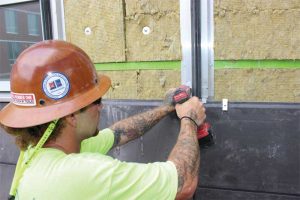
Cladding choices
Many materials or combinations are popular rainscreen cladding options, including:
- terra cotta;
- calcium silicate;
- glass fiber reinforced concrete (GFRC);
- porcelain slabs;
- natural stone; and
- other materials serving the cladding function.
Installation
“The modern mason is trained to be a comprehensive building enclosure installer.” – Jim Boland, president of the International Union of Bricklayers and Allied Craftworkers.
Sequencing of the installation starts with identification of the layers of assembly and assigning responsibility for each material. It is advisable to think about sequencing of products and which trades have access to lifts or scaffold. Generally, the air and vapor barriers integrated with flashings are the first component installed on the backup wall system. This is usually followed by the cladding sub-frame support system, and then continuous insulation (ci). Important connections to address on the mockup panel are methods to make water/air barrier continuous at sub-frame fastener penetrations, and if the sub-frame will be thermally disconnected from the support wall. With insulation, any Z-furring or clips are the responsibility of the installing contractor and are not provided as part of the cladding hardware package. Most sub-frame systems account for irregularities in the building structure and backup materials. Major irregularities are noted and communicated to the appropriate party for resolution prior to hardware installation. Approved shop drawings control the process, and the installation contractor will note the differences between these and actual construction, thereby getting proper approvals before continuing.
As the starter tracks are installed, care should be taken to ensure all horizontal components are level and the vertical elements are plumb. As opposed to traditional masonry with mortar joints, the open-joint larger module of the rainscreen cladding has less forgiveness of smaller unit masonry laid in mortar. Installing craftworkers of masonry cladding materials still need to have expertise in masonry material storage and handling skills, access to scaffolding, masonry cutting, modular layout, humoring of material, and cleaning.
Coordination between trades is critical throughout the installation process. The control layers must integrate with the flashing and the air barrier installers for the walls and roofs should coordinate with each other. One solution is to have a single trade or contractor install the enclosure.
IMI and IMTEF training programs prepare a craftworker for all phases of the rainscreen system.
“As in any masonry product, preparation and layout is the key to a successful installation. With so many manufacturers and different installation methods, pre-installation training is a must. IMTEF offers many courses relevant to rainscreen installations. Air barrier certification, blueprint reading, and rainscreen installation courses are all available at local training centers across the country,” said Bob Arnold, national director of apprenticeship and training, IMTEF.
Case study of St. Barnabas Medical Center West Wing Expansion
This project was an expansion of an existing hospital. The architect was Francis Caufmann and William Blanchard was the construction manager. The contractor installed the air and vapor barrier, cavity insulation, brick, and approximately 465 m2 (5000 sf) of terra cotta rainscreen material on this project. The terra cotta was detailed in its own specification section. The mason contractor, BackBrook Masonry, submitted a combined bid for traditional masonry and rainscreen work. Bricklayers installed the sub-frame system and cladding units with no composite crew. Terra cotta was used as return accents at the windows as well as decorative eyebrows and soffits.
The estimate was created by BackBrook Masonry’s estimating department with assistance from the IMI. Shop drawings were created by the material supplier and submitted electronically. Paper copies of the shop drawings were used for installation in the field.
The window returns were installed from the scaffold used to install the brick. The eyebrows and soffits were installed using man lifts. The contractor said it was not feasible to erect scaffold for the limited amount of work at these areas.
The work was completed with a four-person crew. Depending on the application or area, the crew could install 200 to 300 linear feet of track, or 100 to 150 units per day.
This example demonstrates the advantage of trade coordination and proper pre-planning on a project. The rainscreen system was installed quickly and efficiently through coordinating the control layers with the rainscreen support system and cladding.