Polished concrete flooring projects surge
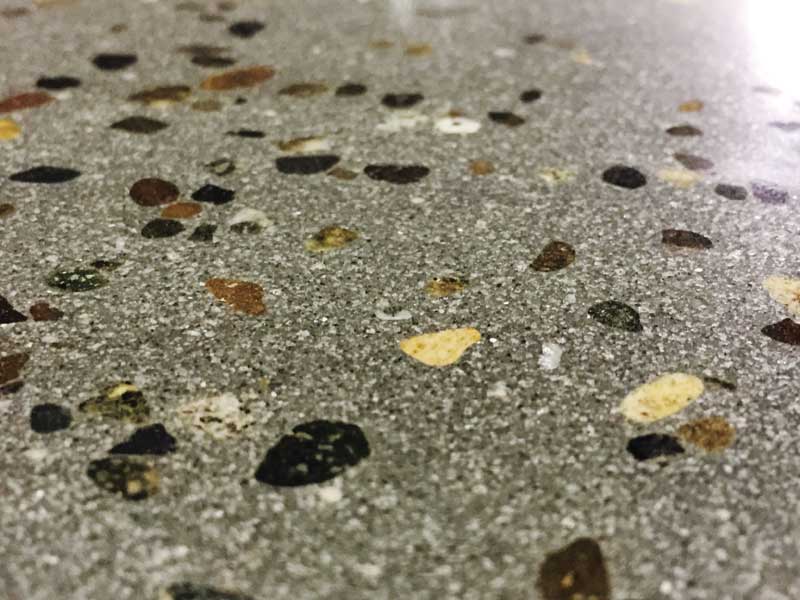
by Jose Ruiz
Projects throughout the United States showcase how construction materials are playing a supporting role in industries where new technology rollouts, tight timelines, and sustainable design are the new norm. Fast-setting, calcium sulfoaluminate (CSA) cement-based products are increasingly the key to achieving demands for both new and renovated construction.
Constant implementation of new technologies means less standardization across industries and greater uniqueness on the jobsite. Unfamiliar workflows and logistics, unusual jobsite conditions, and untried building systems are day-to-day realities. By investigating how materials can meet job requirements, projects can be completed to meet demanding timelines and damaged structures can be salvaged and restored to their original beauty.
Also referred to in the industry as ‘hydraulic cement-based,’ CSA cement products are increasingly becoming part of these jobs. They have provided architects and contractors with the ability to produce beautiful flat, polished floors in a fraction of the time, with considerably less expense, than using portland-cement-based concrete and constructing entirely new floors.
This article shares examples of unique jobs that used a variety of advanced high-performance fast-setting cement products to meet the needs of the project and its schedule.
CSA-based cement products
Portland cement has been the standard for many years, but it always brings certain challenges. It shrinks excessively, cannot be accelerated without negative effects, can be susceptible to attack by prevalent chemicals, and reacts destructively with certain aggregates. Using calcium products based in calcium sulfoaluminate cement can help solve these problems.
CSA cements are manufactured with similar raw materials, equipment, and processes used to make portland cement. The chemistry includes calcium sulfoaluminate (C4A3S) and dicalcium silicate (C2S). The C4A3S compound hydrates to form beneficial ettringite—a strong, needle-like crystal that forms very quickly to give the material its quick-setting and high-early-strength properties.
Another significant aspect of the chemistry is the absence of tricalcium aluminate (C3A), which would be present in portland cement and makes that material susceptible to sulfate attack. The fact CSA cement products have little or no C3A makes it very durable in sulfate environments.
When CSA cement is used in concrete, it provides superior performance in terms of rapid strength gain, reduced permeability, and low shrinkage. Traditionally, when fresh concrete is placed, the heavier particles settle and displace the mix water. The water then forms capillaries as it rises to the surface as bleed water. After the concrete has hardened, these capillaries become routes of entry for substances attacking the concrete and reinforcing steel. As CSA cement concrete is placed, the ettringite crystals rapidly consume water and create a three-dimensional lattice. This stops the settling and displacement process, eliminating capillary formation. The elimination of capillaries reduces permeability, resulting in more durable concrete.
CSA cement-based concrete is more efficient at using mix water than portland cement. This efficiency allows the placement of the concrete in a very workable consistency without the detrimental effect of convenience water. Portland cement will consume about half the mix water, leaving the convenience water to evaporate over time, causing drying shrinkage. At modest water-to-cement (w/c) ratios, CSA cement-based concrete will consume all the water in the mix, greatly reducing drying shrinkage.
CSA cement is a highly versatile material used to formulate mixes for a wide range of applications.