FAILURES
Craig A. Hargrove, AIA, LEED AP, and Tai Mahmuti, PE,
To provide personalized temperature control, while maintaining low initial costs and simplified installation, hotels and dormitories often use packaged terminal air conditioning (PTAC) units. However, penetration of façade systems with PTAC units compromised by poor detail design and/or improper installation has led to water infiltration and moisture-related problems.
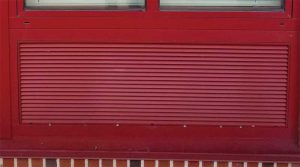
Photos courtesy Hoffmann Architects
PTAC units are factory assembled, provide heating and cooling to a room or area, and do not require connection to the building’s central heating and cooling system. The units are usually installed through the exterior wall or fenestration framing with a sleeve mounted in the opening (typically made of metal) and a louver on the exterior face. The louver allows for air intake and exhaust, while shedding moisture away from the interior of the sleeve. However, louvers are often not designed to stop wind-driven rain and can admit water inside the sleeve requiring drainage, either through weep holes or internal drains.
PTAC manufacturers typically do not provide waterproofing details to incorporate their units and wall sleeves into a specific building enclosure system. Likewise, construction drawings often have an insufficient level of detail to ensure a weathertight connection between the PTAC unit and the wall assembly. Exclusion of fundamental waterproofing details and/or poor installation can contribute to water leakage at PTAC units.
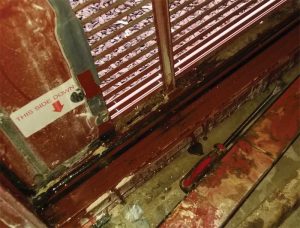
In the illustrated example, the window-wall system was modified by the manufacturer during design and fabrication to include an oversized louver with weep holes set flush with the windows above, to match PTAC ventilation to the façade profile. After the panelized window-wall system was installed on the façade, a different trade constructed an undersized wall sleeve abutting the louver, with butyl tape sealing the perimeter. Shortly after completion of construction, water leaks appeared on the inside of the building, and an investigation by a third-party determined the weep holes of the wall sleeve did not align with the weep holes of the louver. Further, the PTAC sleeves were installed back-pitched, so the water in the sleeve could not drain to the exterior, resulting in interior leaks.
As a repair, additional weep holes were drilled through the louver frame, and a liquid-applied waterproofing membrane was installed to positively slope and drain the sleeves. The new weep holes, however, were over-drilled, creating an opening between the window and louver frames and forming a path for water to infiltrate the glazing pocket. Eventually, the window-wall glazing pocket overflowed, resulting in additional water to the building interior.
To minimize the potential for water infiltration at PTAC units, coordination among the design team, manufacturers, and the trades involved is necessary. Construction documents must include proper waterproofing details at wall penetrations, as well as water management systems. Other items to consider may be thermal bridging, bird protection, and snow buildup.
The opinions expressed in Failures are based on the authors’ experiences and do not necessarily reflect those of The Construction Specifier or CSI.
Craig A. Hargrove, AIA, LEED AP, is senior vice-president with Hoffmann Architects, Inc., and manager of the firm’s New York City office. He may be reached at c.hargrove@hoffarch.com.
Tai Mahmuti, PE, is project engineer with Hoffmann Architects in New York, specializing in structural design and detailing of the building enclosure. He may be reached via e-mail at t.mahmuti@hoffarch.com.