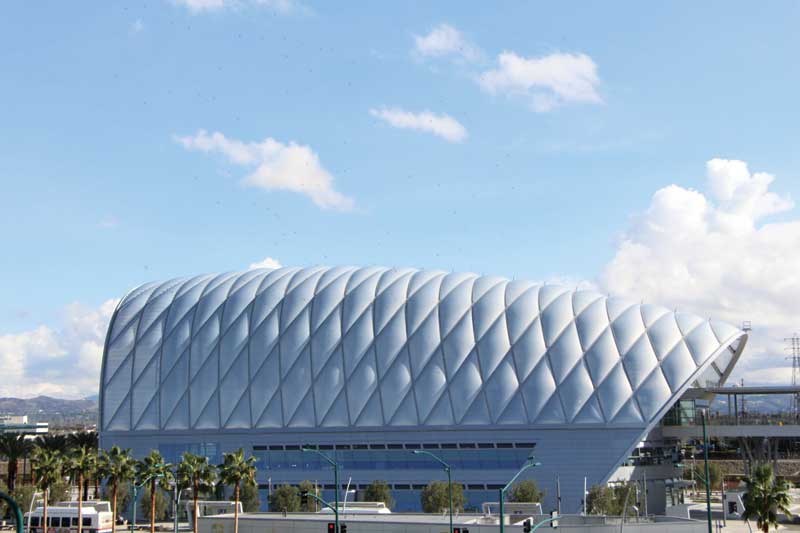
Most of the shop-applied coatings were spray-applied, while all the welded field connections were applied by brush and roller. The brush and rolled-on finish had to be blended carefully with the spray-on finish in order to create a seamless unnoticeable look.
The mockups also assessed whether the coating manufacturer could replicate the same color from one batch to another, explained coating consultant Tony Hobbs of TPC Consultants.
“Every cross-member on the structure is a weld, so there are hundreds of welds that required touch-up,” Hobbs said. “If we couldn’t replicate the same color from batch to batch, all those welds would stand out like a sore thumb. So quality control was a major consideration.”
At the construction site, welds were prepared in accordance with SSPC-SP11, Power Tool Cleaning to Bare Metal, primed with a single-component aromatic zinc-rich urethane coating, followed by an intermediate coat of low-VOC epoxy and a finish coat of a low-VOC modified polycarbamide coating.
The majority of the coating work on the superstructure was more than 30 m (100 ft) in the air—making it inaccessible by boom lifts or scaffolding. The job required highly trained and specially equipped coating applicators who climbed up from the bottom of the superstructure to the top and worked their way down using climbing gear attached to connection posts on the structure’s exterior.
Chris Radovich, NACE, SSPC, plant manager of Techno West, estimated the overall coating project took approximately a year to complete, which included the main superstructure, the glazing package at the main entrance, as well as an approach bridge, and all the stair towers. A six-person crew was responsible for touch-up work on the welded connections while another six-person crew applied field coatings to the ancillary items on the structure.
HOK’s Toossi credited the extensive use of building information modeling (BIM) practices with the design team’s ability to communicate with its clients and the public while aiding in the development of the project’s complex form, geometry, function, and asssorted sustainability objectives.
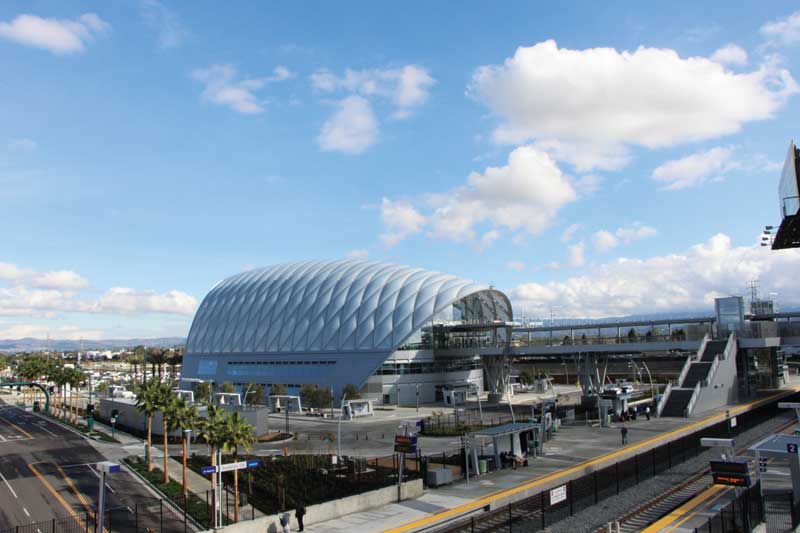
ARTIC has been recognized with numerous awards, including:
- the American Institute Architects (AIA) Technology Architectural Practice Building Information Model;
- the Orange County Chapter’s Eco-City Award;
- the American Institute of Steel Construction’s Innovative Design in Engineering and Architecture with Structural Steel Award;
- the American Public Works Association’s Project of the Year Over $75 Million;
- the Orange County Branch of the American Society of Civil Engineers 2014 Project Awards; and
- the Superior Performance in Real Estate (SPIRE) Project of the Year.
