by Harry Lubitz, CSI, CDT
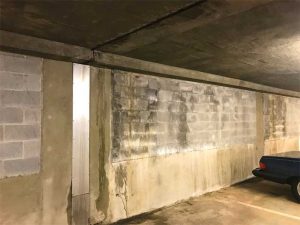
While negative-side waterproofing is not the usual first choice in new construction of foundations, it clearly has its place. It is often selected as the last resort when other options (positive and blind sides) are impractical. Often, negative-side waterproofing is better than re-excavating the entire structure when the original waterproofing materials fail and water is actively leaking.
When positive-side and blindside waterproofing are applied, water under hydrostatic pressure would not permeate the foundation and the building is expected to remain dry for life. Unfortunately, this is not always the case, and the solution either involves excavating the foundation to conduct repairs or retrofitting the insides of the wall with a negative-side waterproofing application.
Negative-side waterproofing is the application of a coating material to the interior or the ‘dry’ side of a foundation or wall. Its primary function is to create a barrier coat to stop water from leaking through the wall and keeping the space dry.
Negative-side waterproofing can also help offer a secondary function of providing a decorative surface that offers a value above and beyond a coat of paint. It makes the foundation space more attractive and livable, while serving to keep water out.
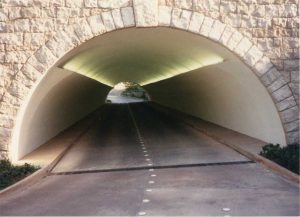
All foundation coatings, including negative-side applications, must be impermeable and withstand hydrostatic pressure, the force exerted in every direction on a foundation. Standing water exerts approximately 3 kPa (0.43 psi) for every foot of water. Consequently, the significant force created by the water will find its way through the foundation wall and into the (formerly) dry space.
Categories
Negative-side waterproofing materials typically fall into two categories:
- penetrating liquid acrylic waterproofing materials sealing voids and capillary openings where water seeps through; and
- cementitious surface coatings providing a secondary cement-based barrier.
Penetrating liquid acrylic waterproofing materials have expanding polymer or crystalline additives as part of their chemistry. On application, these additives expand or grow to block the water-invading pathways. Cementitious surface coatings rely on the applicator to ‘push’ the product into the pathways, and then the product hardens to create a barrier.
Negative-side waterproofing has clear advantages. It can be installed with full visibility and can be easily repaired. It can be applied any time after the substrate material has cured. It can be applied with minimal training and is usually cost effective. Unfortunately, since it is installed from the inside of the structure, the substrate material is not waterproofed, and therefore, unprotected from corrosive soil materials or freeze/thaw cycling.
Hydraulic cement
Negative-side waterproofing does have its limitations. It requires secondary assistance when the substrate has cracks larger than 1.5 mm (1/16 in.) or actively flowing water leaks. In these circumstances, hydraulic cement is the recommended course of action. Hydraulic cement is a more modern invention with unique properties and several advantages.
First, hydraulic cement is easy to mix with clean water and can be troweled into any shape. Second, it expands on curing and will seal static cracks up to 19 mm (¾ in.) wide and/or deep. Third, it will work to plug actively flowing water. Finally, it sets quickly (within three to four minutes) using cold mixing water—warm mixing water accelerates the set time and reduces working time. Using hydraulic cement to tool joints between floors and walls is also a recommended practice. It is important to note hydraulic cement will not stop moving (dynamic) cracks.
Care should be exercised when using hydraulic cement as it is Portland cement based. Proper personal safety equipment, such as eye protection, rubber gloves, and a National Institute for Occupational Safety and Health (NIOSH)-approved respirator, should be used. Breathing Portland cement dust is a health hazard. Some heat is also generated during the chemical reaction with water, therefore, it is best to avoid skin contact with the material.