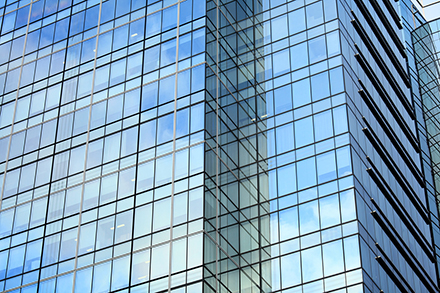
The first article in this two-part series lays the groundwork for this discussion on R-values and their use as a metric for thermal insulation performance. Now, in this second part, the author examines the real-world use of it as a gauge for ensuring insulation products function as intended.1
When it was created, R-value was really the only useful tool in evaluating the effectiveness of the available building insulations, among other materials. After the R-value rule was instituted, the energy efficiency of buildings improved, as well as the nation’s energy conservation effort and the marketplace and technology for insulations. Today, though, most of the insulation industry knows better, and R-values may well be dismissed as meaningless numbers on an insulation package that help to better organize warehouses.
The R-value can be an extremely misleading value due to the laboratory guarded-hot plate apparatus test methods used in attaining these numbers. These procedures are conducted under ideal conditions, and the real-world performance has absolutely no bearing on such tests. As a result, the listed R-values can be higher than what actually occurs. These tests obviously favor fibrous insulations whose performance drastically drops with temperature fluctuations.
The guarded hot-plate apparatus also does not take into account real-world conditions such as wind/wind-washing and moisture. If these conditions were taken into account, other insulation would far out perform fibrous products. These conditions will also effect fibrous insulation—because they are air-permeable—and will have far less of an effect on other types of insulation.
Wind-washing occurs as unconditioned air is allowed to move within air-permeable cavity insulations, such as fiberglass, cellulose, and board-stock insulations. Wind-washing, a form of forced convection, creates loss of thermal insulating properties because many insulation systems are not seamless and monolithic.
The Cellulose Insulation Manufacturers Association (CIMA) has suggested research by Oak Ridge National Laboratory (ORNL) has shown a reduction of steady-state R-values caused by convective heat loss in low-density fiber insulation materials during cold periods, when the temperature difference (i.e. delta T) between the heated area of a building and its cold attic increases.
CIMA states this phenomenon can reduce the steady-state R-value of affected products from 10 percent at a delta T of 10 to 12.8 C (50 to 55 F)—this is –8.3 to –3.8 C (17 to 25 F) in the attic of a space heated to 22.2 C (72 F) to as much as 40 per cent at a delta T of 32.2 C (90 F)— this is –27.7 C (–18 F) in the attic of a home heated to 22.2 C—that can occur during the most severe winter conditions in some portions of the United States.
It was recommended insulation manufacturers provide winter design correction factors in coverage charts to compensate for R-value erosion due to convective heat loss. Further, the manufacturers are required to state on the package label the insulation is not subject to convective heat loss at winter attic temperatures above -28.8 C (-20 F), if insulation material is not subject to R-value loss under cold conditions.2
When questioning whether R-values can be used to compare insulation systems, ORNL states:
R-values are a good starting point—but they are the results of small, meticulously prepared laboratory samples and do not necessarily reveal how an insulation system performs once installed in actual buildings. Different insulation systems with the same laboratory R-value can deliver much different levels of comfort and energy efficiency.3
These R-values are not indicative of the material’s actual performance in a real-world installation, even with the best possible installation.
Other insulations, such as SPF, outperform drastically in real world situations, but this information is obscured by the guarded hot plate-apparatus test and the R-value concept. Fiberglass, for instance, is generally assigned an R-value of approximately 1.38 per/cm (3.5 per/in.). However, it will only achieve that R-value if tested in an absolute zero-wind and zero-moisture environment. Oak Ridge National Laboratory’s “The Whole Wall Thermal Performance Calculator—On the Net” research shows “perfectly installed” batts lose 11 percent of their labeled R-Value, and commonly installed fiberglass batts lose 28 percent of their labeled R-Value.4

This study confirms a test conducted nearly 35 years ago by fiberglass manufacturers, and reveals the surprisingly large disparity between the labeled R-value and the installed performance of fiberglass batts.5 Zero-wind and zero-moisture are obviously not real-world conditions—buildings leak air and, often, water. Water vapor from the atmosphere, showers, cooking, and breathing constantly moves back and forth through the walls and ceilings. If an attic is not properly ventilated, the water vapor from inside a space can quickly condensate on the roof deck and drip into the insulation above the ceiling. Even small amounts of moisture will cause a dramatic drop in fiber insulation’s R-value—as much as 50 percent or more.
