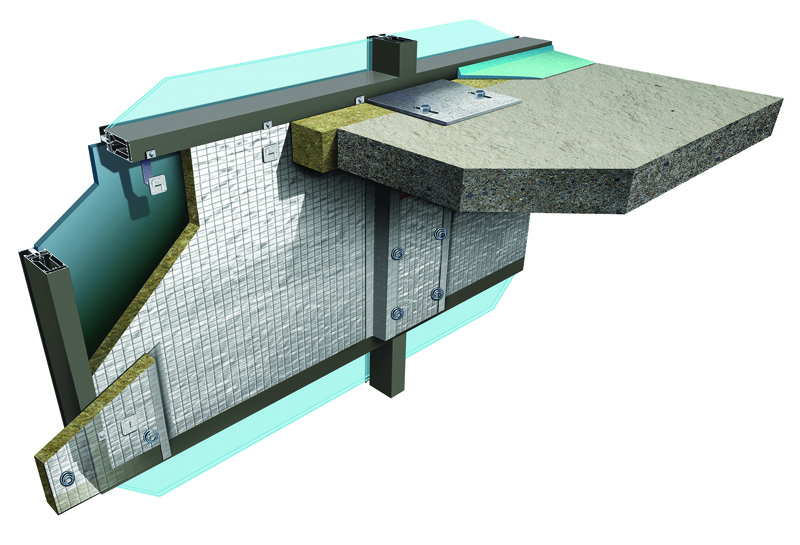
History of perimeter containment failures
There have been multiple cases showing what kind of damage can be done when fires move through improperly protected concealed spaces. In 1988, the 62-story Los Angeles tower, First Interstate Bank building, caught fire on its 12th floor. The fire spread to the 16th floor on the building after the combustibles in work stations ignited and rapidly grew. The exterior glass panels began to break, providing both additional oxygen and an alternate path for the fire to travel.
Flames spread through the gap in the joint between the floor/ceiling slab and the curtain wall. The fire vented through broken windows, first preheating combustibles on floors above before eventually igniting their contents. The building was being retrofitted with sprinklers at the time, but the system was not operational, so the fire was free to spread and grow. The fire was finally contained by firefighters after 3.5 hours.
On February 12, 2005, a fire started on the 21st floor of the Windsor Tower or Torre Windsor (officially known as Edificio Windsor) in Madrid, Spain. The building was a 32-story concrete building with a reinforced concrete central core. It was not sprinklered, and had been undergoing progressive refurbishment over a three-year period. The fire burned for 20 hours, spreading to all levels above the second floor.
At the time of construction, the Spanish building code did not require perimeter firestopping or perimeter columns and internal steel beams to be fire-protected. As a result, the original existing steelwork was left unprotected and the gap between the original cladding and floor slabs was not firestopped. In fact, these weak links in the fire protection of the building were being rectified in the refurbishment project at the time of the fire. Since the building adopted the ‘open-plan’ floor concept, effectively, the fire compartmentation could only be floor-by-floor (about 40 x 25 m [131 x 82 ft]). However, the lack of perimeter fire barriers in floor openings and between the original cladding and the floor slabs led to a failure of the vertical compartmentation, and the complete collapse of the building.
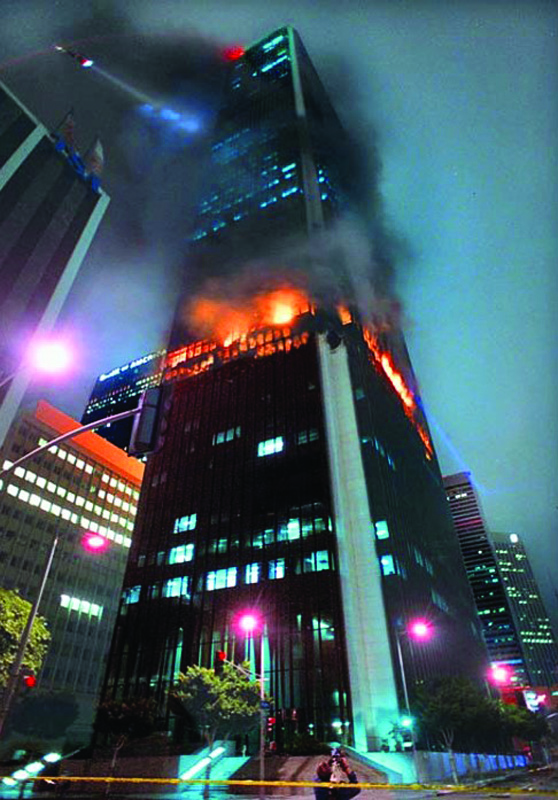
The challenges
A curtain-wall-clad building is a multistory structure having exterior walls not part of the loadbearing structure. As floor slabs are supported by interior beams and columns, there is a perimeter void or gap, typically ranging from 25 to 200 mm (1 to 8 in.), between each floor slab and the exterior curtain wall. Outside walls may be constructed using one of several materials, including glazing, light-gage metals, and gypsum wallboard.
