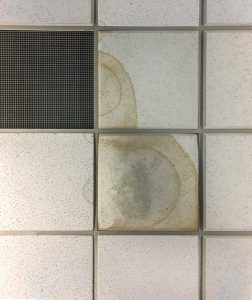
If painting perforated vinyl or metal panels, do not allow paint to bridge small openings as this will decrease acoustical performance. Care should also be taken to avoid painting any acoustical insulation or backing that is visible through the perforations.
Panel replacement
Ceiling panels that cannot be cleaned or refinished acceptably will have to be replaced. If replacing an entire ceiling, considerations about what type of replacement panels to use is similar to the decision-making process used in new construction (read the article, “Breaking Habits: A Rational Approach to Ceiling Product Evaluation,” published in the March 2020 issue of The Construction Specifier).
If most of the existing ceiling is still relatively new and only a small percentage of panels are discolored or damaged, spot replacements may be the best option. The specifier will have to determine whether replacements will blend with the remaining panels, and develop a process (such as unit pricing) for indicating which ones need replacing.
Consideration should be given to life-cycle costs and whether existing panels should be replaced in-kind or with something more durable and sustainable. If 25 percent of the ceiling needs to be replaced every four years, then the entire ceiling is theoretically replaced in 16 years, in addition to cleaning costs over the interim period. A more sophisticated analysis makes clear that spot replacement becomes less acceptable with time because newer panels will increasingly contrast with old ones and accelerate the need to replace the complete ceiling. It could be more cost effective to replace the entire ceiling at once with a material that will last 20 years or more, and be less expensive to clean over that period.
Environmental impact should be factored into a replacement decision. A major manufacturer of mineral fiber products recycles panels. However, they may not be recyclable if painted, wet, or moldy (often the condition of panels that need to get replaced), and they must be stacked and palletized.
High-quality vinyl and metal panels are often recyclable without degradation in their material properties. Small quantities of installation scrap can generally be recycled into local material recovering streams, and one maker of thermoformed panels has a take-back program to recycle retired vinyl panels.
Another option avoids, for the time being at least, concerns about recycling decrepit panels. Panels are available that can be used to reface a ceiling; the thin thermoformed panels are installed beneath existing ceiling panels. Combined with slide-on grid coverings, it may be one of the most expedient ways to rejuvenate a ceiling.
Replacement products need to match the fire-safety performance of originals. In this regard, it is important to note some mineral fiber panels are fire-resistance rated, and some thermoformed panels are tested and approved for use as drop-out panels beneath fire sprinklers.
Conclusion
Ceilings are subject to soiling and damage despite being out of reach of most occupants. Due to their exposure, visual degradation may make a ceiling unacceptable even though it is still functional. For ceilings needing frequent cleaning or rejuvenation, it is worthwhile to determine whether replacement or refacing is more cost-effective than restorative treatments. If spot replacement happens often, then complete replacement with more durable and easy-to-clean materials may be a better choice.
Ceilings can become dirty or disfigured during construction due to improper handling, leaks, and damage, so this discussion about rejuvenating ceilings is also applicable to final cleaning of newly constructed or remodeled spaces prior to being turned over to building owners. Full appreciation of durability and maintainability should be part of the product selection process during design and specification.
Michael Chusid, RA, FCSI, is a frequent contributor to The Construction Specifier, and a consultant to building product manufacturers. He can be reached at www.chusid.com.
Steven H. Miller, CDT, is a freelance journalist and consultant specializing in the construction industry. He can be reached at steve@metaphorce.com.