Design implications of sustainable operation
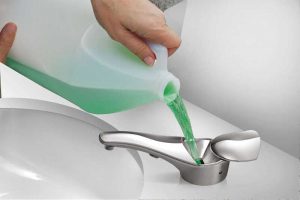
As with any specification decision, conducting appropriate research on sustainable product choices is crucial, as the operational inefficiencies of materials can be costly, for the building owner and the designer’s vision. When design professionals do not sufficiently assess their options and specify products that do not function responsibly, the restroom may quickly become difficult to manage.
For building owners, time wasted on product maintenance is money lost. For example, replacing the cartridges in soap dispensers can require janitorial staff to bend under the counter frequently to replace half-full cartridges. Such was the case at one high-traffic convention and entertainment center on the West Coast. Noticing money was being lost due to inefficient soap dispenser design, a new, chrome-finish bulk foam soap dispenser with top-fill functionality was specified to eliminate waste in both time and product while supporting high-end aesthetics.
As a result, more than 300 units were installed, and all the expenses related to soap dispenser operation and maintenance were reduced by more than 80 percent. Had a less sustainable, but equally aesthetic product been specified, the building owner—shortly into the restroom’s life cycle—may have replaced it with a plastic, wall-mounted dispenser, compromising the design intent of the architect.
Communicating the value of sustainability
As the key decision-maker in product specification, it is standard to provide support materials such as building information modeling (BIM) analyses, technical data, and compliance documentation to support specification decisions. Just as important is fully detailing the long-term value of products that architects specify to appropriate project stakeholders. This is crucial, as each stakeholder, from contractors to facility management personnel, has the ability to challenge or value-engineer products out of the specification if they feel the materials will fail to make a substantial impact on facility operations.
Consumable, water, and energy savings should be outlined and communicated, as well as product durability. Materials with the ability to withstand heavy use over extended periods of time reduces replacement and repair costs and extends product life cycles, minimizing the project’s manufacturing footprint, from transportation to raw materials.
Today, innumerable building products are marketed as ‘sustainable.’ Authentic, long-term sustainability should be considered just as important as eco-friendly materials. It is important to note, many building products marketed as sustainable are manufactured overseas, resulting in higher transportation costs and environmental impact. In the author’s experience, domestically manufactured products often can have a more positive net environmental impact than sustainable materials produced overseas.
Understanding and communicating the operating value of each product, including measurable cost and resource savings, can be the deciding factor in securing the specification. By considering strategies beyond those typically associated with green building, architects can achieve their design vision and make it last.
David Leigh is vice-president of marketing at Bobrick Washroom Equipment, Inc. He had previously served as director of sales & marketing of Koala Kare Products prior to Bobrick’s 2004 acquisition of the commercial child care product company. He can be reached at dleigh@bobrick.com.