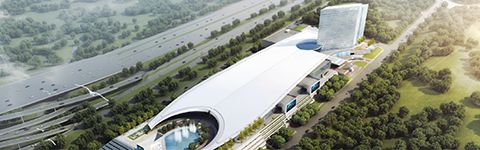
One of the new options for complying with the responsible extraction criteria is ‘extended producer responsibility’ (EPR), also known as ‘product take-back.’ This involves taking products at the end of their useful life and recycling them into the same product in a ‘closed-loop’ system. Currently, this credit option is difficult to achieve because there are limited products with EPRs—the authors are unaware of any for CMUs or other masonry products. (Some exist, for example, for carpeting.) Further, products meeting criteria for this credit are valued at 50 percent of their cost.
To meet this credit of responsible extraction practices, some CMU manufacturers provide products with recycled content to projects. The recycled content credit is calculated in the same way as it was in LEED 2009—that is, the sum of postconsumer recycled content plus one-half the pre-consumer recycled content. The credit states products meeting the recycled content criteria are valued at 100 percent of their cost in credit calculations.
Material ingredients
There are three options to achieve Building Product Disclosure and Optimization–Material Ingredients, but only the first two options are currently viable. The first option is around material ingredient reporting. Projects must use at least 20 different permanently installed products from at least five different manufacturers using one of the approved programs to demonstrate the chemical inventory of the products.
Acceptable approaches include products that have published health product declarations (HPDs) in accordance with the HPD Open Standard, or products that have been certified by Cradle to Cradle (v2 Basic or v3 Bronze level). HPDs are transparency documents similar to EPDs, except they disclose materials that may pose a health risk for either an end user or a person involved in the manufacturing of that product. To achieve this credit, a single manufacturer can contribute up to four HPDs toward the 20 required.
A second option takes it to the next level of optimization where one point is awarded when products are used that document their material ingredient optimization employing various approved tools. Options of compliance include products certified under Cradle to Cradle (where v2 Platinum products are valued at 150 percent of cost, for instance) and GreenScreen (where products can be valued at 150 percent of cost if they undergo a full GreenScreen Assessment).
The third option within this credit involves supply chain optimization. This credit is not currently viable, but USGBC has assembled a working group to iron out the details of this credit in order to make it viable. The intention of the credit is to encourage sourcing from manufacturers who “engage in validated and robust safety, health, hazard, and risk programs.”
The easiest way for masonry producers to contribute to this credit is by issuing HPDs or Cradle2Cradle certifications. An individual company can provide HPDs/C2Cs on up to four products for a particular project, which is a significant portion of the 20 total documents required to collect the credit. If the products meet a certain set of criteria, such as local sourcing and the absence of the highest level of hazardous material, they may be eligible for additional points.
Regional materials multiplier
In the MR credit in previous versions of LEED, points were awarded to projects that sourced materials regionally. However, this is no longer the case in LEED v4. Under the new program, separate points are not awarded for sourcing materials regionally, but rather a “regional material multiplier” is applied to other categories to increase or decrease the value of the points in the credit calculations.
For each of the three Building Product Disclosure and Optimization credits, the regional materials multiplier is applied in the same way. Products sourced within 160 km (100 mi) of the project site are valued at 200 percent of their cost in credit calculations. Another major change is the regional material threshold has been reduced from 800 km (500 mi) down to 160 km.
Conclusion
As concrete masonry unit manufacturers continue to promote sustainable practices, they will seek out new opportunities to reduce the environmental impact of the products they manufacture—implementing CO2 recycling technology is just the first step. With both EPDs and HPDs available for these products, architects can ask for these documents to help them achieve credits and points on projects going after either LEED 2009 or LEED v4 certification.
Jennifer Wagner, MSc, MBA, LEED Green Associate, is the vice president of sustainability for CarbonCure Technologies, a company that retrofits concrete plants with a technology that recycles waste carbon dioxide into the building units. Experienced with carbon accounting, she is a member of the Health Product Declaration Manufacturers’ Advisory Panel. Wagner can be contacted via e-mail at jwagner@carboncure.com.
Chelsea Code-McNeil, LEED Green Associate, is CarbonCure’s sustainability coordinator, and works to reduce the carbon footprint of the concrete industry. Formerly a LEED coordinator for a prominent architectural firm, she is a member of the Health Product Declaration Manufacturers’ Advisory Panel. She can be reached at ccodemcneil@carboncure.com.