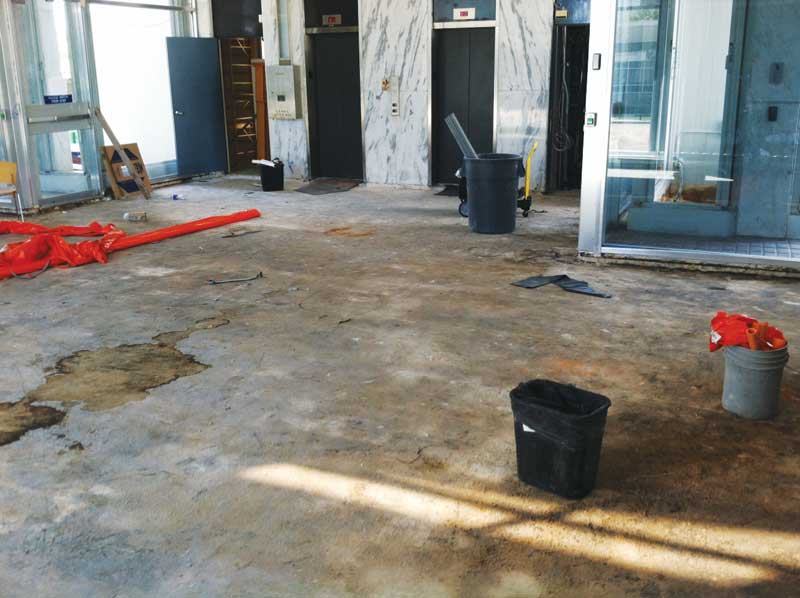
Photo courtesy Kemiko Concrete of Florida
Reviving a historic building
Every year, the National YoungArts Foundation receives thousands of applications from high schoolers who excel in the visual, literary, design, or performing arts. The foundation selects 800 of those students to attend its programs, work with master artists, and present their art on a national scale.
With such a thriving curriculum, the foundation was in need of a national headquarters. It acquired the Bacardi Tower and Museum buildings in Miami—two structures that were granted historic designations by the City of Miami Preservation Board. Renovations undertaken by the foundation, therefore, had a dual goal: create a multidisciplinary cultural center and preserve the architectural masterpieces. A key to maintaining the purity of the building’s modernist style was to achieve smooth, level interior floor surfaces with decorative polished overlay areas.
The seven-story rectangular tower—its well-known north and south walls adorned with painted murals comprising more than 28,000 blue and white tiles—underwent construction beginning in September 2013. To achieve smooth, level interior floor surfaces with decorative polished overlay areas, advanced high-performance fast-setting cement products were employed to both underlay and overlay the original floors. The use of these products allowed for the floors to quickly be leveled and polished without the time and expense of installing new floors. CSA cement achieves structural strength within hours and can be polished or receive a floorcovering the next day—a necessity for this project’s schedule.
The first floor was overlaid with a gray, integrally colored, CSA cement-based, self-leveling topping, resurfacer, and underlayment, and polished to a 1500-grit. The second floor required a CSA-based self-leveling underlayment (SLU) to raise the level of the floor to receive the polishable topping. The sixth floor was leveled with an SLU, in thicknesses ranging from 6.4 to 127 mm (¼ to 5 in.). A wood and epoxy floor system was then installed.
The underlayment was the foundation for the floor that received another covering, such as overlay, tile, or carpeting. (In this case, it was the gray self-leveling topping that was the overlay.) While there are different methods to polish an overlay, the recommendation was to mechanically diamond polish the floors to achieve the 1500-grit polish that would produce a mirror surface. A chemical applied and then buffed will not achieve the same level of polish. Engineers are typically specifying the polish process now to ensure the correct grit level of polish is achieved.
The products were mixed and installed using mixers, gauge rakes, and metal spike rollers. More than 1600 bags of advanced, high-performance, CSA cement products were used in total. The Bacardi Tower renovations were completed in February 2014 and now house the YoungArts Gallery, a restaurant, and staff offices.

Photo courtesy Industrial Concrete Services
Refurbishing floors for new use
In 1890s New York, the Terminal Warehouse Company’s Central Stores building offered ample storage for goods passing through the Chelsea District’s freight yards. Covering an entire city block, the building is in the process of being refurbished and already houses a variety of shops, galleries, and offices. The central ‘tunnel,’ which once provided ingress and egress for trains, will now be used as event space.
Concrete floors provide much of the chic industrial character for this venue, but they were badly worn and damaged in some spots. Paul Huneck, a specialist in decorative concrete and owner of Hudson Concrete in New York City, was called on to give new life to the surface.
To meet the needs of the schedule, CSA-based cement products were used. This allowed the floors to be polished after one day, whereas the contractor may have to wait at least 28 days with traditional portland cement, holding up the project.
First, a high-performance CSA-based concrete repair material was used to fill in deeply pocked areas. The floors were very uneven and needed to be repaired prior to application. Therefore, they were shotblasted between each lift to ensure the overlay would adhere. The process mechanically breaks up the weak areas of the concrete and then vacuums up the surface so it is clean and ready for the underlayment. (Generally, surface preparation should be to International Concrete Repair Institute’s [ICRI’s] Concrete Surface Profile [CSP] Level 3.) Approximately 600 bags of the mix were also employed to fill raised dais areas (e.g. platforms) that were being built into the new event space.
A total of three lifts of concrete repair products were needed to provide a smooth finished floor. Thirty-four kits of two-component, low-volatile organic compound (VOC), moisture- and alkali-insensitive epoxy primer were placed with a sand broadcast to create a textured surface and promote the adherence of each successive lift of product. A first lift of CSA-based SLU was applied to even out extremely low areas of the floor, followed by a second lift that completely corrected elevation discrepancies. In the end, 350 bags of this SLU were used. The same mechanical surface preparation of shotblasting was done between each layer to promote bonding. No testing was needed on this job—testing is only done if the original concrete is very soft or if there are oils spots on it.
A third lift of an advanced CSA-based topping with 325 bags of product was then used. It was mixed with a customized integral color and four different light-colored sand aggregates. To finish the surface, the floor was polished to a 3000 grit. A densifier and polish guard were then applied. There were no compatibility issues with these products since most densifiers and polish guards are formulated to work with all concrete types. Additionally, the densifier and polish guard had been previously used on this type of overlay.
The result is an expanse of beautifully polished floors with new life for their innovative use as an event space.