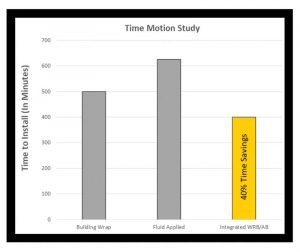
Scheduling and financial implications
Beyond QC measures, air barriers can either increase or decrease construction schedules and project costs, depending on the selected technology. Costs are driven by the price of product and the price of installation.
Labor costs are the primary differentiator since trips around the building require time and costs. Eliminating a trip around the building with an integrated system can provide a higher level of efficiency over products which must be applied on top of a sheathing. Reduced trips around the building translate to fewer components, less time for QC, and fewer areas to check and correct (Figure 1, page 47).10
Cure times and weather also factor heavily into schedules and costs. Cure times do not correlate to labor costs directly; however, it does impact costs and schedules if workers are on the clock but not engaging physically. Similarly, weather can impact installation times since peel-and-stick and other acrylic products cannot adhere to wet surfaces.
Passing the test
Once selected and installed, it is time to assess for air leaks. Identifying and testing for leaks can be a huge challenge. The most common sources of air leaks are areas where one section joins another section, such as fenestration systems, floor lines, parapets, and differing substrates (e.g. framed construction hitting block construction). When leaks occur, tests are used to find the source.
Testing options range from thermographic imaging, to finding cool spots where air might be moving, to smoke tests where smoke is released and creates a path to follow. Infrared tests provide a baseline awareness for areas of concern but can be limited since outside ambience can impact results. Smoke tests can be helpful but expensive for more finite testing, such as smaller air leaks where a fastener was not treated or a window seal with air permeance.
Blower door tests are often performed right after fenestration installation to check for an airtight seal between windows and the rest of building prior to painting and other aesthetic finishes. Blower door tests are also used as a primary mechanism for testing whole building airtightness.
If a project fails a whole building airtightness test, determining why it failed and how to pass becomes a top priority. Solutions vary based on the stage of construction at testing and where the leak occurs. With some such as, self-adhered membranes, the answer can be as simple as applying sprayfoam on the interior or from another part of the building.
Just as solutions to a failed whole building airtightness test vary, so do the consequences. Based on the project’s locale, consequences change since states are adopting different codes. If the project is in Washington, the certificate of occupancy will be delayed or denied. In other areas, building performance may be downgraded, such as a lower Leadership in Energy and Environmental Design (LEED) standard.