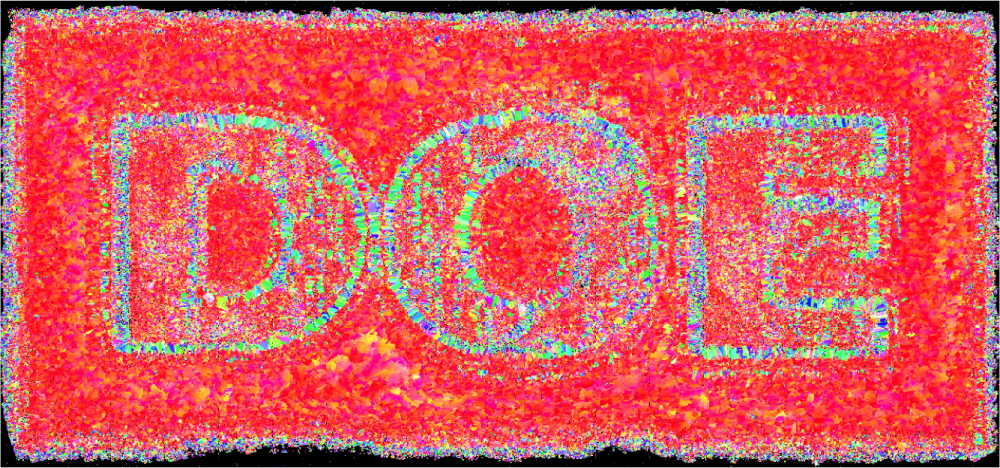
Researchers at the U.S. Department of Energy’s (DOE’s) Oak Ridge National Laboratory (ORNL) have demonstrated a way to control the structure and properties of 3D printed metal components with precision far beyond conventional manufacturing processes.
Ryan Dehoff, staff scientist at ORNL’s Manufacturing Demonstration Facility, explained this new management of local material properties will change the future of how metallic components are engineered.
“This manufacturing method takes us from reactive design to proactive design,” he explained. “It will help us make parts that are stronger, lighter, and function better for more energy-efficient transportation and energy production applications, such as cars and wind turbines.”
The researchers demonstrated the method using an ARCAM electron beam melting system (EBM), which involves fusing together successive layers of a metal powder with an electron beam into a 3D product. By manipulating the process to manage the solidification on a microscopic scale, the researchers demonstrated three-dimensional control of the microstructure of a nickel-based part during formation.
Being able to tailor this crystallographic texture would help alter a material’s physical and mechanical properties. Applications range from microelectronics to high-temperature jet engine components to construction materials.
“We’re using well-established metallurgical phenomena, but we’ve never been able to control the processes well enough to take advantage of them at this scale and at this level of detail,” said Suresh Babu, the University of Tennessee-ORNL Governor’s Chair for Advanced Manufacturing. “As a result of our work, designers can now specify location specific crystal structure orientations in a part.”
The full potential of 3D printing within design/construction applications continues to be a source of much speculation; at CONSTRUCT & the CSI Annual Convention in Baltimore in September, keynote speaker Pablos Holman examined the possibilities of 3D concrete-house-printing in China.