The performance of a curtain wall during a building fire, or fire test, depends on the assembly being installed, but nonrated wall system performance significantly varies. Perimeter voids are generally hidden from view after construction. Once installed, these construction gaps are rarely inspected or re-evaluated unless renovations are made. They must be sealed to prevent spread of flames, smoke, and toxic gases in the event of a fire.
As mentioned, the intent with joint and perimeter firestopping is to confine a fire in the room of origin, preventing its propagation through the floor, ceiling, or walls. Mineral wool, with its high melting temperature, noncombustibility, and ability to retain its strength and integrity under fire conditions, is suited to protecting openings between fire-rated floors and rated or nonrated exterior wall assemblies. (For more, see “Why Mineral Wool?,” below.)
Some insulation materials, such as foamed plastics, melt or burn at levels far below the potential temperature of a structure fire. Flames inside a building can melt aluminum and copper, and cause steel studs and panels to buckle. The loss of these structural elements allows fire to escape quickly up the outside walls. Properly installed perimeter fire barrier systems, using mineral wool insulation, have demonstrated their ability to remain in place longer, and can prevent the passage of flame and hot gases between adjacent stories of a building.
Real fire experience has shown when there is ineffective curtain wall and perimeter void protection, a fire can spread through the space between floors and walls, and the window head transom and the cavity of the curtain wall, as well as through broken glass or around melted aluminum spandrel panels.
As a result, work began on the development of materials and systems to prevent fires from spreading through unprotected joints around the perimeter of floors. Part of the subsequent success of high-rise buildings is due to their perimeter fire containment systems. At every location where two components (e.g. steel beams or floor slabs) are located, mineral wool installed as a part of perimeter fire barrier systems is the key contributor that provides the critical fire containment.
WHY MINERAL WOOL? |
Due to the challenging nature of perimeter fire containment, mineral wool is suited to provide the necessary fire safety performance in fires. This form of manufactured vitreous fiber was initially developed in the mid-1800s by melting slag and spinning it into insulation for use in homes and industry. The term ‘mineral wool’ actually encompasses two products—rock wool and slag wool—that employ different raw materials in their manufacture. Rock wool is made from natural rocks like basalt or diabase, while slag wool is made primarily from iron ore blast furnace slag.
Production begins when natural rock or iron ore blast furnace slag is melted in a cupola furnace or pot. Once melted, this hot, viscous material is poured in a narrow stream onto one or more rapidly spinning wheels, which cast off droplets of molten material and creates fibers. As the material fiberizes, its surface may be coated with a binder material and/or de-dusting agent (e.g. mineral oil). The fiber then is collected and formed into batts or blankets for use as insulation, or baled for use in other products, such as acoustical ceiling tile, spray-applied fireproofing, and acoustical materials. Key points in the manufacturing process include:
Products made from rock and slag wool are extremely useful. They are noncombustible and do not support the growth of mildew and mold when tested in accordance with ASTM C665, Standard Specification for Mineral-fiber Blanket Thermal Insulation for Light-frame Construction and Manufactured Housing. Rock and slag wool fibers also are dimensionally stable and have high tensile strength. In addition to providing insulation, they absorb sound and, with a vapor retarder, help control condensation. The physical and chemical properties of rock and slag wool are major factors in their utility. As the fibers are noncombustible and have melting temperatures in excess of 1090 C (2000 F), they are used to prevent the spread of fire. As a primary constituent of ceiling tiles and sprayed fireproofing, rock and slag wool provide fire protection as well as sound control and attenuation. The excellent thermal resistance of these wools is also a major factor in their use as commercial insulation, pipe and process insulation, insulation for ships, domestic cooking appliances, and a wide variety of other applications. |