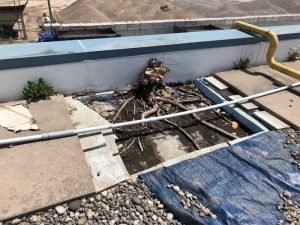
Thermographic roof imaging
In the author’s opinion, the most common, non-intrusive investigation is thermal imaging. It can be used to detect both air leakage in the building envelope and thermal anomalies across the wall and roof assemblies. Depending on the location, thermographic roof scanning is conducted between late spring and late fall. A proper scan requires a cloudless day/night with little or no wind, dry surfaces, and daylight heating. Winds beyond 10 km/h (6 mph) will speed up the cooling of the roof and distort the cooling patterns. Standing water also poses another limitation. Additionally, exhaust fans and other equipment incorporating B-vents/chimneys will have to be turned off, as it may provide alternative thermal signatures that are unrelated to moisture.
In fundamental terms, the process involves the natural (sun) heating up of the roof assembly, and as the roof cools, areas of greater thermal mass
(i.e. wet insulation) will retain heat longer than dry regions. The infrared (IR) camera measures and records the temperature differences of various objects on the roof by reading the emitted heat energy—hotter areas appear brighter with more vivid coloring than cooler zones.
Thermography works on built-up roof (BUR) systems where the insulation is ‘sandwiched’ between the deck and the roof membrane. It is also suitable for conventional modified-bitumen (mod-bit) membranes and fully adhered single-ply membranes such as ethylene propylene diene monomer (EPDM). Thermographic scanning of polyvinyl chloride (PVC) and thermoplastic olefin (TPO) roofs can be challenging, and require special attention due to the inherent sensitivity of light-colored membranes.
Thermal imaging does have some limitations, as it cannot be performed on:
- built-up ballasted assemblies where large 25 to 38-mm (1 to 1 ½-in.) stones are used to hold the membrane in place, as the stones may retain the moisture within the aggregate, and may act as a ‘heat sink’ by absorbing the sun’s thermal radiation, thereby distorting the results;
- loose-laid membranes, as the layer of air between the underside of the membrane and insulating layer may distort imaging;
- inverted roofing systems where the membrane is sandwiched between the roof deck and the insulation; and
- metal roofs, primarily due to the reflectivity of the panels.
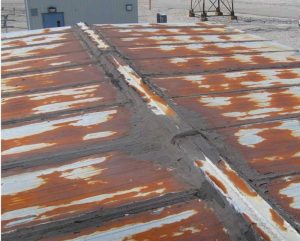
Thermographic scans can only be performed at night. It should be undertaken by people who are properly trained to use the equipment, interpret the onscreen images, and on safety issues. It is advisable to send two people to the site—one to use the equipment and another to record, mark the roof, and act as a safety spotter. A thermographic roof scan can only identify thermal anomalies. The presence of moisture within the assembly will have to be confirmed with a moisture probe or cut tests.
The testing equipment itself has evolved. Gone are the days when liquid nitrogen was required to cool down the IR camera. The equipment is now portable, light, hand-held, and may come with ‘wings’—drones. IR cameras secured to drones allow one to scan a roof from the safety of the ground, by pre-programming the device to fly a specific pattern.
Electronic leak detection
Where thermography is restricted to BUR assemblies and requires ideal weather and environmental conditions, electronic leak detection (ELD) mechanisms can provide more flexibility in locating breaches in the membrane. This diagnostic method can be used on both built-up and inverted assemblies utilizing non-conductive membranes, such as mod-bit, PVC, and TPO and light-colored (white/gray) EPDMs.
ELD testing on black EPDM membranes will not be beneficial because their high carbon content makes them a conductor of electricity.
ELD uses either low or high voltage power sources to create an electrical potential difference between the non-conductive roof membrane and the structural deck, which is grounded to the earth. If there is a breach in the membrane, the electric current will flow toward it, thereby allowing the operator to find the leak with reasonable accuracy.
Low-power ELD begins by laying down an un-insulated wire around the perimeter of the affected roof area. The un-insulated wire is subsequently connected to a pulse generator, and metallic equipment are grounded. Water is then applied to the roof membrane to create an electric field on the roof. By using two probes, and following the readings shown in the potentiometer, the location of the breach (ground fault) can be found.
High-power ELD uses a similar approach but without the need to wet the membrane. In this instance, one lead from the pulse generator is connected to the deck and the other is attached to a device looking like a ‘push broom’ with copper bristles.
The operator then walks the roof. As the push broom passes over a breach, the circuit between the grounding wire and copper bristles will be complete and register accordingly on the operator’s equipment, thereby identifying the location of the leak.
You are right, because I personally did not devote time to maintenance of the roof of the house where I live, but scheduled maintenance of the car takes place once every few months. If you have no desire to spend on capital roofing work, it is better to take care of the roof in advance and carry out annual preventive maintenance. Now I will set reminders so that I don’t forget to check and I will monitor the work closely.