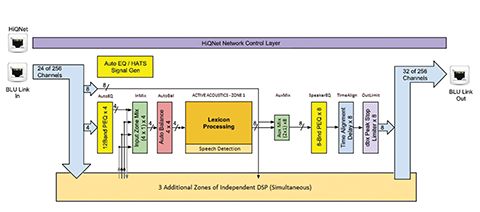
Site challenges
Before the active acoustic system could be installed, Neumann Auditorium presented a number of challenges. Background noise from the ventilation system and the pipe organ’s air compressor had to be considered in system programming and fine-tuning. The facility’s infrastructure was also carefully evaluated, which uncovered several complicating factors.
First, asbestos was found in the auditorium ceiling and under-balcony ceiling. The under-balcony ceiling asbestos was entirely removed, due to its relatively small size and easy access. However, the auditorium ceiling asbestos was left intact—this is because total abatement was prohibitively expensive, in part because of the 8.5-m (28-ft) ceiling. To minimize asbestos disruption, recessed speakers were not used in the auditorium ceiling. Instead, small holes were drilled in the ceiling for speaker mounts, with vacuums collecting any asbestos dislodged by the drilling.
Second, the auditorium’s side walls were discovered to be non-structural—insufficiently strong to support the four mounted sub-woofer speakers required. The auditorium was designed as a room within a larger building shell—a fairly common acoustical situation. To overcome this limitation, the sub-woofers were suspended from structural supports above the ceiling.
Third, the building’s electrical system needed an upgrade. The active acoustic system requires its own dedicated transformer with an isolated ground; this minimizes the potential for disrupting electrical noise. A motorized load-distribution center is also required to sequence nearly 20,000 watts of power to the signal processor and eight amplifiers with 64 channels of amplification. Sequencing helps prevent possible speaker damage from an electrical ‘pop’ or surge in the audio signal chain.
These electrical enhancements were made as part of a general upgrade to ensure Neumann Auditorium met current electrical codes.
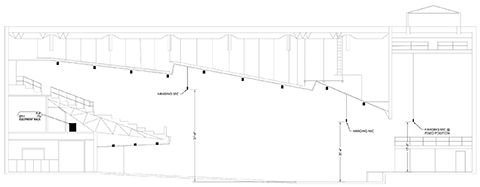
Installation procedure
Before the speakers could be installed, the final preparation step was temporarily removing all the auditorium seats. Doing so enabled unrestricted access for the motorized, articulated one-man lift used to reach the 8.5-m (28-ft) ceiling for wiring and mounting speakers and microphones.
These pre-installation site preparations at Wartburg spanned approximately one month. While installing this beta-site system took longer, similar future installations would be expected to require approximately two weeks, plus another one to two weeks for tuning the system.
Before arriving onsite, the installation company configured all system components—including amplifiers and signal processor—into a standard 2108-mm (83-in.) high rack and performed preliminary testing. Once at Wartburg, technicians situated this rack in a pre-selected location—a storage room located under the balcony. They also pulled the thousands of feet of necessary wire before installing 84 speakers in the auditorium: four sub-woofers located near the ceiling, 37 speakers on the walls, and 43 speakers in the ceiling.
To determine the proper number and placement of speakers, engineers utilized CATT-Acoustic software. By factoring in the auditorium’s dimensions, along with speaker specifications and coverage patterns, the software created a model space that helped locate optimal speaker positions. The number of speakers, in turn, influenced the number of amplifiers required in the system.
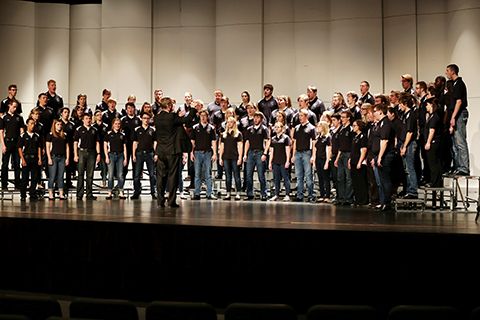
Microphone placement was also optimized for the auditorium’s unique programming needs. Unlike most performances that happen only onstage, Wartburg’s Christmas concert—the school’s largest annual event—also utilizes vocalists in the balcony. To accommodate the large orchestra at this concert, the first four rows of audience seating are removed.
While previous active acoustic systems required up to 30 microphones, Wartburg’s new-generation system only needs four—two above the stage and two over the balcony for the Christmas concert. All microphones are motor-controlled and drop into position when used; this eliminates possible visual distractions during projector use in the auditorium.
Initial skepticism
Nelson had been initially skeptical this active acoustic technology could deliver on its promises until visiting a rehearsal-room installation at Wayzata High School in Plymouth, Minnesota.
“In Wayzata’s orchestra room, I expected to hear sounds coming from the speakers,” explains Nelson. “That was my biggest fear—it would sound amplified. I didn’t want that.”
Once the Wayzata orchestra started playing with the system on, he stood as close as possible to a speaker, but could not hear it.
“I was blown away by the authentic sound,” Nelson says. “You can make it as acoustically ‘wet’ or as ‘dry’ as you want. I became excited about the possibilities.”
Nelson realizes the Neumann Auditorium’s situation with the Christmas concert made the goals unique.
“Most auditoriums would concentrate solely on the stage, but we truly use the entire space,” he notes. “[The team] rose to every challenge during the project and came up with some really creative ideas.”