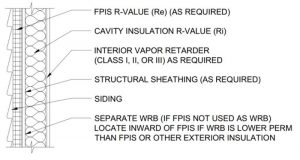
The ‘warm wall’ design approach described above is simple to implement and robust in the field. It controls the temperature of the assembly and promotes drying to the interior through the selection of an appropriate interior vapor retarder, such as interior latex paint, kraft paper, or various types of ‘smart’ vapor retarders. The warm wall design is based on a temperature-controlled design approach and, as such, removes the headache of attempting to control moisture purely by a traditional ‘water vapor permeance’ design approach. The downfall of the traditional method is it requires careful specification of the vapor retarder properties of each material layer on the interior and exterior of the assembly. For many materials, this property may be unknown or uncertain. It also attempts to walk a fine line between outward (wintertime) and inward (summertime) water vapor movement, which ends up cycling the assembly through seasonal periods of higher and lower moisture. Conversely, a warm wall design results in a stable and dry assembly year-round.
As energy codes continue to advance, the traditional vapor retarder design approach has become more and more challenging to reliably implement. Increasing cavity insulation levels can worsen the vulnerability to condensation or moisture accumulation by causing wood or gypsum sheathing materials to become colder (not warmer), resulting in condensation on surfaces.
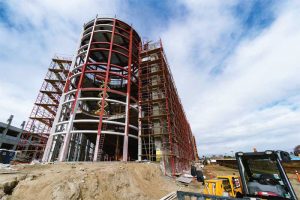
Photos courtesy Atlas Roofing Corporation
However, the use of ci for a warm wall design completely changes this challenge into an opportunity to leverage newer energy code insulation requirements in a way that also improves moisture performance. Fortunately, energy codes always afford specifiers the ability to use ci (alone, as in the perfect wall, or together with cavity insulation) whether it is offered in the code as a prescriptive option or not. Also, building codes are in the process of updating vapor control provisions to better coordinate with advancements in the energy code, such as in the case of the upcoming 2021 editions of the International Building Code (IBC), International Residential Code (IRC), and International Energy Conservation Code (IECC).
Below-grade vapor control methods
The discussion so far has been focused on above-grade wall applications, but what about below-grade walls? Well, the same principles apply, but in many ways, basements are easier because the climate below-grade does not change as much with the seasons. Basically, the ground is always moist and moderates the outside temperature year-round. The result is water vapor drives are always inward. Of course, the same high priority for liquid water control applies. All high performing basement walls start with:
- proper drainage of surface water (slope of grade away from building);
- drainage to remove any liquid water in the soil away from the foundation; and
- waterproofing the below-grade outside surface of the basement wall.
Nearly 90 percent of basement moisture problems are related to the failure to provide or maintain one or more of these crucial features.
For basements, the perfect wall concept also applies as the ideal solution. This simply requires the use of ci on the exterior side of the basement wall. However, for practical reasons, it is often optimal to use ci on the interior side of the assembly together with the water control strategies discussed above. These practical reasons include the need to protect the insulation (particularly above-grade portions) and the need to retrofit an existing basement (like the case study addressed in the next section). When insulating and finishing a basement on the interior side, it is important to be mindful of where the vapor retarder layer is placed. Ideally, vapor retarder should be layered directly on the interior surface of the block or concrete wall and should be water-resistant and insulating, like ISO ci, in order to protect moisture-sensitive materials. Consequently, wood framing, furring, gypsum, and water-absorbing insulation materials should be placed on the inside of the ci layer. This approach is consistent with the U.S. Department of Energy’s (DOE’s) Building America Program best practices for foundations.