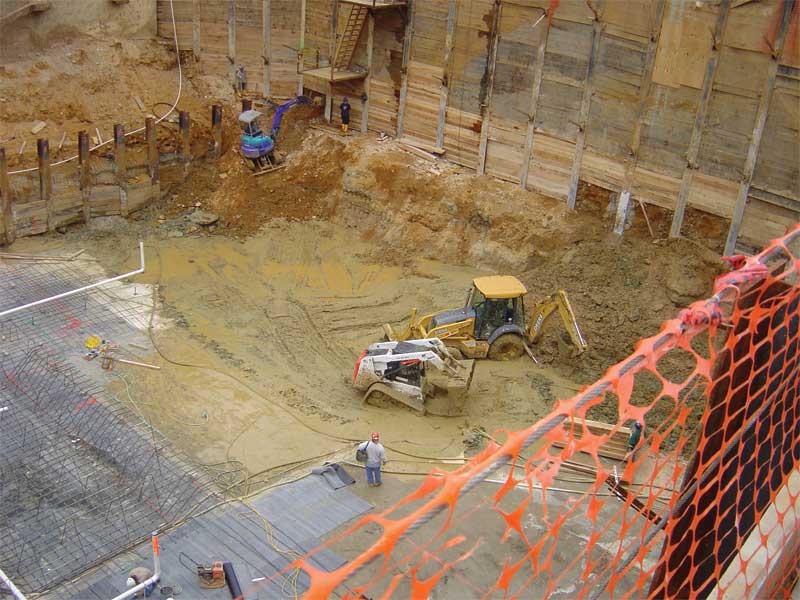
Inspections
To ensure the quality of work during construction, there should be adequate inspection, meaning field verification of design intent. Where full-time inspection is not practical, both the schedule and approximate percentage of part-time inspection should be established. Such an inspection of the installed waterproofing must be conducted prior to any concrete pour or backfill placement. Inspections should be scheduled close to the concreting or backfilling, but still allow enough time for correction activity to repair or replace any damaged or nonconforming waterproofing. Backfill soil compaction requirements vary by waterproofing material type so the inspection process should take into account the manufacturer’s guidelines for the specific system being inspected.
The project team should ensure the selected inspection firm is a reputable company with qualified personnel trained by the waterproofing manufacturer. It is also important to make sure the company is hired by the owner and not the contractor or waterproofing subcontractor to eliminate conflict of interest.
If the proposed personnel are to cover more than one area of expertise, it should be determined there will not be a conflict in scheduling the inspections. The duties, responsibilities, and authority of the inspector should be clear and definitive, including the power to stop work as a result of adverse site conditions and nonconformance material installations. The inspector must have a booklet or electronic notepad of all waterproofing details approved for the project to use as a reference in the field for verifying in real-time if the waterproofing materials have been installed as per project requirements.
A good practice is to require field inspectors be trained and certified by the manufacturer. Too many times this author has seen people conducting field inspections of materials they were not specifically trained to inspect, and thereby missing obvious nonconformities in the project.
Inspections conducted by the manufacturer’s sales staff should also be avoided or limited because of the perceived bias or conflict of interest with the waterproofing subcontractor.
It is also important to note the independent inspector is not intended to replace or substitute for the “internal” inspections by the contractor and waterproofing subcontractor. It is the duty of those executing the work to systematically check their work is meeting project needs. Subcontractors can be mandated to notify the main contractor—in writing—when waterproofing is damaged during work, so the system can be repaired prior to backfilling.
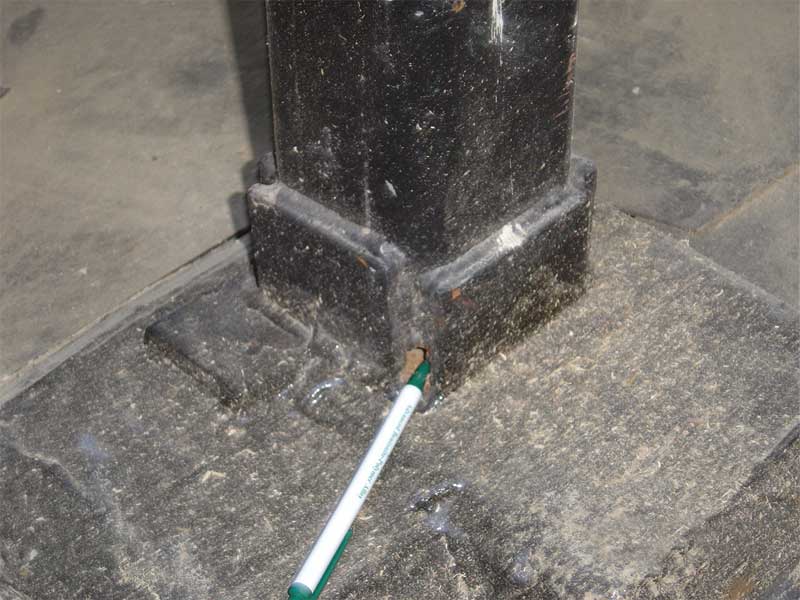
Rarely do manufacturer’s typical details include all of the conditions that will be encountered. Job-specific details should have a unique number listed on the document as well as indicate the specific project. One must not depend on subcontractor-prepared shop drawings; pass all job-specific details through a and the consultant, prior to being approved by the designer. If there is no approved detail, an inspection cannot be conducted to verify conformity.
Substrate inspection
Poor substrate preparation can impact the performance of any waterproofing system. Inspection of the substrate ensures suitable dryness, texture, and soundness. With property-line retaining walls, it is extremely important
to define/provide acceptable guidelines, not just state the shoring wall shall be “structurally sound.” For example, with soldier pile and lagging, the interior face of the lagging timbers should be monolithically installed to provide a “flat” surface, and maximum allowable gaps between timbers specified. Requiring all the voids and cavities behind the lagging be filled with compacted soil or cementitious grout is also recommended.
Timber lagging placed on the outside flange of soldier piles should be avoided, especially in hydrostatic conditions. This orientation of shoring wall support typically results in the waterproofing membrane being installed intermittently whereby it is actually installed in separate defined segments terminated between each soldier pile. This creates what basically amounts to a penetration through the membrane extending the depth of the excavation.
Inspection reporting
Inspection reports should be completed and submitted promptly to all applicable parties as established in the pre-con meeting. This is just as important as the onsite inspection itself. Quick distribution of the reports allows all parties to review it while still having the opportunity to take corrective action on any nonconformance. Sometimes inspectors must submit a report internally to a supervisor or an engineer for review before distributing it. This can cause delays if the supervisor does not act promptly.
Some manufacturers have dedicated staff specializing in inspection-report reviews. This staff performs a second review. Typically when this second layer of review is undertaken by a manufacturer, additional nonconformance may be identified. These must be communicated promptly to all applicable parties
for corrective actions. Manufacturers having this additional review process as part of their warranty eligibility are truly engaged in a quality assurance program. Beware of manufacturers stating they offer the same “warranty” but do not have this second review process.