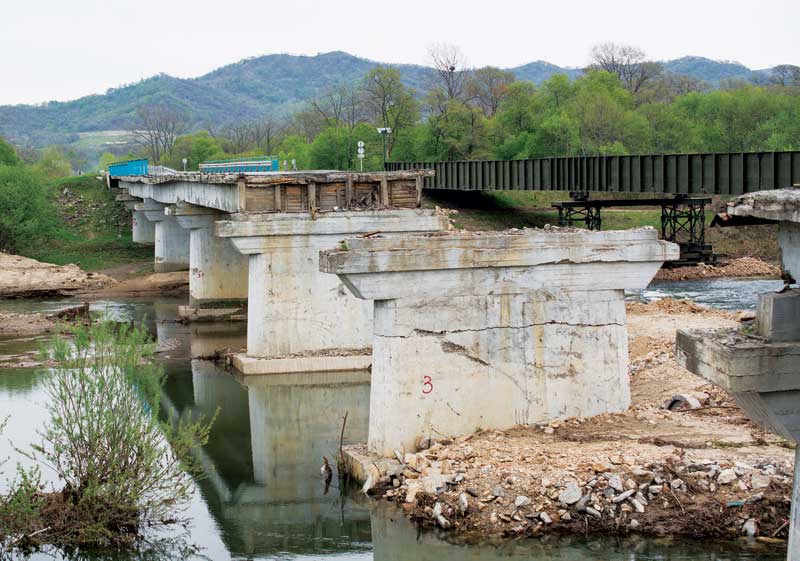
Photo © BigStockPhoto
Preparing for the future by returning to the past
The Ancient Romans made durable and resilient concrete, creating monuments and buildings that withstood centuries while maintaining mechanical and aesthetic performance. Shown at the beginning of the article, Trajan’s Market is the world’s oldest shopping mall—a large complex of Roman ruins opposite the Colosseum. Designed by Apollodorus of Damascus, and built in 100−110 AD, it is an example of the durability of Roman concrete. Fully understanding how they did this would be critical in producing a modern, durable, and environmentally responsible concrete material.
Much research has built on earlier studies in the characterization of constructs such as the seawater harbors of Ancient Rome. Now, this knowledge must be applied to the development and optimization of modern concrete. How can we maintain strength with a variety of natural resources? Can mimicking the Roman process fulfill current demands, including the modern construction schedule? Al-tobermorite research by Paulo Monteiro’s team at the University of California, Berkeley alongside the U.S. Department of Energy’s (DOE’s) Lawrence Berkeley National Laboratory (LBNL) found the Roman concrete recipe not only used less lime when manufacturing concrete, but the limestone was also baked at a lower temperature than modern Portland cement, reducing fuel demands and thus CO2 emissions. (See M.D. Jackson et al’s “Unlocking the Secrets of Al-tobermorite in Roman Seawater Concrete,” in American Mineralogist (vol. 98) in 2013 or “Material and Elastic Porperties of Al-Tobermorite in Ancient Roman Seawater Concrete” in the June 2013 edition of the Journal of the American Ceramic Society.)
Monteiro and his team proved the Romans were not only making concrete at two-thirds or less the temperature of the Portland cement process (creating less CO2), but the concrete was also more resilient, surviving, wind, water, and chemical attacks for 2000 years. If modern design/construction professionals know far more about cement than third-century Romans, why is newly designed infrastructure struggling to stand the tests of time?
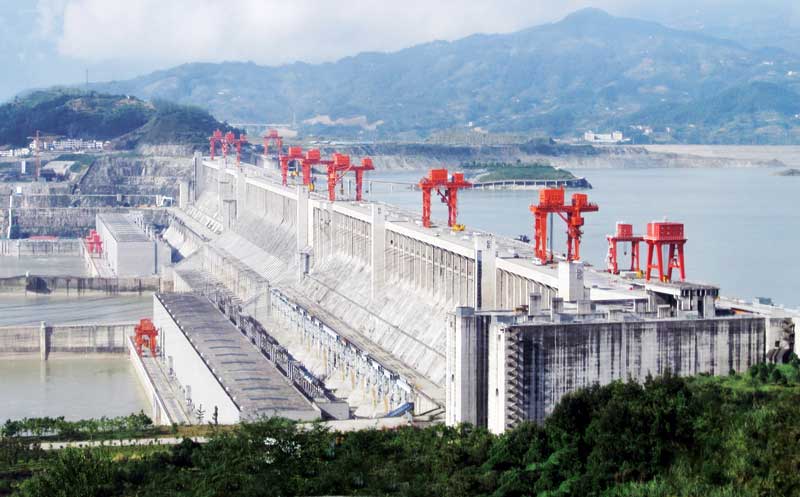
Photo from Rehman via Wikipedia CC BY 2.0 (derived from Le Grand Portage)
Conclusion
In April 2016, the United States signed the Paris Agreement written by the United Nations Framework Convention on Climate Change (UNFCCC), agreeing to fight the increase in global average temperature. (For more on this agreement, see The Construction Specifier article, “How Paris COP21 Drives Low-carbon Building Energy Efficiency” by Paul Bertram, FCSI, CDT, CSC, LEED AP, GGP. Visit www.constructionspecifier.com/how-paris-cop21-drives-low-carbon-building-energy-efficiency.) As such, this country, along with the 191 others who signed the treaty, will be moving more toward sustainable and renewable energy. This means concrete will become more invaluable to support the new technologies and the longevity of construction materials. With knowledge and clear, correct specifications, it is possible to design just as strong, just as true, yet more resilient concrete to help cut carbon dioxide emissions.
We must start thinking more about reducing CO2 emissions from concrete, and one of the best ways to do this effectively is to look to the past—Roman maritime concrete can provide fresh perspective. This legacy highlights not only that it is possible to make concrete with fewer carbon emissions, but also that the material can be made better and more resilient.
Concrete microstructure will determine the macrostructure and, therefore, the durability of the home, road, bridge, airport, or nuclear waste storage facility where the concrete is used. This means the characterization of cement is vital to the built environment and to ensuring creation of a resilient infrastructure.
This highlights the necessity for ongoing research—not just to reduce the cement content of concrete, but also to increase knowledge of cement. Such knowledge will further the optimization of cements and concretes in order to better exploit alternative energy sources, such as those contributing to the goals of the Paris Agreement.
Chris Bennett, CSI, is a concrete consultant for commercial projects in North America. He specializes in document creation, contractor training, and technology testing for MasterFormat Divisions 03, 07, and 09. He can be reached via e-mail at chris@bennettbuild.us.
Rae Taylor, PhD, holds a doctorate in civil engineering and materials science from the University of Leeds, and a post-graduate certificate in technology management from the Open University. Her principal research interests lie in the field of materials science and improving the environmental impact of construction materials, with a focus on the effect of cement replacement materials and additives on cement microstructure. Taylor has published on the topic of cement in numerous academic journals and conferences, such as the Journal of the American Ceramic Society, American Mineralogist, and Cement and Concrete Research. She can be reached at raemorristaylor@gmail.com.