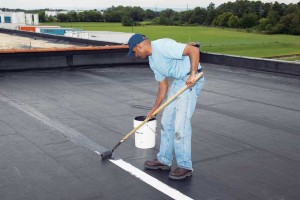
EPDM roof re-cover
The re-covering option is primarily employed on adhered and mechanically fastened systems, providing the opportunity to address more building issues than a typical restoration. Energy-analysis software reveals most buildings in the United States are under-insulated. (This is reflected by the fact American Society of Heating, Refrigerating, and Air-conditioning Engineers [ASHRAE] 90.1, Energy Standard for Buildings except Low-rise Residential Buildings minimum R-values increased from 15 to 20 in many climate zones when the standard was updated in 2007.) This is important, as the cost of energy has gone up dramatically in the past 10 to 15 years.
Re-cover options afford the opportunity to add more insulation to the rooftop without having to tear off the original material. The insulation can be fastened in place or, in some cases, adhered directly to the existing material with a two-component urethane adhesive. With the recent advancements in insulation product offerings, drainage issues can also be addressed with tapered insulation or crickets before installing the new membrane. The ability to correct ponding water and drainage issues on the roof is a huge advantage of the re-cover option.
Some insulation materials should not be placed between two individual single-ply roof membranes; however, this can be addressed by drilling weep holes through the existing membrane before placing the new insulation. Dewpoint calculations can also be done to determine if there will be an issue. In most cases, the insulation is only added in certain locations to address drainage issues.
Altering a building’s rooftop color is also easier in a re-cover than a restoration. If a structure has a black roof in the South—where there are more cooling degree-days than heating—it makes sense to consider re-covering the system with a white membrane. Conversely, if one has a white roof in the North—where there are more heating degree-days than cooling—a black roof re-cover could be the answer.
The emergence of fleece-backed technology (i.e. a single-ply membrane mated to a fleece material) has advanced the roof re-cover industry. These membranes separate the new from the old, while providing an increase in puncture and hail-damage resistance.
This method has been popular for several years when re-covering asphalt-based roofing assemblies, and the technology has also recently been extended to single-ply systems. In many cases, the existing EPDM membrane can be power-washed, and then a fleece-backed membrane can be adhered directly to the old roof. One can think of this as a two-ply system that provides dual protection, yet is much lighter in weight than many of the alternative multi-ply roofing systems. Fleece-backed membranes are typically available in EPDM, thermoplastic polyolefin (TPO), and polyvinyl chloride (PVC) options of varying thicknesses.
Another option growing in popularity is a vegetated roof re-covery. This allows a new membrane to be loose-laid on top of the existing system and then covered with a traditional or modular vegetated system. These ‘green roofs’ not only provide an aesthetically appealing roofing option, but also help reduce a building’s stormwater runoff and overall energy cost. As vegetated roofs can add significant weight to the building, a structural analysis should be performed before they are implemented.
Benefits for owners and the environment
As the market for single-ply continues to grow, there is an expanding body of knowledge, techniques, and design options available to building owners looking to protect their assets, maximize their return on investment (ROI), and be in sync with the sustainability movement. Restoring or re-covering an existing roof system makes sense because the owner and the environment receive numerous advantages. In addition to the obvious gains of a watertight roof, other benefits include:
- extended service life;
- lower waste generation;
- less ozone depletion;
- little disturbance to building operations; and
- financial advantage of incurring minimal maintenance costs versus large-scale capital expenses required for full replacement.
Investigative tools have dramatically improved over the past decade, with investigation techniques beginning to follow suit. In the future, system and material choices will be based on how the roof space will be used and, therefore, the process of tearing off an existing roof may become less appealing.
For more information, see What Building Owners Need in a Rooftop.