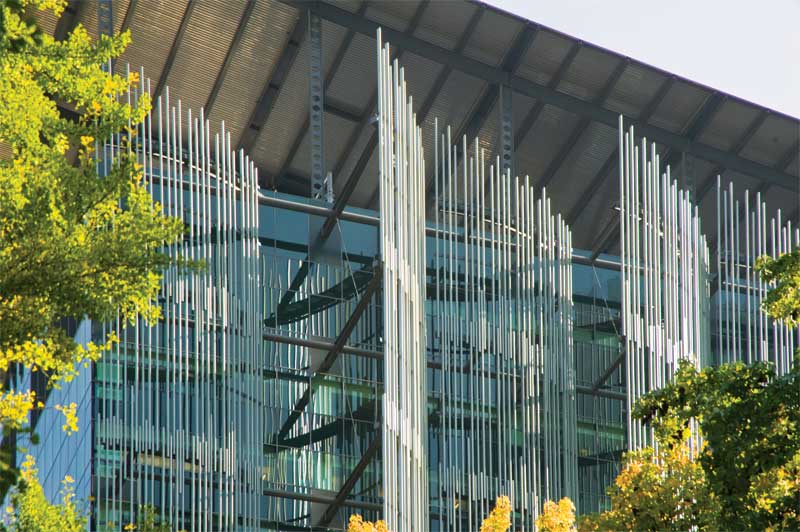
Photos © Brett Drury. Photos courtesy PGE
Pursuing third-party green certification due to concern for the environment and the health and well-being of tenants is not the only consideration, although it is of paramount importance. Owners may benefit financially as well. Several studies have demonstrated LEED-certified buildings may demand higher rents and increased market value. (For more, see articles from Bentall Kennedy Group or San Diego Union Tribune—respectively, www.bentallkennedy.com/news-2015-10-06.php and www.sandiegouniontribune.com/business/growth-development/sdut-green-buildings-outperform-vacancy-rental-rates-2012sep05-htmlstory.html.)
Being able to demonstrate the business and financial benefits of their green building investment is important to owners. Measuring energy efficiency and energy savings in retrofits is one obvious solution, as is achieving LEED certification. However, ‘soft’ measurements also can be of value. For example, asking employees and tenants through surveys specifically about the building’s green initiatives (e.g. thermal comfort, daylighting, and ventilation) may provide anecdotal evidence a green building offers a more pleasant work environment.
Owners and developers who do try to quantify the impact of healthy buildings report improved employee satisfaction and engagement, the ability to lease buildings quicker, and a potential positive impact on the building’s market value.
Conclusion
Determining the optimal combination of building performance and functionality depends heavily on the building’s fenestration system. In turn, the fenestration heavily depends on use of highly engineered framing to meet structural challenges, as well as current and foreseeable stringent energy codes. Aluminum provides the sustainability, structural integrity, and inherent beauty to do the job well.
THE ANODIZING PROCESS |
Anodizing is a chemical process that converts the surface of the aluminum to an oxide finish. This is actually a naturally occurring phenomenon, but it can be controlled in manufacturing processes. Anodizing consists of three processing stages.
|
Rich Rinka serves as the American Architectural Manufacturers Association’s (AAMA’s) technical manager for standards and industry affairs. Before coming to AAMA, Rinka worked in the industry as a field technical engineer for a component supplier, and also served as chair of the AAMA 800 Maintenance Committee. During his time in product development for the automotive industry, he developed (and still holds) four patents related to sealants. He can be reached at rrinka@aamanet.org.