FAILURES
Deborah Slaton, David S. Patterson, AIA, and Jeffrey N. Sutterlin, PE
A recently completed multistory building was experiencing significant water leakage directly below the interfaces of rising walls at setback roofs during prolonged wind-driven rain events. The building was principally clad with 150-mm (6-in.) thick architectural precast concrete (APC) panels finished by the fabricator with a 75-mm (3-in.) thick mortar-set stone veneer placed in a random rubble pattern. Panel joints were specified to be 19 mm (3/4 in.) wide, while incorporating a two-stage joint design with the primary seal positioned at the exterior face of the APC panels, and the outer weather seal applied flush with the exterior plane of the stone. At the interface of the APC panels with the setback roof assemblies, the stone panels were eliminated and the APC panel thickened to 229 mm (9 in.) to accommodate installation of the roof flashing.
A surface-mounted metal counterflashing protected the leading edge of the single-ply roof membrane that was secured to the APC with a termination bar and capped with sealant.
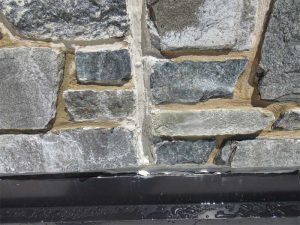
Photo © Jeffrey N. Sutterlin, PE
Diagnostic water testing resulted in leakage to the interior after a vertical panel joint at the base of the rising wall was subjected to the influence of the spray—leakage occurred within five minutes of testing.
Removal of sealant from the panel joint where leakage occurred during testing revealed the following:
- the panel joint was protected by a single line of sealant at the exterior surface of the stone rather than the two-stage sealant joint specified;
- the joint sealant was very thick because of multiple, unsuccessful applications of sealant to address ongoing water leakage; however, despite the depth of the sealant (which would reduce its movement properties), it appeared to be well bonded to the stone and mortar joints; and
- the stone veneer was installed such that a number of units extended beyond the edge of the APC backup, reducing the panel joint width and impeding installation of a primary seal at the face of the APC; the joint remained open at these locations.
Perhaps not too surprisingly, removal of sealant from other panel joints in rising walls where past leakage was reported revealed similar conditions. However, at joints where no leakage had been experienced, the joint was observed to be unobstructed and the primary seal had been installed continuously, providing the specified two-stage sealant joint.
The APC panels were designed to function as the water control layer for the exterior cladding. As such, primary seals for the panel assembly should align with the exterior surface, and be bonded to the edges of the APC panels to maintain continuity between panels. Secondary (or weather) seals are designed to align with the face of the veneer and protect the primary seal from exposure to the elements. At areas where leakage occurred, panel assemblies relied solely on the secondary seal to prevent water from entering the building, resulting in a cladding that was vulnerable to leakage, as water entering through the stone veneer had a direct pathway into the building via the open APC panel joints that were unprotected by a primary seal. Disregard for the project specifications and details proved costly because all sealant as well as some stone units adjacent to the joints had to be removed to facilitate installation of the primary seal to correct the noted deficiencies in the water control layer of the wall panels. Additionally, stone units extending beyond the edge of the APC panel needed to be resized before the reinstallation, and the counterflashing had to be removed and reinstalled, to ensure integration of the primary seal of the panel assembly to the roof membrane to maintain continuity between panel and roof water control layers.
The opinions expressed in Failures are based on the authors’ experiences and do not necessarily reflect those of The Construction Specifier or CSI.
Deborah Slaton is an architectural conservator and principal with Wiss, Janney, Elstner Associates (WJE) in Northbrook, Illinois, specializing in historic preservation and materials conservation. She can be reached at dslaton@wje.com.
David S. Patterson, AIA, is an architect and senior principal with WJE’s office in Princeton, New Jersey. He specializes in investigation and repair of the building envelope. He can be reached at dpatterson@wje.com.
Jeffrey N. Sutterlin, PE, is an architectural engineer and senior associate with WJE’s Princeton office, specializing in investigation and repair of the building envelope. He can be reached at jsutterlin@wje.com.