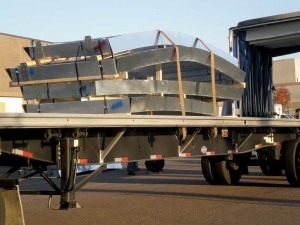
Proprietary hat channels can eliminate the need for clip connections, are easier to attach to various surfaces than other materials, and can be flexed in the field. Curved hat channel offers more strength using less material because it can be installed in longer spans than most stud shapes. No clips are used, so torsion is removed. For these reasons, curved hat channel is an economical alternative for use in:
- exterior walls;
- domes,
- roofs to interior ceilings;
- barrel vaults; and
- other curved surfaces.
Due to its geometry, contractors working on the renovation of historic buildings or retrofits find pre-curved hat channel can attach to an ‘out-of-true wall’ and be shimmed to provide a level surface to attach drywall. Additionally, hat channels can provide sound dampening characteristics as acoustic sound travels differently though angles than straight surfaces.
The twisting façade of the new Edmonton International Airport control tower in Alberta, Canada, is an exemplary profile of how hat channel is used to solve a complex problem. The tower perches on the edge of an office building and features a metal ‘wrap,’ which is covered with shingled undulating zinc carefully integrated with windows to maximize daylight and offer shading when needed. The design and construction team developed a method for curving hat channel that provided a smooth surface for the finishing material and more importantly, served as a way to ensure accurate and easy installation.
This hat channel framing solution was attached to the trusses and served as the surface to attach the decking and zinc finish. Since the channel could be fabricated to a highly exacting curvature, it arrived on the jobsite perfectly aligned to the trusses. As the metal ribbon twisted and turned around the building, the underlying hat channel had to be curved to meet each unique bend. The high degree of accuracy allowed hat channels to be used to help place the location of the trusses.
Thinking outside the box
Curved box beams can make complex aperture framing significantly more cost-effective in many cases. By substituting CFS box beams for more traditional red iron structural steel in façade openings, contractors can achieve significant savings of time and material. As architects continue to push the envelope to create more interesting building façades and roofs, the use of curved surfaces is gaining popularity. There are now new methods to frame openings using structurally engineered curved box beams made from CFS.
These new methods reduce the framing assembly’s weight and provide the same finished result for reduced cost. Some examples are at curved window head and sill locations, curved canopies replacing tube steel, and large curved openings where profiles may include curved support elements.
There are multiple material and installation benefits of using a curved box beam. CFS costs less than structural steel and can be easily formed for curved surfaces. Beams made from CFS are simpler to attach, due to their tolerance of ± 3.17 mm (1/8 in.) in 7.3 m (24 ft), and connector clips are the same length. Equipment use and power costs are reduced because welding or powder-actuated fasteners are not required. CFS beams do not require expensive as-built laser surveys. In fact, accurately located beams can establish control geometry for the installation of stud framing.
Box beams score at the Minnesota Twins Stadium
When the Minnesota Twins decided it was time to take baseball back to the great outdoors in 2010, the new Target Stadium had to be designed for every kind of weather. The design included a giant, swooping sunshade canopy that serves to shelter fans from sun, rain, and even snow.
Structural tube steel was originally envisioned to create the sunshade, but the design team quickly realized this option would be expensive, heavy, and stiff, making construction difficult. The use of tube steel also offered potential integrity problems when welding the steel into the framing. The solution was an interface system that supports the metal decking independent of the structural steel. An intricate assembly of curved box beams supported the finished surface shape. Structural engineers determined the size, spacing, and span of the box beam, and then 14-gauge CFS beams were crafted to its required dimensions. Most beams ranged between 6.1 and 9.1 m (20 and 30 ft), and the curvature of each had to be perfect to achieve the canopy’s swooping, circular lines.
Every one of the 230 box beams was meticulously coded for easy installation, using a numeric and color-coded system. The sunshade also houses intricate lighting and sound systems, which were studied using 3-D modeling capabilities prior to modifying the beams in precise locations to accommodate openings before the installation of 7432 m2 (80,000 sf) of metal panels. The solution saved considerable time and money and the work was completed two months ahead of schedule.
When big ideas cost less
Architectural firms are pushing the boundaries of curved surfaces in every detail of their designs. Buildings such as the Disney Concert Hall (Frank Gehry Partners) and the Kauffman Performing Arts Center (Moshe Safdie & Associates) are among the most recognizable applications of curved CFS technology, and the concept has spread to even the simplest retail soffit. Once limited by techniques such as stretch-forming and hand-bending in the field, geometrically precise curves are re-inventing what is possible. By expanding the limits of simple materials like CFS, and integrating them with modern modeling technology, curves in buildings have become simpler, and often cost-effective solutions.
Chuck Mears, FAIA, is the founder of Minneapolis-based Radius Track Corporation. Mears’ pioneering work in 3-D computer modeling technology linked to fabrication allows his team to create steel structural systems to support any imaginable architectural form. He began studying the art of curved surfaces while designing retail stores for national chains using basic computer-assisted design (CAD) software. Mears created 3-D algorithms to model surfaces and link them to fabrication systems in-house. He can be contacted at chuck@radiustrack.com.