So, why is the use of R-value perpetuated? Maybe it is because performance cannot be defined by any one number and multiple values are needed to describe its performance. However, the problems become clear when this philosophy is transferred to a real-world situation, such as buying a car. Suppose the salesperson tells you he has the perfect car, it being a ‘5.’ One would automatically wonder if it was a ‘5’ on a scale of one to 10, a 2005, a 5-speed, or a 5-liter. It is likely more information would be needed, such as many miles to the gallon or how many previous owners. The use of R-value alone is similarly limiting, yet there are building codes such as International Energy Conservation Code (IECC) and International Building Code (IBC) requiring these values. Passing building codes is like getting a ‘D–’ on a test, barely passing. In other words, it has become common for meeting building code requirements to be enough, when so much more can be improved far above the safety/efficiency requirements code inspections deem as sufficient. These codes were instituted mostly for safety, and certainly not for building efficiency performance.
In a building, there can be areas, such as knee walls, or loose-fill insulation in attic ceilings, where fibrous insulation is being installed with no air barrier on one side (i.e. the attic side). Some of these codes are slowly changing, but this extremely common practice even further reduces the actual installed R-value from the package printed R-value. Fibrous insulations absolutely depend on an air barrier, on both sides, to try and attain the performance the packaging states.
What further complicates this issue is other insulations such as sprayed polyurethane foam (SPF), with higher performance per R-value, are held to this value and compared on a level playing field with fibrous insulations. Consumers should consider many things when choosing an appropriate insulation, including but not limited to, building design, orientation, and vapor permeance, as well as R-value.
According to FTC:
Citing research that heating energy consumption can vary 25 to 38 percent in structures insulated to the same nominal R-value with different insulation materials, CIMA similarly asserted that, by focusing only on R-value, the current Rule has the effect of misleading consumers into thinking that R-value is the only consideration when buying or specifying insulation.6
This comparison is happening every day and could be leading to misinformed decisions. For example, 2009 IECC for Climate Zone 4 stipulates an R-38 in a ceiling. Closed-cell SPF’s performance realistically tops out at around 101.6 mm (4 in.), which is an approximately R-25 to 28. This R-25 to 28 has been shown to outperform an R-38 of conventional fibrous insulation.7
However, if a closed-cell spray foam application was wanted in an attic, current code would require an approximate 152 mm (6 in.) R-38. This is a full one-third more material and labor that may unnecessarily prevent a great deal of specifiers to choose this product. Put more simply, building codes in many instances are preventing the use of higher-performance insulation systems.
Another complicating factor is many other building-related calculations depend on an R-value input. The strengths of the current building enclosure thermal metric (i.e. R-value) is it is simple to measure and communicate, along with being widely accepted. It was, however, created to describe the thermal property of a single material or property under specific and easily reproducible conditions. Its weakness is it oversimplifies the reality of enclosure assemblies (i.e. multiple materials or tolerances), and does not account for the real temperature conditions these materials are exposed to. It therefore neglects important physical phenomena occurring in real buildings and assemblies. The current industry focus on this material product standard has resulted in the use of inappropriate metrics for the control of heat flow.8
Conclusion
Although the thermal performance of any insulation product in actual use is complex and includes many parameters, in this day and age the industry can do better than R-value alone. It is critical consumers, contractors, and specifiers have a useful, accurate tool for evaluating the true performance of numerous types of building insulations. There is some encouraging work being done by Buildingscience.com, with its Thermal Metric Project. The program’s goal is to develop a metric that can capture the in-service thermal performance of whole assemblies. More accurate measurements will allow truly high-performance assemblies to be identified and promoted. When the testing criteria for a material’s performance is flawed, antiquated, and not actually performance-based, it is time to come up with new testing criteria and a new value truly based on performance.
Notes
1 The opinions expressed in this article are based on the author’s experiences and do not necessarily reflect those of CSI or The Construction Specifier.
2 For more, visit www.ftc.gov/os/1999/08/rvaluefr.htm.
3 Ibid.
4 See J.E. Christian, J. Kosny, A.O. Desjarlasi, and P.W. Child’s “The Whole Wall Thermal Performance Calculator–On the Net,” which appeared in Thermal Performance of the Exterior Envelopes of Buildings VII (1998).
5 This information comes from R.M. Neisel’s “A Study of the Effects of Insulation Gaps on Building Heat Losses, Final Report,” a Johns-Manville Sales Corp., report released in 1979.
6 Ibid.
7 For more, visit www.sprayfoam.com/cnt/docs/16/Attictestingarticle1.pdf.
8 For more, visit www.buildingscience.com/documents/reports/rr-0901-thermal-metrics-high-performance-walls-limitations-r-value.
Ken Wells has been part of the insulation industry for more than 17 years. In 2006, he started Elite Insulation & PolyPro LLC with his brother Chris, and father Bob; the company has been recognized with two National Industry Excellence Awards from the Spray Polyurethane Foam Alliance. Wells can be contacted at kwells@polyprollc.net.