Results for walls, window frames, and roofs with 70 percent reflectance
In addition to the analyses where high-reflectance coatings were applied to the walls, window frames, and roof individually, the modeled building also was analyzed with reflectance for all three surface types set to 70 percent. As expected, combined savings are higher than savings for a single low-reflectance surface (Figure 10).
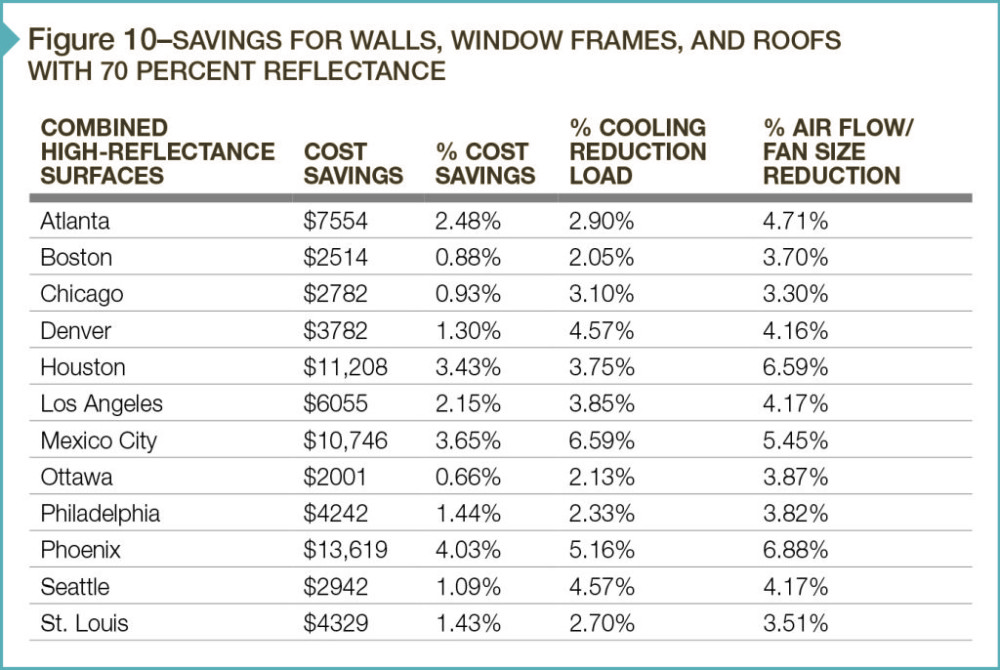
Conclusion
The energy modeling analyses showed high-reflectance coatings reduce energy costs significantly in warm and hot climates, and less so in the coldest climates, as would be expected. Other findings include:
- when wall reflectance was increased to 70 percent from five percent, energy savings as a percentage of total building energy cost ranged from 0.4 to 2.3 percent, depending on location;
- when reflectance for window frames was similarly adjusted, energy savings as a percentage of total building energy cost ranged from 0.4 to 1.2 percent; and
- when roof reflectance was increased to 70 percent, savings ranged from zero to 0.78 percent.
Cool roof savings are limited in comparison to other surface areas in this modeling study, because on tall buildings, a well-insulated roof only accounts for a small portion of its surface area. It should also be noted higher surface reflectances reduce design airflow in all cases.
Building configuration, HVAC system type, and local climate all are significant factors in determining a building’s potential energy savings. Nevertheless, the simulation analyses showed when designing a building for low energy consumption, even in cold climates, high-reflectance coatings should be specified for walls, window frames, and roofing given their small cost premium.
Scott Moffatt currently holds the position of market manager, building products for the coil, extrusion, and wood groups within PPG Industries. He has 36 years of experience within PPG’s industrial organization in various sales, sales management, and marketing functions covering multiple technologies and market segments. Moffatt’s current position involves getting PPG specified with architectural firms, glazing companies, and applicators. He can be contacted by e-mail at moffatt@ppg.com.