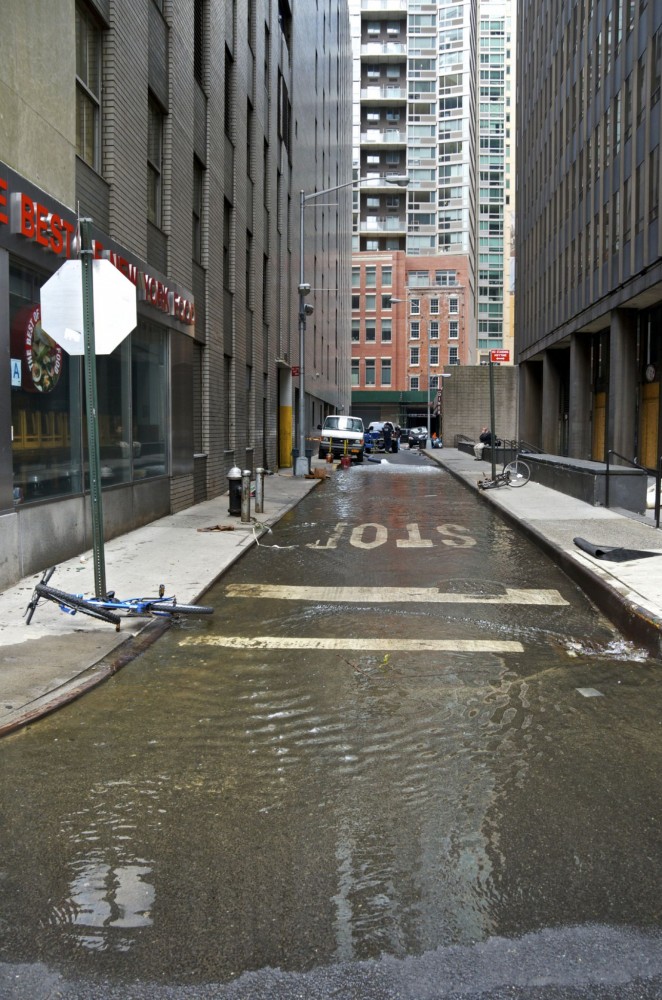
by Jeff Bowman, B.Sc., Greg Maugeri, and Sarah Rippin
Major flooding has dominated international news in recent years. While it may not be occurring more frequently than it was 50 years ago, due to growing infrastructure, the impact is certainly greater. Since 1949, the U.S. population has doubled, leading to a rapid increase in the construction of the urban environment. Most cities are unprepared for these rare increases in water levels—initiatives to protect infrastructure from major damage too often occurs only after the destruction.
Concrete is the modern world’s most commonly used building material, employed twice as much as other major building materials—steel, aluminum, wood, and plastic—combined.1 Concrete walls naturally protect against structural damage that can be caused by the effects of nature.
Looking back in history, many century-old structures stand longer than those erected in the last 50 years. This is largely due to reinforcement methods—instead of using solid stone, most U.S. infrastructure contains reinforcing steel embedded within poured concrete. As the priorities of construction methods shift to increase productivity and streamline scheduling, long-term durability often takes a backseat.
Feeling the effects of flood damage
In 2012, Hurricane Sandy ravaged the Atlantic coastline. The ferocious storm was among the worst disasters to ever hit the United States, causing tens of billions of dollars in damages and losses. The storm surged more than 4 m (13 ft) above the average low tide, leaving millions without power, causing severe flooding, and leaving properties destroyed.
One such flooded building happened to house the server farm for a well-known company’s global financial transactions. The server farm was located in a large warehouse building on West Street in Manhattan, more than two blocks from the Hudson River.
The most damaging issue in the storm’s aftermath was the street-level power plant running the server infrastructure was dramatically flooded. The mechanical room took 750 mm (2 ½ ft) of flooding during the hurricane, which was foreseen by neither owners nor builders when the servers were installed.
After the waters receded, engineers worked with waterproofing experts to come up with a way to protect the vital systems from potential flooding in the future. They opted to surround critical systems with waterproof concrete half-walls that could stand up to hydrostatic pressure.
