by Stephanie Lengel and Maha Nagra
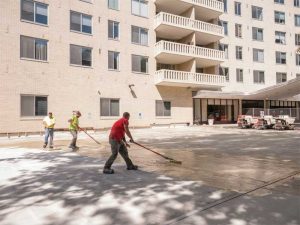
Protection of concrete decks, foundations, and other surfaces against damage that is caused by water infiltration, abrasion, and chemicals, can be accomplished with a range of coating and waterproofing technologies.
Gaining attention in this space in recent years are polymethyl methacrylate (PMMA) and polyurethane methacrylate (PUMA)-based solutions. For projects with tight timeframes and stringent performance requirements, PMMA/PUMA technology coatings and membranes are appealing due to its ultra-fast cure time, even in extreme weather conditions, and long-term durability.
Old is new again
The adage holds true for PMMA, a polymer that was initially discovered and commercialized in the 1930s as plexiglass by German chemists seeking to develop safety glass. A U.S.-based manufacturer had later produced its own version. PMMAs have been used in a variety of applications for more than 40 years, including acrylic nails, medical technology such as bone cements, musical instruments, and photovoltaic (PV) roof shingles for solar energy consumption. A transparent thermoplastic resin, PMMA offers a cheaper, more environmentally friendly option to polycarbonate.
Though often characterized as a new technology in construction, it has been used in roofing since the 1990s in Europe and for the last 12 to 20 years in the United States. It is now gaining recognition across North America for below-grade waterproofing and coating applications.
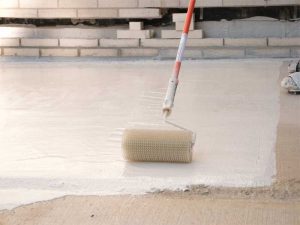
Differences between PMMA and PUMA
Both PUMA and PMMA technologies are rapid curing, meaning full cure in one hour or less after application. They require an activator to catalyze and initiate curing. PUMA and PMMA systems share many characteristics. PUMA is a polyurethane over polymethyl base and offers some advantages over PMMA, most notably its elongation properties and its ability to bridge cracks even at very low temperatures. PUMA technology coatings can pass ASTM C1305, Standard Test Method for Crack Bridging Ability of Liquid-applied Waterproofing Membranes, with elongation of up to 400 percent at 21 C (70 F) and closer to 300 percent at colder temperatures. With this much elongation, additional reinforcement should be avoided as it prevents the coating from stretching to its full capacity. This is important to note in cases where there is substantial movement, as in climates experiencing extreme temperature fluctuations throughout the seasons.
Versatility in construction
PMMA/PUMA’s molecular structure makes it suitable for fluid-applied applications in construction. Its bond strength is superior to alternative coating technologies because it is not a superficial adhesive bond, but rather a covalent or chemical bond that involves the sharing of electron pairs between atoms. The formation of bonds at the molecular level occur even when the catalyzed liquid is applied over an existing cured membrane, such as with a lap or tie-in, and is unaffected by the passage of time. This means, for example, a PMMA/PUMA system can be installed in a parking garage and recoated in an hour, or many years later with the same level of cohesive bond.
PMMA/PUMA coating systems can be used in pedestrian, under-tile, vehicular, and other heavy-duty, traffic-bearing applications experiencing significant wear and tear such as helipads, parking garages (especially around ticket spitters and turn lanes), bridges, loading docks, garbage, and chemical facilities. It is also used on roofing, balconies, terraces, walkways, plaza decks, planters, and because it can be fully immersed in water, in pools and fountains installed over occupied space. As a cold-applied waterproofing system, the below-grade applications are horizontal split slab and asphalt overlay.
Substrates suitable for PMMA/PUMA applications are numerous and include concrete, wood, masonry, gypsum board, and metals such as steel, copper, and aluminum, as well as existing roofing systems, provided the proper testing is completed to verify the roofing system is sound.