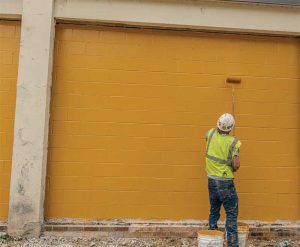
Self-adhered membranes
Self-adhered (peel-and-stick) membranes emerged in the last 20 to 30 years and have impressive flexibility and strong adhesion, often making them excellent around rough openings and other wall penetrations. However, if seams are not fully adhered or properly lapped, low permeable membranes can trap and hold water if moisture penetrates to the sheathing through the seams, accelerating the very problems of moisture-related decay they were designed to prevent.
Liquid- or fluid-applied membranes
Liquid-applied or fluid-applied membranes were first introduced around 2000s and create a continuous coating, tightly sealing the building against water and air intrusion without additional fasteners. Though more expensive than building wrap, these membranes are considered competitively priced due to their ease of installation. Liquid-applied barriers go on easily, and almost anyone can apply this type of product with a roller or sprayer. However, this can be a disadvantage.
With liquid-applied air barriers, it is important to have the right thickness (mil) on all areas of the building. This can be hard for a novice installer to achieve since there are coating thickness variations. Whether spray- or roller-applied, the wet thickness of applied material should be routinely checked and verified by the applicator to confirm proper coverage.3 If the milage is too thin, the barrier will not perform in the way it is designed, and reapplying over the thin spots adds extra labor and product consumption to the project. Contrastingly, if the coating is applied too thick, it can hinder drying time, affect performance, and increase labor and product costs.
Water-resistive barrier-air barrier (WRB-AB)
Integrated sheathing reduces the potential for installer error associated with field-applied water-resistive barrier-air barrier (WRB-AB) systems and offers a faster, easier installation process, and provides the protection of a continuous WRB-AB.
Products that integrate an exterior sheathing and water-resistive technologies to form a hydrophobic, monolithic surface, block bulk water but allow vapor to pass through, eliminating the need for an additional external WRB-AB. With the WRB integrated with the sheathing, contractors do not need to walk the building again with a wrap, and owners can feel confident in the coating’s uniform thickness and cure.
By removing an entire installation step, integrated systems save on installation time compared to traditional fluid-applied or building wrap methods. Crews can move on to the next job faster, and safety risks are reduced with fewer trades and less time spent on the job.
Understanding the codes
As air barrier products and systems evolve, so do building codes and testing standards. Just as air barrier systems are relatively new, building codes and testing requirements are new as well.
The most updated and frequently referenced building code appears in section C402.5 of the International Energy Conservation Code (IECC). The 2021 version of the code contains details for air barrier materials, building envelope performance, and testing—all of which vary based on building components, location, and building type.4
This, and all building codes are model codes only, and it is up to state and local governments to adopt them fully or in part. For example, projects in Washington, the United States General Services Administration (GSA), and United States Army Corps of Engineers (USACE) all require whole building airtightness testing, and each has its own standard of airtightness. Some different standards of include:
- 2015 IECC; 0.2 L/s•m2 (0.42 cfm/sf) at 75 Pa (1.57 psf)
- USACE; 0.118 L/s•m2 (0.2500 cfm/sf) of flow at 75 Pa (1.57 psf)
- Passive House Institute (PHI); 0.00085 to 0.0043 m3/min (0.03 to 0.15 cfm)
- Seattle Energy Code; 1.5 L/s/m2 (3.17 cfm/sf) at 75 Pa (1.57 psf)
The Air Barrier Association of America (ABAA) explains: “Airtightness testing is a process in which the building envelope is tested to quantify airtightness. The test measures air leakage rates through a building envelop under controlled pressurization and depressurization.”5 ABAA also notes testing is not mandatory or prescribed in building codes, but a performance-based option designers may require.
ABAA provides standard testing methods for building enclosure airtightness compliance (ABAA T0001-2016), for pull-off strength of adhered WRB-AB using an adhesion tester (ABAA T0002-2019), and for determining gap bridging ability of WRB-AB barrier materials (ABAA T0004-2021).6
ASTM indicates how to test based on building location and climate zone, and it can be performed on the materials or individual components alone, the assembly, or the whole building. The first and most basic testing is the material alone as indicated in ASTM E2178, Standard Test Method for Air Permeance of Building Materials, which measures the air permeance of flexible sheet or rigid panel-type materials and determines their suitability as a component of an air retarder system. Assembly testing, described in ASTM E2357, Standard Test Method for Determining Air Leakage Rate of Air Barrier Assemblies, is for wind pressure loading.
Materials can behave differently when tested on their own compared to testing within an assembly. For instance, most air barrier materials test well independently; however, it is the testing of the assembly and/or the whole building where most issues often occur.