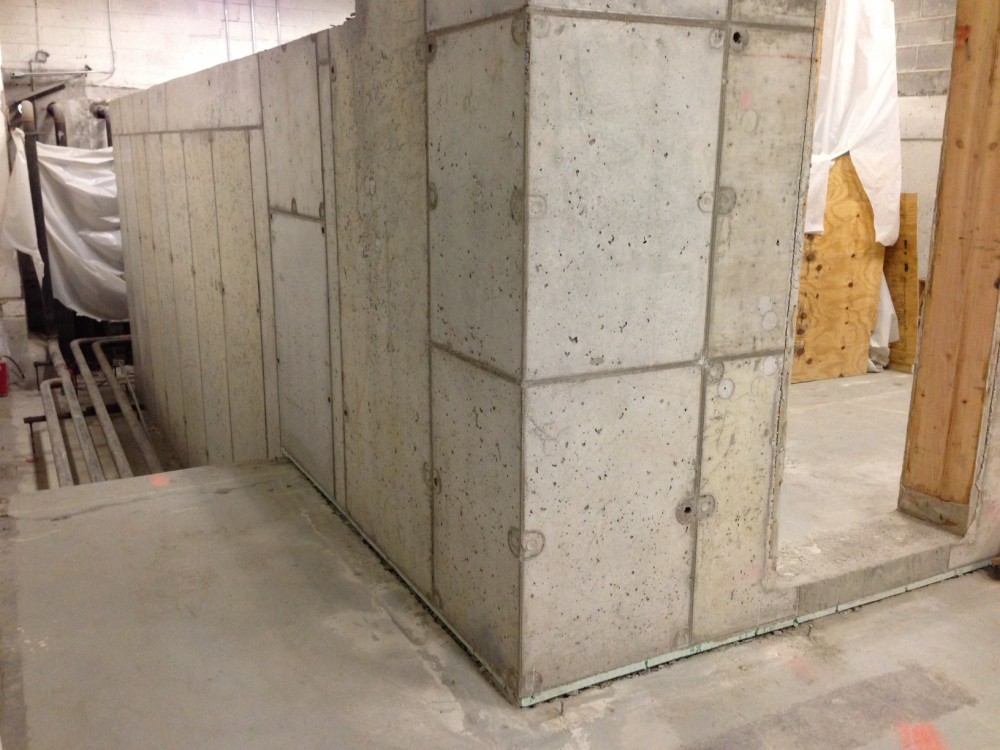
Even under normal circumstances, if soil around a below-grade structure’s foundation is saturated with water to 1 m (3 ft) or more above the ground level, the water’s force causes pressure on the concrete. The walls absorb the moisture like a sponge, leading to cracks and ensuing water infiltration, rebar corrosion, and mold. In a flash flood, similar water pressure is applied to concrete structures.
Waterproofing concrete from the inside out
The project team knew waterproofing the server farm would require a robust assembly that could withstand the sudden onset of a large volume of water. Typical concrete structures built in the past 50 years are waterproofed solely on the positive side (i.e. wet side) using surface-applied paints or membranes. These surface barriers are vulnerable to damage during construction, which can lead to waterproofing failure. In the case of the server farm, the water pressure of a flash flood (and the debris it carries) could damage a membrane and leave the servers vulnerable at the most critical moment.
The slow effects of water damage to an aging building can be accelerated by flooding, which adds force to aging materials and pushes moisture into concrete. This moisture stays within the concrete even after the building is cleaned up, and can cause mold and mildew growth over time. The moisture can also collect around the steel reinforcing rebar within the concrete, causing corrosion that spreads throughout the structure. Additionally, the rebar expands as it corrodes, cracking the concrete and adding to the deterioration.
To make concrete truly ‘waterproof’—which means both preventing water passage and resisting hydrostatic pressure—many contractors have embraced a long-term, permanent approach. Using an integral system, usually in the form of a powdered admixture added directly to the concrete itself, the entire mass of concrete can be made the waterproofing barrier. The system should include properties which work to protect steel from corrosion, saving structures which incur water damage fewer repair or replacement costs down the road.
