Alternative concrete systems
Cinder concrete
Cinder concrete—one of the most encountered alternative concrete systems—can be one of the most troublesome due to the unpredictable chemical properties of coal cinders used in its construction. Patented in 1906 by engineers A.W. Buel and C.S. Hill, cinder concrete became a dominant structural slab system in the 1920s to the 1940s. Surviving examples can be found extensively throughout New York City as cinder concrete had several advantages over other systems of the day: high load capacity, fire resistance, low material cost, and ease of assembly.
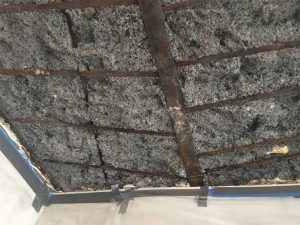
As indicated by its name, a cinder concrete system is comprised of a cinder fill layer encased on either side by low-strength concrete. This cinder fill is made from the cinder and clinker leftover from coal burning, an abundant waste product at the turn of the century. Anywhere from 101.6 to 203.2 mm (4 to 8 in.) thick, this loose cinder layer provided lightweight fire protection.
Cinders would also be used as an aggregate in the concrete itself, a typical mix being one part concrete and two parts sand mixed with five parts cinders. The resultant concrete weighed 38.5 to 49.9 kg (85 to 110 lbs) per square foot and had a rough, pumice-like texture.
Tensile strength in this system was provided by wire mesh draped between light-gauge steel beams. Laid in this way, this arrangement provides tensile support by means of a catenary system, the strength of which is the basis of many of the various alternative floor systems.
Taken together, the cinder fill provides fire resistance and helps distribute the load, the draped wire mesh provides tensile strength, and the concrete topping provides the walking surface, transfers loads to the mesh, and protects the system from water intrusion. In typical installations, the floor would be covered over with wood sleepers and hardwood floors or, in the case of rooftops, with a loose cinder fill sloped to provide drainage.
Roebling floors
Introduced in 1892, Roebling floors were one of the earliest concrete floor systems used in the U.S. The Roebling models were defined by a series of patents held by William Orr for John A. Roebling’s Sons corporation, a producer of wire and wire rope. The genesis of these floors came out of a desire to find new markets for wire cloth, one of the products the company produced.
By adding small gauge rods into the wire mesh at intervals, Orr produced stiffened wire cloth to serve as the basis for the Roebling floor. On its introduction, it was marketed as a lighter and cheaper alternative to the then commonly used brick and terra cotta arches. Two systems were used: System A and System B, with variations for different building types.
System A was comprised of the company’s stiffened wire cloth arched between I-beams, providing a formwork onto which lightweight concrete was poured. Often, this would be a cinder concrete of the same type used in the floor systems discussed previously. Above this, wood sleepers and fill material provided the base for wooden flooring. Depending on the situation, the arches could be covered by another layer of stiffened wire cloth stretched between the I-beams and covered with an applied plaster coating or left open with the beams themselves coated in concrete. While this might appear to be a reinforced concrete system, it is not and was not intended to be so, as the wire mesh is positioned distinctly outside of the concrete.
System B, while also considered a Roebling floor, was a much different system. In this case, the concrete was reinforced by flat iron bars laid over top the supporting steel beams, with the wire cloth again providing formwork; though, in this case, the cloth was not arched but rather laid flat underneath the reinforcing bars. This system could accommodate wider spans than System A, by virtue of its tensile reinforcement.
The metropolitan system
The metropolitan system was patented in 1899 by Conrad Freitag. What distinguishes it from other alternative concrete systems is a gypsum binder, instead of Portland cement. In the metropolitan system, gypsum plaster is mixed with treated wood chips and sawdust as aggregate, then poured between steel beams. As with cinder concrete, tensile strength is provided by wire reinforcement in a catenary arch, though in this case the structural support is provided not by wire mesh but by twisted pairs of wires individually secured and strung between the beams. These wires carry almost all the load; the thick but lightweight plaster slab predominantly serves as a base for the walking surface and provides fire resistance.
Other alternative systems
While these three systems may be the most common of the alternative concrete floor systems, they are not the only ones. These systems were typically produced and sold under patent, and this drove diversity of design along with innovation. Many systems exist as slight variations of one another; as an example, one cinder concrete deck was observed to have iron bars laid across the beams in the same fashion as a Roebling System B. General themes are often present: the use of wire reinforcement to provide tensile strength, short spanning distances, and the use of thick slabs to impart fire resistance. Aggregate materials are diverse, and nonstructural materials are often present solely to impart fire resistance.