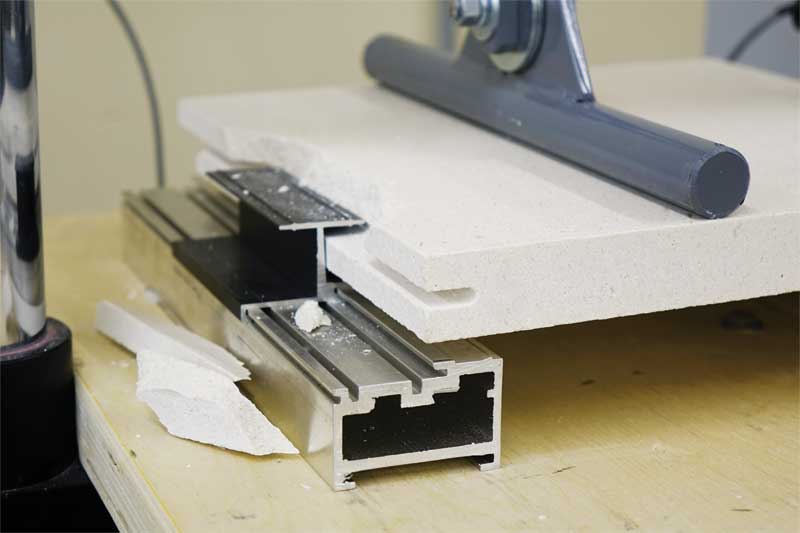
Photo courtesy The Natural Stone Institute.
by Charles Muehlbauer
Natural stone products have perhaps the longest history of use of any construction material. Their usage was often governed by empirical design methods because everyone was comfortable with “the way things were being done.”
Materials introduced in modern eras typically underwent more vigorous testing and engineering to prove their worthiness as a construction component. For example, the number of standards and test methods for the use of steel in construction far outweighs the ones for stone. One of the reasons for this is steel, having been used in construction for only a couple of centuries, needed those quality control (QC) assurances to gain acceptance in the industry. Stone, with several millennia of historic use, did not require a similar validation of its usefulness in construction.
However, stone construction methods have changed; the days of loadbearing masonry walls built with massive, cubic sections of stone are no longer. Driven by cost-reduction desires and energy-efficiency requirements, today’s stone cladding is usually quite thin, frequently in the 30-mm (1 3⁄16-in.) range. This thin shell of stone then needs to be attached to the structure of the building by one of two methods: adhesion or mechanical anchorage.
Both adhesive and mechanical anchorage are used and accepted. However, there are limitations on what can be adhesively attached. Adhesive attachment of any masonry unit is limited to products not exceeding 73 kg/m2 (15 lb/sf) unit weight, 0.5 m2 (5 sf) in unit area, and 0.9 m (3 ft) in either the vertical or horizontal dimension. Stone products heavier or larger than these parameters must be mechanically anchored to the building.
Surprisingly, on smaller projects of less than perhaps several hundred square meters, the capacity of these anchors may not actually get tested. This is particularly true when an engineer’s stamp is not required on the stone anchorage design. Similar to the spacing of brick ties in a façade, there are industry-published “rules of thumb” about how many anchors are to be used for a given area of stone panel.
For instance, Chapter 15 of the Natural Stone Institute’s (NSI’s) Dimension Stone Design Manual recommends using four anchors for panels up to 1.1 m2 (12 sf), and two extra anchors for every additional 0.75 m2 (8 sf). The recommendation is accompanied by a host of cautions, as it should be, since multiple anchorage locations on a stone panel do not always equate to uniform loading of those anchors, and there needs to be some discretion used in the selection and performance verification of the anchor in the stone. However, for someone applying a stone base course to a retail store front, following this rule of thumb is likely adequate. If the stone is being installed at higher levels or in regions of greater loads, building professionals need to get serious about verifying loads, anchor capacities, and safety factors.
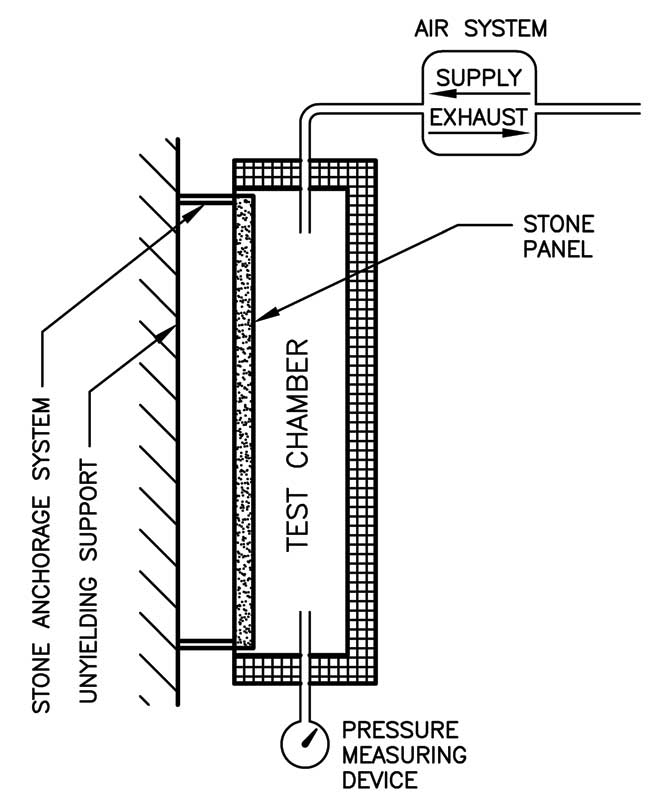
Testing stone anchorage
ASTM C1242, Standard Guide for Selection, Design, and Installation of Dimension Stone Attachment Systems, governs natural dimension stone attachments. This guide is written from the perspective of “best practices” as opposed to a “minimum practices” guide. It is also written with frequent usage of permissive language, as opposed to mandatory language. Therefore, much of the guide’s content is to be interpreted as suggestion rather than rule.
It is also unlikely it will ever be referenced in building codes, since they are always written in mandatory language and focus on minimum standards required for public safety, rather than best practices. Being a guide makes the enforcement of ASTM C1242’s content much more difficult, yet the document contains valuable information. It is one of the few documents with recommended safety factors for stone attachments.
Predictably, the recommendation is accompanied by a host of cautions and warnings saying the factors of safety may not be adequate in all cases, but they at least provide a starting point from which one can make modifications. The recommended factors of safety in ASTM C1242 vary greatly by the geological type of stone, as seen in Figure 1. It may seem alarming to some people to know travertine, for example, is recommended to have almost three times the factor of safety as granite. However, the recommendations are influenced by the variability of the stone and the concern of strength degradation over time. Sedimentary stones, such as limestone, travertine, and sandstone, are typically the most variable types.
Physical and mechanical test results in these stones will frequently have noisy data sets with large standard deviations. Additionally, there is no published test method within ASTM to assess degradation of strength due to weathering exposure. Both the variability of the material and the concern of possible degradation of strength over time are unknowns which the authors of ASTM C1242 have guarded against by recommending a high factor of safety.
There are two methods within ASTM to test stone anchorage. One is ASTM C1354, Standard Test Method for Strength of Individual Stone Anchorages in Dimension Stone. The other is a far more involved procedure titled ASTM C1201, Standard Test Method for Structural Performance of Exterior Dimension Stone Cladding Systems by Uniform Static Air Pressure Difference. ASTM C1201 was originally published in 1991, and the ASTM C1354 procedure did not arrive until five years later. This does not mean anchors were not tested prior to 1996, but that there was no standardized, published protocol for the laboratory to follow.