In late 2010, the American Concrete Institute (ACI) published a new report on chemical admixtures for concrete called ACI 212.3R-10, Report on Chemical Admixtures for Concrete. This document contains a new chapter focused entirely on permeability-reducing admixtures (PRAs). Chapter 15 embodies research dating back nearly five years, with volunteers from across the industry spending countless hours and untold effort into its development.
The result is a valuable resource for concrete users, with the greatest value of the new chapter being its clear categorization of permeability-reducing admixtures into two divisions:
- permeability-reducing admixtures for non-hydrostatic (PRAN) conditions; and
- permeability-reducing admixtures for hydrostatic (PRAH) conditions.
Dampproofing admixtures
Used for PRAN conditions, dampproofing admixtures reduce water absorption via treatment with repellent chemicals (e.g. soaps or oils) or partial pore-blocking (i.e. fine particle fillers). Since resistance to water under pressure is limited or non-existent, these admixtures are not suitable for concrete exposed to this situation.
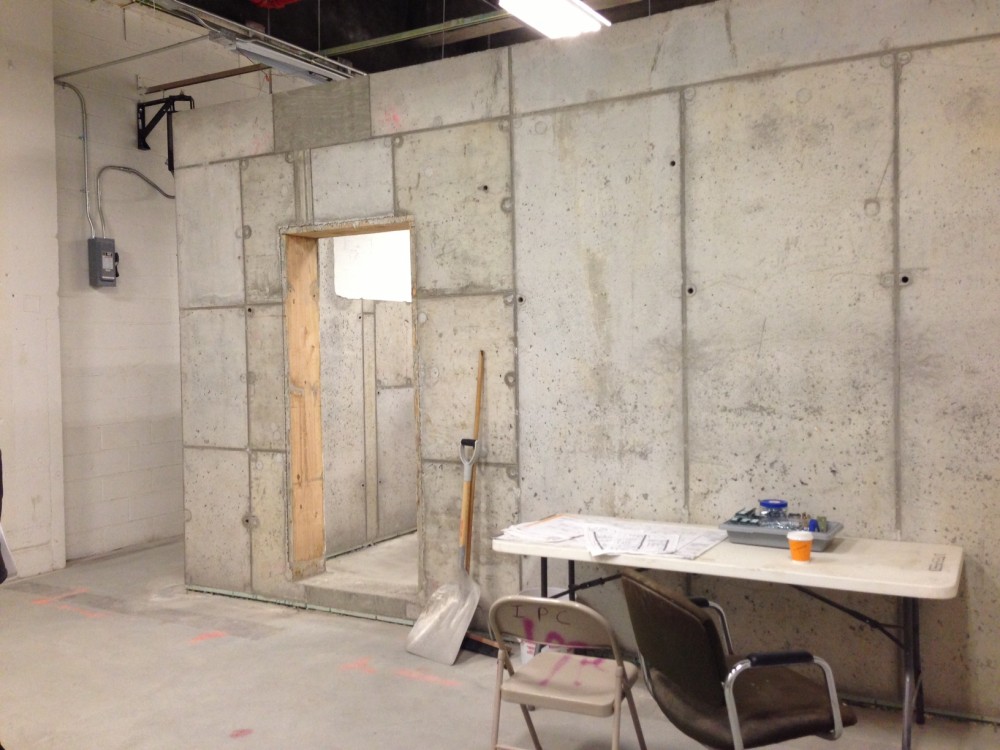
Waterproofing admixture
Waterproofing admixtures are specified for PRAH conditions. They reduce water penetration via a pore-blocking mechanism (e.g. crystalline growth or polymer plug). Given these materials are sufficiently stable to resist water under pressure, they are suitable for use in watertight construction, such as basements and water tanks.
Corrosion considerations
Not all flood damage to concrete structures is immediately apparent. Even after the water recedes, there is still a risk of rebar corrosion, especially if the flooding involved salty ocean water.
Corroded rebar can weaken a buildings vital support network, and the damage can quickly spread. Reducing water permeability effectively lowers opportunity for this, thereby increasing the structure’s longevity. Of course, not all corrosion-inhibiting admixtures (waterproofing or otherwise) are created equal.
