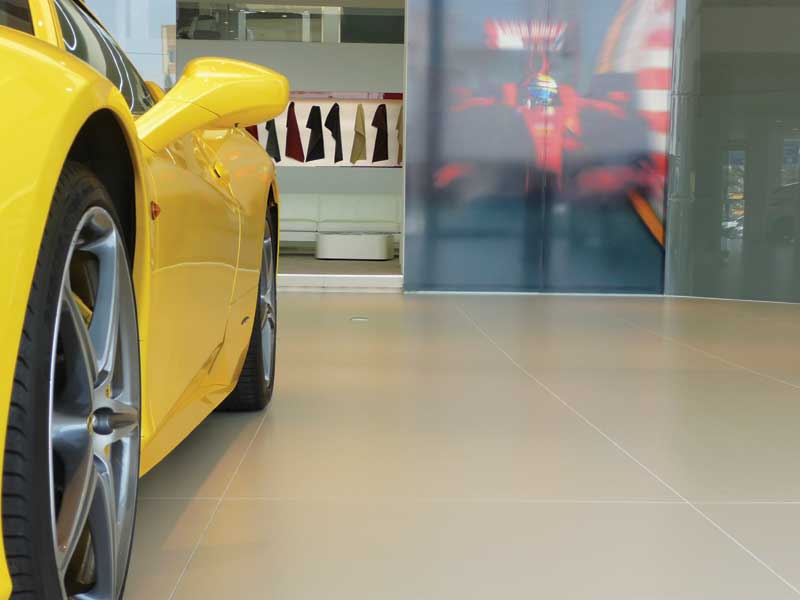
by Neil McMurdie, PhD
In 2009, amid great fanfare and drama, the latest innovation in porcelain tile technology was formally announced and touted at the Cersaie exposition in Bologna, Italy. Multiple manufacturers had developed and launched new commercial tile lines that were bigger in size and thinner than anything else currently on the market.
The halls of the exposition buzzed with the news of tiles as thin as 3 to 5 mm (0.12 to 0.2 in.) in various sizes and patterns with the potential to revolutionize the industry. The new technology was expected by some in the industry to bring tiling back into a leading position as a ‘green’ wall and floor finish. Thin tiles weighed less per square foot, could be produced and shipped with a lower net carbon footprint, and produced with the consumption of fewer natural resources. Suddenly, thin was in.
Prior to the formal announcements at Cersaie (and all the press releases that followed), work carried out in the preceding two or three years had shed some light on the thin tiles. Fiberglass mesh had been applied to the back of some of the thinnest products to give strength using state-of-the-art adhesives that would work with standard cement adhesives. Expert installers were already working to find ways to direct bond these tiles in vertical positions on walls and exterior façades.
The biggest opportunity for total square footage of application would eventually be if the materials could be applied to flooring systems not only in new construction, but also, more importantly, in renovations. A thin tile would reduce added dead-load weight and make renovations easier with less need to adjust floor heights and make doorway transitions. The question that immediately came up was how to install and what adhesives should be used on the new thin tiles to make the launch a commercial success.
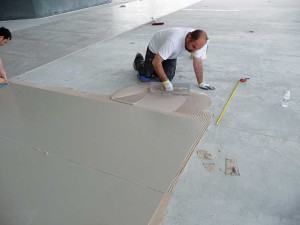
Nothing like hitting a moving target
Since the 2009 announcement, engineers and developers at major tile manufacturers around the globe have continued to make progress in the way thin tiles are manufactured and fabricated. As of late 2012, at least three technologies are used.
Most of the 5-mm thick tiles are produced using a variation of the traditional pressed methods. Here, large presses compact the starting ceramic powder in a mold in a sequential process. Newer processes use a continuous press on a conveyer belt to make long sheets of tile with a wide variety of patterns and layers. The continuous sheets are then cut to size for shipment. The available maximum size has grown from around 1.2 m (4 ft) in 2009 to tiles 1 x 3 m (3.3 x 9.8 ft) long today—not the kind of flooring the average DIYer throws in the back of a minivan for a quick weekend project.
More companies and countries have jumped on the thin-tile bandwagon; the market has become global in the past two years, with each new product containing its own variations and nuances. The net effect has been to make it just that much harder for the architect, design professional, contractor, and installer to know exactly what is best and where to use the readily available new products.