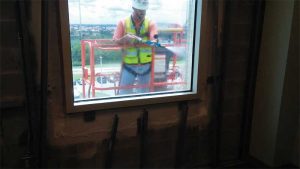
It is a good practice to dampen surfaces prior to applying hydraulic cement. This is also recommended before using cementitious surface coatings. Hydraulic cement is compatible with both penetrating liquid acrylic waterproofing materials and cementitious surface coatings that could be employed as topcoats after curing.
Providing a proper substrate for these materials is critical. Negative-side waterproofing coatings need an unobstructed access to the base substrate material to penetrate the voids and capillary pathways the water is using to intrude. Removing old surface coatings, paints, foreign matter, dirt, efflorescence, and other substances that would impede both penetration and proper bonding are critical for success. Commercial cleaning and etching materials are available to assist in this process.
Etching or abrading the substrate provide a proper surface profile to allow for better penetration and ‘grip’, especially on smooth troweled or precast substrates. The International Concrete Repair Institute (ICRI) has developed a concrete surface profile (CSP) classification to simplify the specification. It is advisable to refer to the waterproofing material manufacturer’s product data sheet to ascertain the recommended CSP.
There are circumstances other than foundation water intrusion where negative-side waterproofing is the logical choice from the outset. These fall under the category of waterproofing where access to the positive side of the substrate is impossible or financially impractical or the negative-side application adds to the entire waterproofing system.
Tunnels
Sophisticated passenger, traffic, and rail tunnels rely on negative-side waterproofing to keep them dry. High-tech geotextiles are incorporated into the structural layers underneath a final surface coating as part of a waterproofing and water management system. Often, as a ‘belt-and-suspenders’ approach, a final topcoat of penetrating liquid acrylic waterproofing is applied to give a final layer of protection, and is tinted to provide decoration.
Less sophisticated tunnels rely on more traditional negative waterproofing products like those previously mentioned to seal foundation walls. To maintain these types of tunnels over time, the occasional topcoat of tinted penetrating liquid acrylic waterproofing is recommended to keep the interior dry and attractive.
In-ground tanks and cisterns
A negative-side waterproof coating is often used to coat the inside of in-ground tanks to seal in its contents and prevent water intrusion. In-ground potable water storage tanks and cisterns utilize negative-side waterproof coatings. These should be specified to comply with NSF International/American National Standards Institute (NSF/ANSI) 61, Drinking Water System Components. Also assure any confined spaces like enclosed tanks are properly ventilated to protect workers and ensure proper curing of the coating.
In-ground water features
Similar to tanks, other in-ground, water-holding devices like decorative water features and swimming pools need to be kept clean and sanitary. Holding ponds for other wildlife need to be properly coated to keep ground contaminates out and clean water in. Negative-side applications of penetrating liquid acrylic waterproofing materials or cementitious coatings serve this purpose. Adding tints to liquid waterproofing offers multiple decoration options. Interior waterproof coated surfaces are easier to maintain and do not tend to leak as those treated with concrete paint films alone.
Retaining walls
A retaining wall is really an outdoor foundation designed to keep soil and water under control. Positive-side waterproofing placed on the soil side of the wall creates a primary barrier, while negative-side waterproofing develops a secondary barrier to water migration. The latter can also be tinted to add beauty to the visible (dry) side of the retaining wall.
Elevator pits
Elevator pits should be properly waterproofed from the positive side as they are a ‘foundation’ surrounding the elevator components. Unfortunately, the positive-side waterproofing tends to fail here more often than regular foundations due to the lack of proper selection and installation attention. Providing an additional barrier with a negative-side waterproofing application helps keep elevator pits dry. By adding a tint to a liquid acrylic waterproofing material, the elevator pit becomes a more attractive place for elevator service persons to work and easier to maintain. The negative-side coating will seal the pit from the inside and capture any leaking fluids from the elevator system and prevent them from penetrating the pit walls.