The University of Hawaii recently released the results of a 10-year study on the corrosion of reinforced concrete exposed to a marine environment.2 Concrete panels were placed in the tidal zone of Honolulu harbor—a highly corrosive environment due to chlorides in the ocean water, as well as constant weather fluctuations.
Corrosion can be prevented in concrete in two primary ways. If the permeability of the concrete is very low, the penetration of water and chlorides will be minimized, preventing corrosive conditions from developing. Alternatively, the concrete can be treated with corrosion-inhibitors that act to chemically inhibit corrosion at the surface of the steel once corrosive conditions develop. For real projects, both methods can be used, but for research purposes only one additive was used in each test mix.
The Hawaii program used a good quality, control concrete (water/cement [w/c] ratio of 0.40) that would be considered durable. Even so, the control (i.e. plain concrete) showed corrosion induced cracking and rust residue after 10 years. The other materials evaluated included two supplemental cementitious materials (SCMs)—fly ash and silica fume—as well as four corrosion-inhibitors and three PRAs.

At the study’s conclusion, the report published in 2012 made the following recommendations to minimizing corrosion:
- Use a W/C ratio as low as possible, but not greater than 0.40.
- Include fly ash with at least 15 percent replacement of cement, or silica fume with at least five percent replacement of cement. Mixing must ensure the fly ash and silica fume, in particular, are well-distributed throughout the concrete.
- Include a calcium nitrite admixture at minimum dosages of 20 L/m3 (4 gal/cy).
- As added protection, consider including a proprietary hydrophilic crystalline product at two percent by weight of cement.
These findings are particularly relevant because they are based on field exposure in a harsh costal environment. This is the best type of testing because the exposure simulates the actual service conditions of a real structure. Laboratory tests are generally designed to provide accelerated results using conditions that do not always model real life. Many products may perform well in a short-term laboratory experiment, but perform poorly over the long term in actual conditions.
Wall joints and entryways
Certain water entry points are particularly sensitive when exposed to hydrostatic pressure. For example, water can easily penetrate through the joints where walls meet in a corner, or where the wall meets the floor. Tie-holes should also be treated as possible leakage points, and with a product that is effective under hydrostatic conditions, especially if in a below-grade location.
It can be difficult to predict how vulnerable a concrete joint is until it is too late, so it is important to mitigate any concerns well in advance by administering a permanent jointing system that can permanently withstand high water pressure, without breaking down and becoming an entry point for moisture.
Unsuspecting entryways are another issue. Insufficient waterproofing of the concrete is not the only way water can infiltrate an interior space during a major flood. In many cases—including the aforementioned building housing the server farm in New York—there are strong enough winds and water pressure to simply break through windows or doorways.
Boarding up these entrances is an effective protection measure in many cases, but this is time-consuming and, in some cases, impossible. Installing flood-resistant doors, gates, and window protectors upon the construction of the building helps ensure the structure can be protected quickly and efficiently when facing a flood.
If all entrances cannot be flood-proofed, protecting below-grade concrete from water damage from both the positive and negative side is a vital step in ensuring a building’s longevity.
