Weight-loss goals
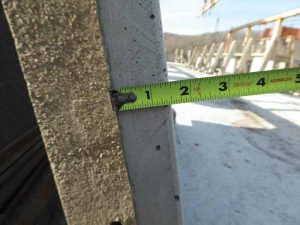
The new and improved high-performance concrete (HPC) was developed by researchers and chemists at ORNL and UT (Chattanooga). The slimmer version of a precast concrete insulated panel weighs 1602 kg/m3 at an estimated $300 per cubic yard. The team continues to tweak the high-performance concrete mixture proportions.
“Precasters conducted trials with preliminary mixes, but we are trying to further optimize them,” says Diana Hun, sub-program manager for building envelopes at ORNL. “We reached the target concrete properties we were tasked to achieve, namely 4137 kPa (600-psi) flexural strength in 12 hours and the 45-kg (100-lb) density. Now, we are researching if we can further reduce costs.”
The assembly consists of two thin concrete wythes attached to insulation.
“While the optimum R-value of future panels depends on local building codes, we are using four inches of XPS [extruded polystyrene foam] for test purposes,” says Hun.
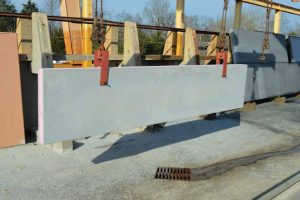
Images courtesy ORNL
“The development of a high-performance concrete mix to allow precasters to reduce piece thickness translates to lighter cranes, fewer trucks, less concrete, and reduced costs,” says Roger Becker, vice-president of technical services for PCI.
Lightweight concrete is nothing new, as it has been around in various forms for centuries. While normal-weight concrete typically weighs 2323 kg/m3 (145 lb/cf), lightweight concrete is around 1762 kg/m3 (110 lb/cf).
Lightweight and normal-weight concrete have a comparable 28-day compressive strengths. However, high-performance, lightweight concrete has higher early flexural strength, by almost 30 percent. This is significant because stripping, yarding, and shipping precast concrete impose more significant stresses than experienced on a building.
Steve Brock, senior vice-president of engineering at a precast concrete manufacturer, has been actively involved in field testing the mix.
“This mix reduces cracking without being prestressed. There is not enough concrete cover over any type of steel. We are testing carbon and glass fibers and stainless-steel wire reinforcement,” he says.
Another benefit is the ease of widespread adoption for the lightweight concrete. It was designed so as not to require major changes to precast concrete manufacturing facilities across the country.
Brock continues, “There really is nothing unusual about the lightweight mix, except for the learning curve regarding additional admixtures and how to handle fibers. A typical precast facility might install additional silos to handle the increase in additives. Right now, we are handling small amounts for testing, but I do not anticipate large changes to batch plants.”
Non-corroding composites
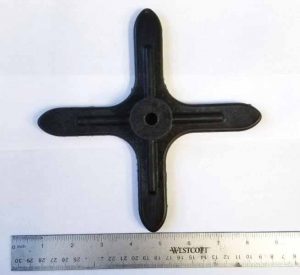
With ultra-thin panel sections, it is imperative the researchers replace traditional steel accessories with non-corroding composite materials.
“The lifting inserts were our first target,” says Hun. “We have achieved our goal by developing a non-corroding composite edge lifter with an ultimate load capacity of more than 5443 kg (12,000 lb).”
The new and improved inserts have broad appeal. Given recent steel tariffs and price escalations, the timing is excellent.
“The intention was to use composites because the wythes are so thin you do not have appropriate concrete cover,” says Brock. “Ultimately, we could use them in any type of product, not just insulated wall panels. The same thing for the lightweight mix—you can use the mix any time you want to lighten up a piece.”
Hun agrees. “The technology can be easily transferred. The inserts can be used in precast or any concrete application where corrosion is a potential problem. This will have a broad-reaching impact.”
In addition to the non-corrosive aspect, the new edge lifters can eliminate thermal bridging. The composite materials have low heat transmittance. Research is still being conducted on the remainder of connectors used in precast concrete wall panels. Ultimately, the research will examine all types of lifters as well as gravity and tie-back connectors made out of composite material.
“While ORNL is focused on insulated panels, this could also benefit architectural panels that are insulated in the field. Metallic connectors from panel to building would be eliminated,” says Becker. “Composite connectors are of benefit to non-insulated panels because if we are not using steel then we are no longer creating a thermal bridge through the field-applied insulation.”