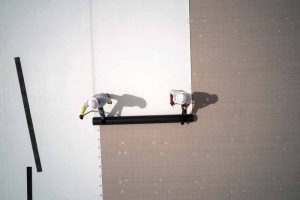
Polyiso is also the only foam plastic insulation product approved for direct application to steel decks to earn FM approval for Class 1 roof systems. This means the roof assembly with polyiso has successfully passed a series of tests which include external and internal fire exposure, wind uplift, water leakage, and impact resistance. As a result, polyiso direct-to-deck assemblies meet NFPA 276 (FM 4450) or UL 1256 standards and can be installed without a thermal barrier.
Reducing the environmental footprint
While one arm of sustainability is the efficient functioning of the material, the other is its impact on the environment. To fully understand a material’s footprint, it is important to account for greenhouse gases (GHGs) emitted during the entire life cycle of the material, from the extraction of raw materials to the disposal of the product.
Polyiso manufacturers recognize the significance of these comprehensive factors and attempt to minimize their environmental impact through product design and production processes to promote sustainability. Polyiso manufacturers put their commitment to sustainability into action in several compelling ways.
Transparency through EPDs
The Polyisocyanurate Insulation Manufacturers Association (PIMA) publishes third-party verified, ISO-compliant Environmental Product Declarations (EPDs) that provide industry-averaged environmental impact information for polyiso products manufactured across the U.S. and Canada. These cradle-to-grave reports cover the full product life cycle of polyiso insulation over a 75-year building service life, as specified in the Product Category Rule for thermal insulation. It includes environmental impacts from the supply, and transport of raw materials as well as the manufacturer, transport, installation, replacement (in the case of roofing materials), and disposal of polyiso products.
For roof applications, the EPDs are applicable to polyiso roof insulation manufactured with glass fiber-reinforced felt facers and polymer-bonded coated glass facers (ASTM C1289, Type II, Class 1 and 2). Similarly, the EPDs for wall applications are applicable to polyiso insulation commonly used in commercial and residential construction with glass fiber reinforced aluminum foil facer (ASTM C1289, Type I, Class 1 and 2). EPDs also available for polyiso HD cover boards manufactured with polymer-bonded coated glass facers (ASTM C1289, Type II, Class 4; CAN/ULC S704.1, Type 4, 5, and 6). These reports provide one piece of the sustainability puzzle, making it possible for project teams to make environmentally conscious decisions during the specification process.
Blowing agents that safeguard the environment
Blowing agents are often used in insulating materials to increase the final thermal resistance and facilitate the manufacturing of the foaming process. However, these agents come with a global warming potential (GWP). Manufacturers of polyiso insulation products in North America produced one of the first rigid foam insulations to be formulated using a blowing agent without chlorofluorocarbons (CFCs), hydrochlorofluorocarbons (HCFCs), or hydrofluorocarbons (HFCs). Instead, polyiso manufacturers use pentane or pentane blends in their production processes, which is a hydrocarbon with zero ozone-depletion potential (ODP) and a GWP value of less than 10 to ensure code compliance and reduce its environmental impact. In addition, polyiso products are available with other environmental certifications such as Underwriters Laboratories (UL) Greenguard Gold certification, which verifies those products meet or exceed UL’s standards for volatile organic compound (VOC) emissions.