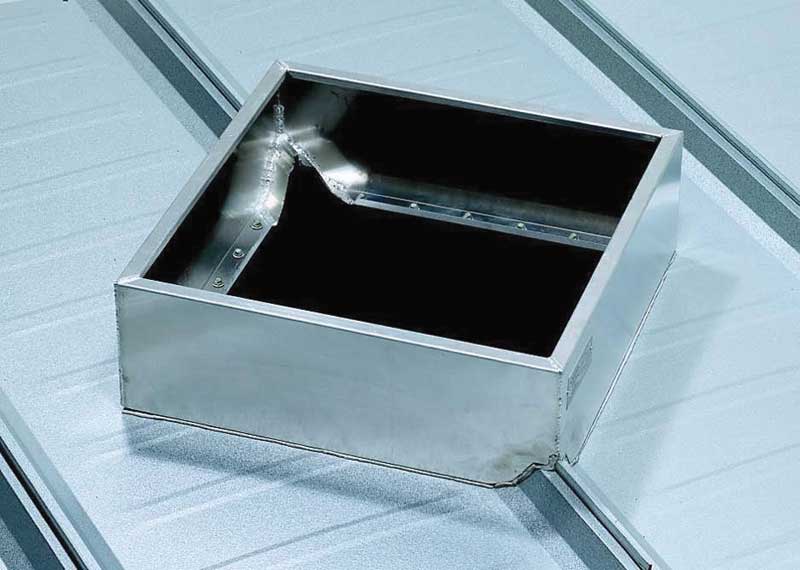
HVAC equipment
HVAC-related penetrations can range from being fairly minimal to extensive, depending on the building design and its heating and cooling requirements. Irrespective of the scope, it is critical that each penetration is correctly installed.
There are a couple of different approaches to installing HVAC equipment on a standing-seam metal roof. In applications where the curb for the HVAC unit encompasses all potential penetrations, the ductwork is inside the curb. The size of this unit is typically limited to 907 kg (2000 lb) or less and 1.2 x 1.8 m (4 x 6 ft) in size. These can still easily divert water around the base.
In applications requiring multiple curbs and penetrations for ductwork and related electrical requirements, larger HVAC units are often installed on racks or steel structures, as their size and weight prohibit employing a typical curb. This type of installation suspends the equipment 0.6 to 0.91 m (2 to 3 ft) above the roof surface. Electrical connections and ductwork, along with the structural supports (e.g. round pipes or wide flange beams), are then flashed accordingly.
Repairs for large HVAC units can be very challenging and expensive, often requiring the use of a crane. Therefore, it is critical to be thoughtful in how they are specified. In any case, best practices include specifying the curb be supplied by the roofing manufacturer and the work be completed by the roofing contractor.
Solar applications
Standing-seam metal roofs are strong options when building designs include solar panels. The preferred approach to minimize leaks is one that specifies the panels be attached to the roof using manufacturer-approved clips. These are designed to attach to roof panel seams with set screws, eliminating the need for fasteners or additional penetrations.
Mounting solar panel racking systems to the building’s support structures through the roof requires minimal penetrations, and leaks are often the result of improper installation of these supports or electrical work versus a problem with the panels themselves. These leaks tend to be fairly easy to repair. The same common practices utilized with suspended HVAC equipment should be employed and properly specified. Additionally, communication between the panel system installer and roofing contractor is critical.
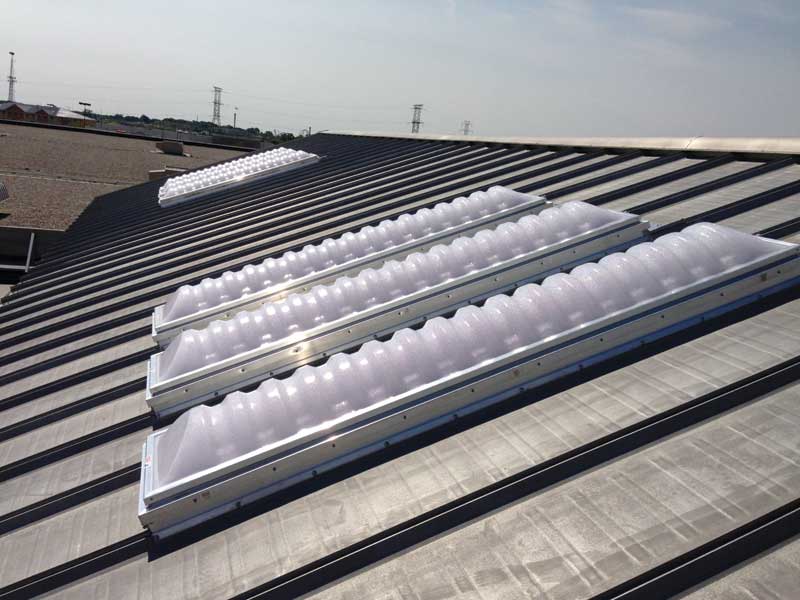
Daylighting
More and more building owners are opting for daylighting as facility managers are becoming aware of benefits like saved energy costs and increased employee productivity. Further, the International Energy Conservation Code (IECC) and American Society of Heating, Refrigerating, and Air-conditioning Engineers (ASHRAE) energy codes are mandating it. (Since standing-seam metal roofs are energy-efficient, they may help building owners apply for credits under the Leadership in Energy and Environmental Design [LEED] program for certain projects.)
Historically, either lite panels (translucent fiberglass panels with the same profile as the metal panels) or skylights and roof curbs were the most common daylighting solutions, but both created challenges in maintaining a weathertight assembly. For example, the warrantable service life for fiberglass is limited to 10 years—lite panels then become brittle and a significant safety hazard.
Skylights with curbs face similar challenges as roof-mounted exhaust fans, including possible panel deflection if proper secondary supports are not used. Additionally, when the specification is open or ambiguous, curbs designed for conventional built-up roofs (BURs) are commonly used. This is problematic because using improper curbs often lead to recurring leaks.
The good news is installing a daylighting system is no longer an open invitation for roof leaks. Recent innovations include seam-integrated or self-curbing systems that support prismatic domes. These systems use a design that has a diverter in the rear and a dome over the seam-integrated extruded aluminum rails to minimize leaks. This type of installation eliminates the need for secondary structural supports and moves the attachment point above the roof line to mitigate the chance for leaks.
Specifying a building employ a seam-integrated/self-curbing solution will help maintain a weathertight roof surface over the long term.