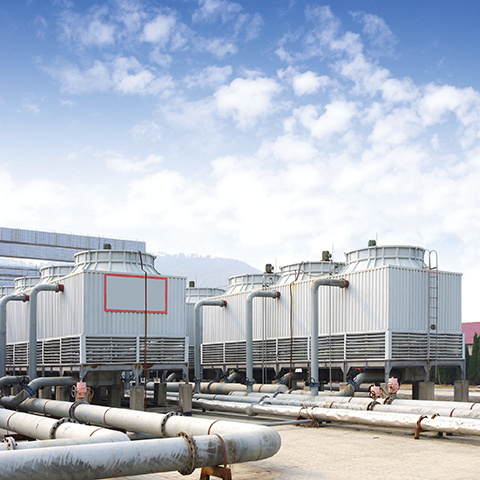
A poorly operating cooling tower reduces chiller efficiency and eventually leads to system failures. Most chilled-water plants have excess capacity, so one or more cooling towers are not operating during low-load hours. To make the most of existing cooling towers, condenser water can be run over as many towers as possible, at the lowest possible fan speed, and as often as possible.
Cooling tower fan motors are a major source of electricity use, as well as a generator of significant noise. Most towers are installed with a single- or two-speed motor. However, as the load on the cooling tower decreases, the fans might operate at a speed not necessary for that load, hampering energy efficiency.
Much has happened in recent years to give managers tools to improve motor efficiency. The federal government has developed energy standards manufacturers must meet. Replacing standard-efficiency motors with high-efficiency ones will reduce the energy requirements for that motor by two to eight percent. While that might not seem like a major improvement, depending on the motor’s horsepower and the number of hours it operates annually, energy savings can be significant.
The development of high-efficiency motors was only the first step. Premium-efficiency motors now meet even higher energy-efficiency standards and can produce even greater savings. A side benefit for both energy-efficient and premium-efficiency motors is to meet the energy standards, they require higher-quality components and more exacting manufacturing processes, resulting in a better motor.
High-efficiency motors can not only save money, but they can also make money. Some utilities offer rebates for installing these motors in new or retrofit work. In many cases, an upgraded motor can pay for itself in less than a year.
Upgrading with high-efficiency motors is a major part of the U.S. Environmental Protection Agency’s (EPA’s) effort to improve energy efficiency. Many resources offer comprehensive information on state, local, utility, and federal incentives that promote renewable energy and energy efficiency. Whether in a new design or an existing application, upgraded motors offer numerous advantages when used in cooling towers.
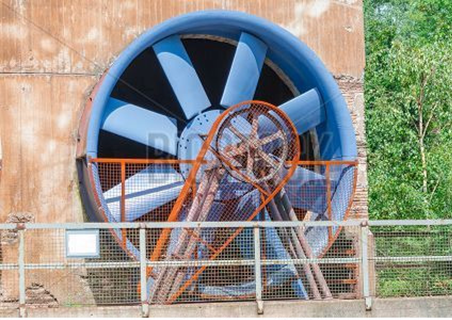
Government’s commitment
As part of the Obama administration’s effort to double energy productivity by 2030 and reduce carbon emissions in commercial buildings, the Department of Energy (DOE) recently announced $9 million to encourage investments in energy-saving technologies that can be tested and deployed in offices, shops, restaurants, hospitals, hotels, and other types of commercial buildings. The funding will facilitate the implementation of market-ready solutions across the United States to improve commercial building energy efficiency, with a goal of demonstrating upwards of 20 percent savings across various approaches.
Each year, the country spends $400 billion to power buildings—about half on commercial and industrial facilities—which is equal to half the energy in the U.S. economy. Reducing energy waste in these buildings—and doing so cost-effectively—will save more than $80 billion on energy bills annually.
The DOE’s Better Buildings Challenge, a cornerstone of the Climate Action Plan, is partnering with more than 200 organizations to shape aggressive goals to reduce energy intensity by at least 20 percent within 10 years.
Utility programs
Utility companies’ commercial rebate programs offer financial incentives for commercial, industrial, and agricultural customers to invest in energy-efficient technologies. Standard rebates are available for lighting, HVAC technologies, motors, and motor drives. Custom rebates may also be obtainable for other projects that will save energy, but do not fall into any easily identifiable category. Institutions, such as healthcare campuses, and business are eligible for rebates for virtually any project that can be demonstrated to consistently save energy.
A unique incentive program to Pacific Gas and Electric (PG&E) healthcare customers is the Healthcare Energy Efficiency Program (HEEP), administered through Willdan Energy Solutions. HEEP is an incentive program created to assist hospitals and other healthcare providers install energy-efficient equipment to reduce energy consumption and low operating costs.
Thanks for sharing this advice on having the cooling tower fans replaced to make the transfer of energy more efficient. I had no idea that changing the fan could even have such a huge effect even though they are a simpler mechanic of the tower. Plus, if the replacement fans are efficient enough to reduce costs, then I think it is worth it to at least investigate that option.
Thank you for all of the helpful information you give about cutting costs on energy and cooling. That being said, you talk about how using an electric motor for cooling towers runs the blades a low speed, which allows them to move large flow rates at a low pressure. This seems like a really easy and simple way to reduce costs and keep airflow efficient.