Spin-offs
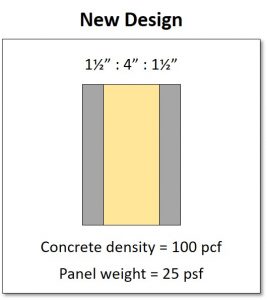
The multiprong investigation has already developed and spun off profitable ideas. One of the standalone concepts generated from this research is 3D printing of molds. ORNL researchers are encouraged to cross-pollinate ideas. Tasked with reducing production time, the team introduced an idea from a different proposal. Several precasters have already turned to 3D printing to decrease the amount of time to create complex molds.
The industry is also exploring how to improve business opportunities and provide precast concrete fabricators with the capability to run two cycles of casting every 24 hours. Nanotechnology is a promising research field that may significantly improve the mixture proportions, performance, and production of concrete, so it makes sense to increase production capabilities. Colloidal nano-silica added to a concrete mixture improves the time of strength development significantly. ORNL wanted to add that challenge as an extension of their research project. They are working with UT (Knoxville) to create mixture proportions that attain 3447 kPa (500-psi) flexural strength and 24,132 kPa (3500-psi) compressive strength in six hours.
Moving ahead
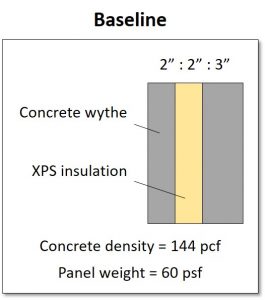
“All of this research can help energize the industry and prevent stagnation of market share. If we are able to match some or most of the goals that were established, it is great example of how a national lab can help the construction industry,” describes Hun.
As a result of this research project, there will be additional methods, materials, and resources to help designers, contractors, and building owners create an energy-efficient and high-performance structures.
“If all we wanted to do was increase energy efficiency, we could simply add more insulation. But the caveat with this research is that the solution be cost-neutral,” says Brock. The research team is closing in on that ambition.
Ultra-high performance concrete (UHPC) offers superior flexural and compressive strength, but it is significantly more expensive. The HPC discussed in this article is targeting some specific properties that are lower than UHPC, but sufficient
to create an energy-efficient building envelope, and also more economical.
Everyone benefits from improvements to thermal performance in building envelopes. When fully developed, these new insulated sandwich wall panels would be lighter, less costly, and easier to erect.
Monica Schultes is president of MM Schultes Consulting and is managing editor of the Precast/Prestressed Institute’s Ascent magazine, where this article originally appeared. She is also the executive director of the Pennsylvania Precast Association.