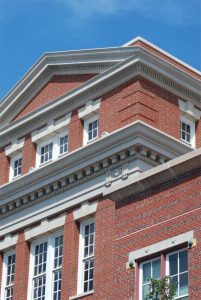
Principles and Precepts
While this kind of overcladding is an extensive project, it offers several attractive benefits: thermal performance and air tightness are significantly improved, helping eliminate moisture and condensation issues. In addition, overcladding can boost desirable acoustic isolation and attenuation. Properly executed, overcladding can also optimize the use of a masonry enclosure’s thermal mass. It can add decades to the structure’s service life expectancy without decreasing room sizes, as with interior façade stabilization and insulating options.
Specific considerations for façade overcladding approaches are like those for any retrofit of the enclosure assemblies that are predominantly masonry, including bearing walls and brick veneer. Design goals include:
• Increasing thermal performance;
• Providing an air and water barrier;
• Providing fire/smoke containment to enhance
building resilience;
• Modest costs and short design and construction schedules;
• Allowing building to be largely occupied and accessible during construction; and
• Limiting disturbance to occupant or tenant operations.
Another critical consideration is the retrofit approach should allow the limiting of overcladding system weight to stay below structural framing load capacities. Typical limits for steel-framed, masonry veneer systems, for example, would be about five percent of the dead load threshold for steel structural members, and 10 percent of building lateral loads.
Done well, overcladding will improve building aesthetics with relatively minimal impacts to occupants during installation. Green retrofit projects and building rehabilitations should be designed to tighten up the building envelope for better thermal efficiencies, not to mention dramatically reduced air and moisture infiltration. Overcladding options include energy-efficient insulated wall systems, silicone sealant and gaskets for glazed areas, new air and vapor barriers transitioning into window openings, and the sealing of all window-wall interfaces.
But where does one start? For example, how much insulation is required, and where should the vapor barrier be located? What are the benefits and disadvantages of overcladding for masonry assemblies? Good questions, and the project team should start with the basics, as a pioneering enclosure guru, the late Wagdy Anis, would say: heat, air, and moisture, or HAM.
Heat (and cold)
Overcladding, as with all enclosure design opportunities, hinges on climate. The climate zone will dictate many of the design choices, such as the location of air and vapor barriers. The building configuration and orientation and the local site’s topography, prevailing winds, external shadowing, and direct sunlight will determine the enclosure needs during both heating and cooling seasons. In all climates, continuous insulation is important—the insulating layer should not be interrupted by structural members or thermal bridges, such as metal elements that extend from the building interior through the insulation layer to the exterior. Thermal breaks at window frames, for example, ensure effective ci.
Project teams can use Building information modeling (BIM) models or U-value calculations to determine enclosure properties. Another option is the Simplified Building Energy Modeling (SBEM) calculation methodology, a national standard used to determine the energy efficiency of commercial properties. The methods allow project teams to evaluate heat flows and the overcladding design’s impact on energy performance. Variables include window-wall rations (WWRs), insulation levels and barrier types, use, and location.
Moisture
Water vapor in the air as well as bulk moisture must be addressed in the overcladding design. Rainscreen-type overcladdings drain behind the exterior finished wall, while barrier enclosures such as EIFS drain at the exterior plane. The chosen building overcladding application should balance moisture inside and outside the building, as well as allow the building and the enclosure assemblies to dry out. Moisture accumulation inside the building and within the enclosure should be offset by equivalent drying.
One concern for over overcladding is the potential for trapping excess moisture within the building but also within the enclosure assembly itself, for example between the new exterior cladding and the original masonry walls. To limit the negative effects of excessive condensation—which can lead to oxidation, deterioration of building materials, and potential mold occurrence—the project specifiers and architects should designers determine how much water vapor could be generated within the building and determine the resultant increase in internal vapor pressure above that of external air. After that determination, assess the performance expectations and physical properties of the enclosure assemblies.
Air
How much air should pass through the enclosure? More often, the answer is none. The air barrier should be continuous, structural, and uninterrupted. As Anis himself wrote in the Whole Building Design Guide, the enclosure and the overcladding layer should address three types of air leaks through an architectural enclosure:
1. Orifice flow, such as in a slit unintentionally left between a window rough opening and its frame.
2. Diffuse flow, such as through some brick or concrete block.
3. Channel flow, the common type of air leaks where “the air entry point and exit point are distant from each other, giving the air enough time to cool below its dew point and deposit moisture in the building enclosure.”
The issues of unchecked air movement also create moisture management problems since air carries moisture and water vapor.
Taken to together, these HAM principles advanced by Anis help to effectively design and specify overcladding for one of the most common challenges faced by long-term building owners: poorly performing and unattractive masonry walls. Failure modes in masonry façades where the masonry wall is supported from steel lintels begin with age alone and can be exacerbated by older practices such as missing or ineffective masonry expansion joints. Some cavity wall construction may lack thermal insulation, too.
Further inspection may reveal aging flashings and the use of parged cementitious coating on concrete masonry unit (CMU) as an air barrier. Thermally displaced masonry will result from the lack of expansion joints, which may be visible in brick façades. In extreme cases, these may impact glazing systems. Some exterior walls may not even comply with modern codes for resisting lateral imposed loads.