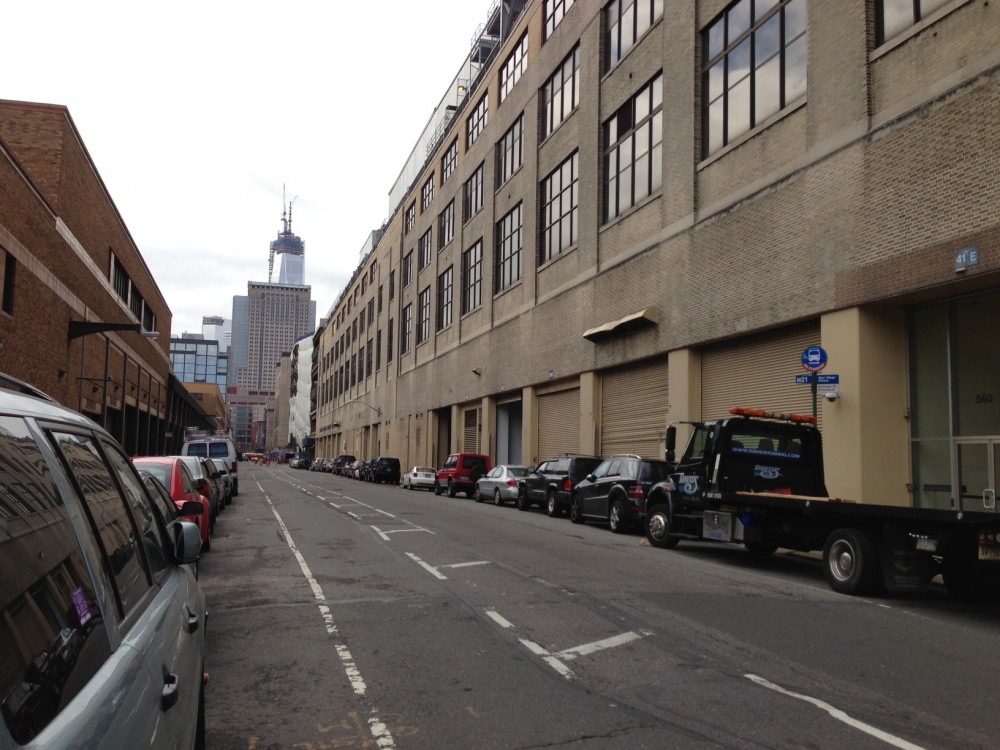
The concrete barriers, designed by engineers for the server building in Manhattan, contained a system that would work with water under pressure, rather than against it. Hydrophilic technology (from the Greek hydros, meaning water and philia, meaning friendship) absorbs water rather than repelling it, effectively using the water contact to its advantage.
This process is employed in crystalline admixtures and surface-applied cementitious crystalline products, which transform water into microscopic crystals. These crystals permanently block the pores of the concrete, preventing water from penetrating and moisture from remaining within the wall. As time goes on, the crystalline product remains dormant in the concrete, and reactivates upon the presence of moisture, throughout the entire life of the structure.
For the New York project, the finished wall took on crystalline waterproofing in three different applications:
- as an admixture added directly to the concrete mix;
- as a surface-applied brush-on (i.e. to the positive side—on the outside of the walls facing any potential water penetration into the building); and
- within the concrete joints as a two-part physical and chemical barrier.
By using these extra enforcements, engineers could guarantee the protection of this vital server farm should a flooding event at the level of Hurricane Sandy occur again.
Preparing for the future
With climate change and the increases in water-related damage to cities and areas around the world, it is becoming more apparent drastic steps need to be taken regarding the way we build, and the materials we use. In order to gain full insight, it is critical to pay attention to new innovations based on proven techniques, which reflect both sustainability and durability. Staying up to date with the new tools, research, and reports can help us to know what we can do to protect our structures from costly damage and early deterioration.
Notes
1 Visit cementtrust.wordpress.com/a-concrete-plan. (back to top)
2 For more see the report, “Performance of Corrosion-inhibiting Admixtures in Hawaiian Concrete in a Marine Environment,” by Joshua Ropert, MS, and Ian N. Robertson, PhD, SE. Visit www.cee.hawaii.edu/reports/UHM-CEE-12-04.pdf. (back to top)
Jeff Bowman, B.Sc, is a technical manager at Kryton International Inc. He earned his bachelor’s degree in chemistry from the University of British Columbia, and has extensive experience in the development and use of various construction products for the repair and waterproofing of concrete, specializing in crystalline admixtures and repair materials. Bowman has written numerous articles on waterproofing technologies and has contributed to international publications on this topic. He can be reached at jeff@kryton.com.
Gregory Maugeri is the CEO and managing partner of New England Dry Concrete, which specializes in solving cementitious waterproofing problems with crystalline materials. He has decades of construction and waterproofing experience; his company has been awarded the (ICRI) Project of the Year. Maugeri can be contacted via e-mail at greg@dryconcrete.com.
Sarah Rippin is a multimedia coordinator for Kryton. Over the past eight years, she has worked within the construction and marketing industries, and now uses both visual and written communications to promote and draw awareness to the importance of concrete waterproofing. She can be contacted at srippin@kryton.com.