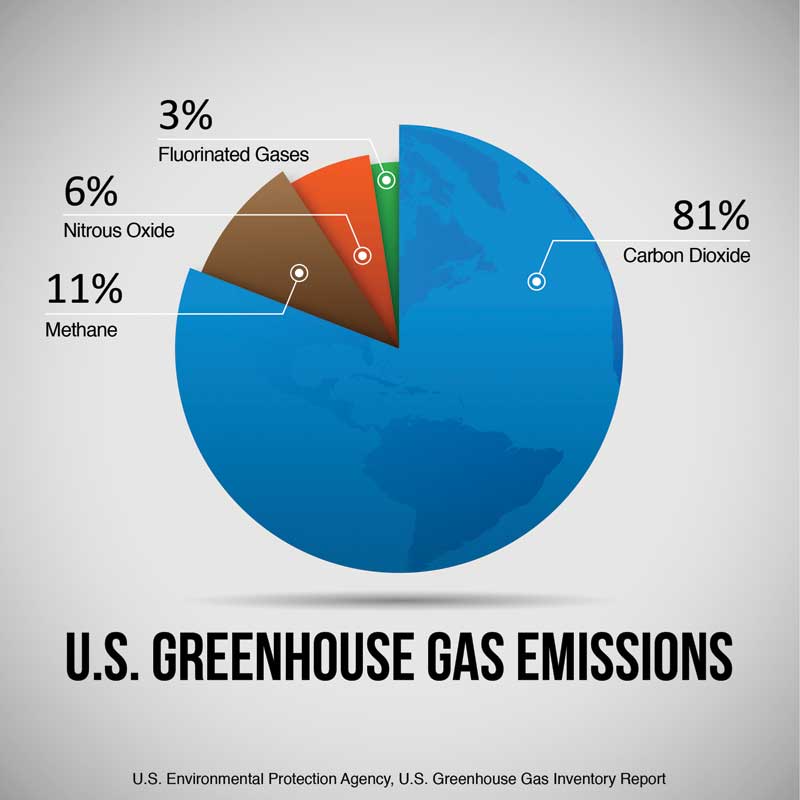
Image courtesy U.S. Environmental Protection Agency
Fly ash, GGBS, and SCMs
Use of fly ash as a cement replacement has become increasingly common due to the material’s resistance to sulphate attack, chloride-ion penetration, and de-icing salt-scaling. These benefits are the result of fly ash’s pozzolanic reaction, consuming the calcium hydroxide formed from the hydration reaction
of ordinary Portland cement and water, which produces supplementary C-S-H. With the introduction of additional C-S-H comes an increase in density and strength. (A pozzolan is a silicate-based material that reacts with the calcium hydroxide generated by hydrating cement to create materials with cementitious characteristics See R. Helmut’s “Fly Ash in Cement and Concrete” published by the Portland Cement Association in 1987.) The strength of fly-ash blends has been reported to be initially low, but improved over the long term. (See the fourth edition of Lea’s Chemistry of Cement [Elsevier Ltd, 1998] for Massazza’s work.) Other benefits include increased workability and less water demand, lower heat of hydration, and reduced drying shrinkage.
ASTM standards define Class F fly ash as a pozzolan, whereas Class C has some cementitious properties. In the British standard BS 3892-1997, Pulverized-Fule Ash, Class F fly ash was used in the mixing of samples nine years earlier. This means fly ash does not have cementitious properties, but when finely divided and introduced to water in the presence of calcium hydroxide, it chemically reacts to form a compound that does.
GGBS, on the other hand, comes from the production of iron in a blast furnace to which flux is added to the charge of iron ore. At 1400 to 1550 C (2552 to 2822 F), it produces slag, which is a liquid containing all the impurities from the iron ore and coke. The principal oxide components are lime (added as flux), silica, and alumina. If this liquid is rapidly cooled by converting the liquid into small droplets (granulation), crystallisation is prevented. This allows it to form a glassy structure with latent hydraulicity, which, after grinding, resembles sand.
The oxide composition of GGBS varies between plants due to different ores being used. However, composition remains roughly the same for one plant’s output. As GGBS hydraulicity is latent, hydration reactions are very slow, so an activator is required. There is a range of activators that can be used, such as alkali, lime, and gypsum. However, the most common is Portland cement.
Due to the extensive body of research on cement and cementitious materials, we now understand more about C-S-H, the original minerals required, the ideal conditions vital to its correct formation, and possible replacement materials for Portland cement (i.e. supplementary cementitious materials [SCMs]). This knowledge reveals that mix design is of the utmost importance.
Natural materials and those taken as waste from other industries have varied mineral composition. This gives rise to the main disadvantage of SCMs—quality control of the material. Concrete suppliers rely almost exclusively on the SCM supplier to ensure the quality of the product, which can vary significantly and have a profound impact on the hardened concrete. Control of fly ash is greater than with GGBS, as it is more variable, and can affect setting, air content, and overall strength.
Another disadvantage to SCMs involves the delayed setting time and low early strength. Too often, this results in subsidence and plastic shrinkage, along with thermal and volume stresses. These cause unintentional cracking, structural problems, and overall negative impacts on architectural quality.
There is another option—one involving a look back at history to find what the modern construction industry’s predecessors did right to make constructions such as the Colosseum, aqueducts, the Pantheon, or the Appian Way.