Thermal performance
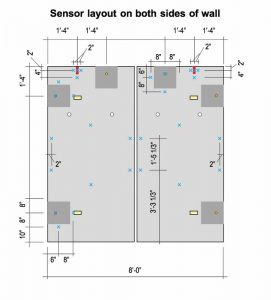
The target to double the thermal performance of a typical precast concrete panel is achieved by adding insulation without increasing the panel thickness. The prototype uses 102 mm (4 in.) of insulation, twice the amount typically used.
To establish a baseline panel (50 x 50 x 76 mm [2 x 2 x 3 in.]), ORNL performed hot box tests as per ASTM C1363, Standard Test Method for Thermal Performance of Building Materials and Envelope Assemblies by Means of a Hot Box Apparatus, to measure the performance of current industry standards.
“When we reach final panel configuration with composite lifters and thinner wythes, then they can do final hot box tests to compare [performance],” explains Becker.
Improved thermal performance is at the heart of this research.
The original test examined a jointed configuration (Figure 1). The results reiterated that two lines of backer rod and caulk proved effective and heat loss was minimal.
Instead of tackling the joint itself, the researchers focused on the more practical goal of improving the sealant and subsequently the air- and water-tightness of joints. Industry feedback has helped direct their efforts. The solution is a caulk that does not require a primer and uses self-healing polymers to make the whole system more durable.
“Here at the lab [ORNL] we collaborate with researchers from various fields, so I reached out to the polymer chemists. We had to raise the bar because there are so many sealants available in the market,” explains Hun.
Cooperative agreement
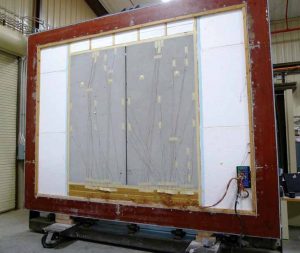
PCI and ORNL have a cooperative research and development agreement (CRADA) enabling this opportunity for government, industry, and academia to jointly pursue common goals. The CRADA has made facilities and expertise available to collaborate and to develop technological knowledge into useful products.
“Ultimately, PCI has first option for licensing any new technology developed as a result of the research. PCI is allowed to restrict use of that new technology to its members,” explains Becker. “The end result is that members who make insulated panels will have sufficient information to demonstrate to the marketplace this system reduces operating energy as compared to conventional cladding materials.”
It is important to note this technology has not yet been licensed, and is unavailable in the marketplace at the time of writing this article.
Most of the research has focused on technologies for new construction. How could this research apply to the significant stock of commercial buildings constructed before energy codes?
The research team has begun studying retrofits and how to improve energy efficiency in older buildings. Retrofit data would demonstrate to owners the energy savings from envelope renovations. Precast concrete has been too heavy for recladding projects in the past. With the new, lighter panels, precast concrete can be considered as a possible solution.
The precast concrete envelope has not changed much in the past few decades, except for gaining a bit of weight. “Not only can this new panel be advantageous in new construction, but also be considered for the re- and over-clad market as well,” anticipates Brock. “If there was an old dorm with poor energy performance and the college cannot afford to move students out for renovation, lightweight precast panels could be a viable solution.”