Conclusion
High-performance coatings formulated for long-term corrosion protection and aesthetic appeal can make or break a landmark construction project. With the right surface preparation, coating selection, technical assistance, and applicator coating systems help ensure the structure of concern lasts for years to come. In the case of both the Javits Center and ARTIC, the coating systems were installed as specified and will help extend the maintenance cycle of the two iconic buildings—protecting the steel above millions of visitors every year.
THE VARIOUS UNDERLYING RISK FACTORS FOR OVERCOATING PROJECTS |
Before a specifier makes a decision on whether to overcoat or completely remove an aged coating system on architectural structural steel, several factors must be considered—starting with the amount of corrosion.
ASTM International has published standard test methods for evaluating aged coating systems for rust and blistering.* Both test methods use photographic reference standards in determining the extent of corrosion and whether a coating system should be repaired or replaced. Total film thickness, the number of existing coatings, their adhesion to the substrate, and between coats are other overcoating risk factors. The number of coats and dry film thickness (DFT) of an aged coating system can be established with a Tooke gauge, or by visual examination of a paint chip cross-section. Testing for adhesion in accordance with ASTM D3359, Adhesion Tape Test, can establish whether an older coating system is at risk for delamination. Multi-coat, high-film thickness coating systems with poor adhesion between coats or to the substrate are high-risk candidates for overcoating. Adding coatings to an aged paint system will always increase the degree of cohesive stress exerted on the underlying layers of paint. The amount of cohesive stress varies with different types of generic coatings. Generally, non-flexible, two-component epoxies and aliphatic urethanes will develop more cohesive stress on curing than more flexible, one-component coatings such as acrylic emulsions, medium to long oil alkyds, moisture-cured urethanes, or epoxy mastics. The higher the film thickness, the greater the cohesive stress on the aged coating system, regardless of the generic type. Typically, flexible, low-cohesive stress overcoat systems are preferable in northern states where coatings are subjected to more freeze/thaw cycling stress. Test patches or mockups can determine the adhesion of the candidate overcoat system(s) to the existing paint system. ASTM D5064, Standard Practice for Conducting a Patch Test to Assess Coating Compatability, can be used as a guide when conducting test patches. One should establish the adhesion of the candidate overcoat system to the existing coatings using ASTM D3359 Method A.** Limitations on surface preparation are an important consideration when choosing an overcoat system, especially on interior spaces where abrasive blasting is unfeasible. Typically, cleaning with power tools is required to avoid interfering with other construction work. Overcoat systems with ‘dry-fall’ characteristics are available to help reduce the potential for overspray issues. Prior to applying any overcoat, all existing coating systems must be dry and clean, which can usually be achieved with power-washing. Rusty areas need to be power cleaned and spot-primed before an overcoat is applied. The edges of the existing coating system must be feathered to achieve a smooth transition prior to spot priming. In recent years, advances in power tools, surface cleaning media, surface profile media, and hand tools have made it possible to produce a surface profile with less extensive labor, even in high-rise locations and hard-to-reach areas. As is the case when selecting a coating system, the environmental service conditions are the most important consideration to make. One should consider, above all else, what exposure conditions the substrate will be subjected to before determining the necessary surface preparation and subsequent coating system. Notes ** The Society for Protective Coatings (SSPC) SP No. 11, Power Tool Cleaning to Bare Metal, can be found at www.scribd.com/doc/27681910/ SSPC-SP-11#scribd. |
Jennifer Gleisberg, CDT, is the architectural market manager for Tnemec Company Inc., where she provides sales support to Tnemec’s independent sales representatives. She is a LEED Green Associate (GA), a NACE Coatings Inspector (Level I Certified), and a member of The Society of Protective Coatings (SSPC), and the U.S. Green Building Council (USGBC). With more than 10 years of experience in the coatings industry, Gleisberg brings a customer service perspective to architectural projects requiring coating solutions. She can be reached at gleisberg@tnemec.com.
Choosing the right coating could make or break your building. Sometimes literally. Very informative post, thanks for sharing.