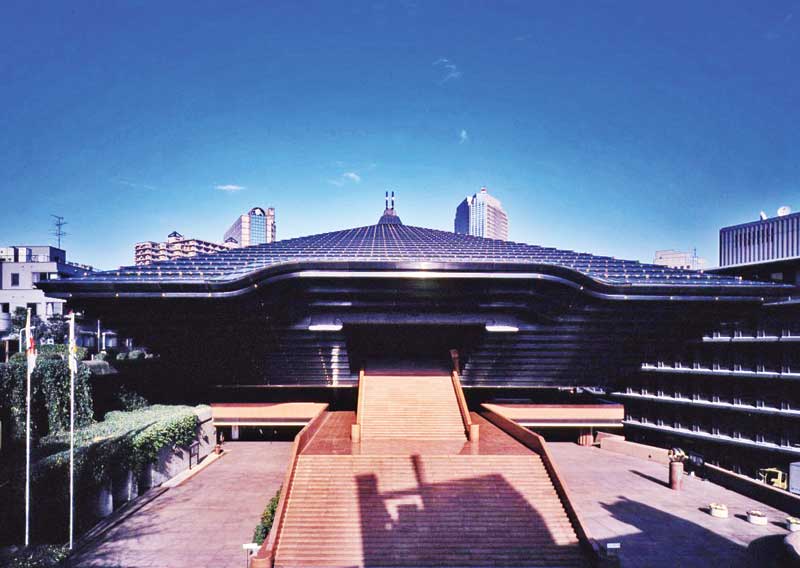
Photo courtesy JSSA
Avoiding material replacement
Corrosion or deterioration can lead to aesthetic or structural failure necessitating premature replacement. The first step in determining an appropriate material involves assessing the site environment to determine whether it would be corrosive. The specific environmental conditions that cause deterioration vary with the material, but include temperature, humidity, coastal or deicing salt exposure and pollution. This author developed the International Molybdenum Association (IMOA) stainless steel site evaluation, which is used globally.
One should also look at nearby buildings and structures to see how materials are performing, and ask questions about maintenance and replacement history. A material may look good because it is cleaned quarterly, but, if this level of maintenance is unlikely on your project, the product may fail. Applying the understanding of the environment, it is also important to determine whether material suppliers, industry associations, or consultants specializing in that product have long-term atmospheric corrosion testing data for a similar environment, since known corrosion rates are the best way to predict failure.
This author has written articles providing specific guidance on comparative metal selection in coastal and deicing salt, soil, and swimming pool environments. (Previous articles by this author for The Construction Specifier include “Designing on the Waterfront” [November 2007], “Stainless Steel for Severe Coastal Environments” [September 2011], “Architectural Metal Corrosion: The De-icing Salt Threat” [December 2006], “Preventing Corrosion in Soil” [April 2006], and a piece co-authored with James Fritz, “Swimmingly Stainless Pool Design” [December 2005]). Further, industry association website resources provide significant additional stainless steel selection resources. (Visit www.imoa.info/molybdenum-uses/molybdenum-grade-stainless-steels/architecture/stainless-steel-selection-system.php or www.nickelinstitute.org/en/NickelUseInSociety/MaterialsSelectionAndUse/ArchitectureBuildingAndConstruction/SpecificationSelectionAndFabrication.aspx for examples).
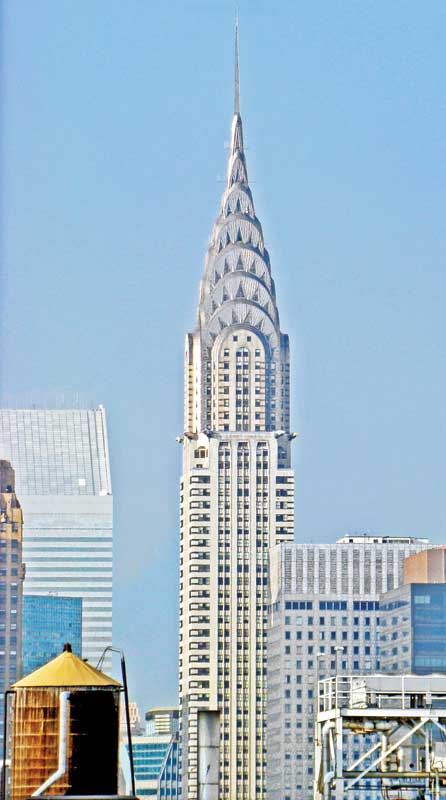
Photo courtesy Catherine Houska
The stainless steels most commonly used in architecture are:
- Types 304/304L (UNS S30400/S30403, EN 1.4301/1.4307, SUS 304); and
- 316/316L (UNS S31600/S31603, EN 1.4401/1.4404, SUS 316).
Duplex stainless steels are growing in popularity for structural applications. They include lean duplexes and UNS S32205 (which provides substantially more corrosion resistance than Type 316). There is a growing number of aesthetic finishes available for 2205 sheet. (See this author’s May 2015 The Construction Specifier article, “Duplex Stainless Steel Revolutionizes Structural Design.” Visit www.constructionspecifier.com).
With 60 percent of the world’s population living in coastal zones, increased use of deicing salts, and high pollution levels in developing countries, the corrosion resistance of Type 316/316L or comparable stainless steels is typically necessary unless there will be regular maintenance cleaning. In more-corrosive environments like the Middle East, high deicing salt exposures, coastal splash zones, and near volcanic areas, UNS S32205 and other higher-alloyed stainless steels should be considered.
Long-term performance
Stainless steel provides documented long-term performance with minimal or no maintenance in a wide range of service environments. The first known architectural applications for stainless steel date from the mid-1920s—they were relatively small or low-profile projects such as entrances and industrial roofs. Many of these early installations are still in service today, including the entrance canopy of London’s Savoy hotel (1929). (See this author’s co-written (with P.G. Stone, and D. J. Cochrane) Nickel Development Institute reference book, Timeless Stainless Architecture, from October 2001). This illustrates the durability and longevity of stainless steel. When properly specified and maintained, it can last the life of the project. When demolition finally occurs, an average of 92 percent of the stainless steel used in construction is recycled back into new metal—an indefinitely recyclable resource—without deterioration of properties. (For more, read Barbara Reck and T.E. Graedel’s May 2013 internal report for the Center for Industrial Ecology Yale University, “Comprehensive Multilevel Cycles of Stainless Steel in 2010 Final Report to the International Stainless Steel Forum (ISSF) and Team Stainless”).