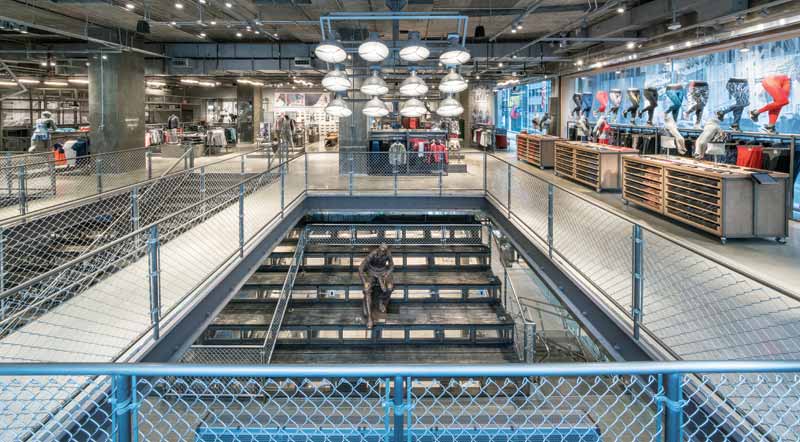
Photo courtesy Adidas
Water
Concrete is the world’s second most used material in construction. Water is the first. Water reacts with cement and aggregate to create concrete but it is also essential for the material’s demolition or refinement. Hydro-demolition technologies use high-powered streams of water to remove concrete. Unlike mechanical demolition using tools like jackhammers, hydro-demolition removes material on a bridge, road, or building without creating micro-fractures in the surrounding matrix. This helps the concrete structure to remain intact longer while reducing the need for patch and repair materials.
Water is also essential in refining existing concrete surfaces. When the contracting firm Desco took on the task of surface preparation and architectural concrete floor installation at a 55,741-m2 (600,000-sf) Rolls Royce facility, a wet refinement process was chosen to reduce material use and meet the client’s schedule. Polishing the floors dry would have meant using additional latex and epoxy grouts and potentially heavy coats of acrylic sealers as well as the extra time and labor necessary for installation.
There are additional benefits of a wet polishing. The accelerated installation means reducing the operation of diesel generators and their impact on our air while powering commercial grinding and polishing equipment. The air at the worksite is made safer in another way by trapping silica on the surface of the concrete in a slurry instead of letting it become airborne. (Click here for Occupational Safety and Health Administration’s regulatory requirements.) Dry polishing requires specialized air filtration systems and frequent filter cleaning to reduce the amount of silica dust making its way into the air. Additionally, Occupational Safety and Health Administration’s (OSHA’s) new regulatory requirements can mean heavy fines for contractors and even jobsite shut downs.
“Grinding wet means we know we will always maintain a safer worker environment and be able to meet OSHA’s new regulatory requirements on allowable airborne silica, and finish fast. We do not cut or polish dry anymore,” says Brandon Godbey, head of Desco’s polishing division.
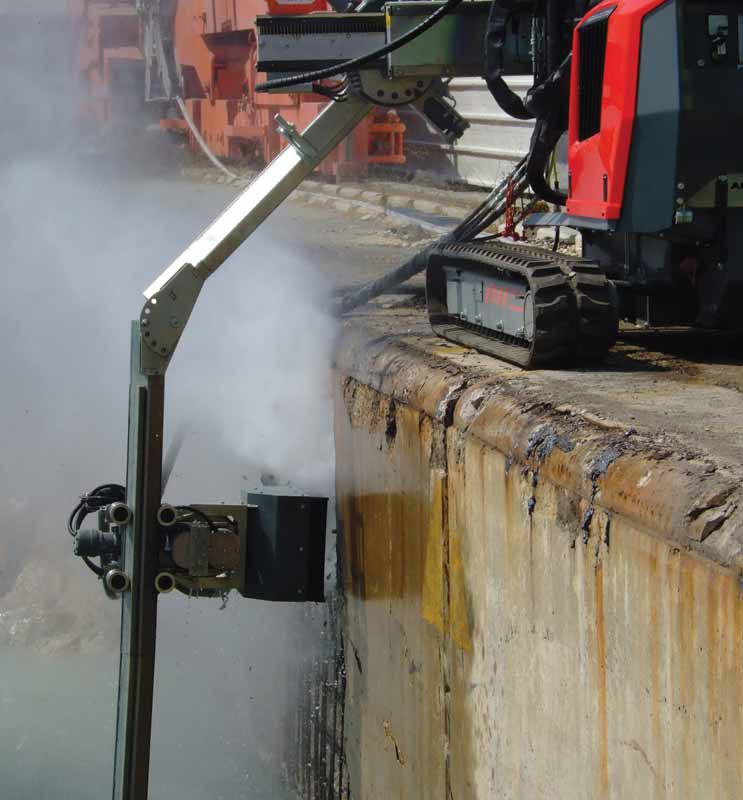
Photo courtesy Aquajet
Cutting-edge technologies
At the National Center for Education and Research on Corrosion and Materials Performance (NCERCAMP) at the University of Akron in Ohio, David M. Bastidas, PhD, and his colleagues from the chemical and biomolecular engineering department are advancing another type of eco-friendly concrete science at the micro level. Although still in the early stages, studies related to smart micro-encapsulated corrosion inhibitors are investigating concrete corrosion, specifically in areas where steel rebar makes contact with the concrete matrix. Corrosion is reduced by using time-released “pills” containing natural colophony (rosin) from California pines. Rosin or “Greek pitch” is a solid state of resin made from pine and other coniferous trees. This system of limiting the corrosion and degradation of concrete comes from allowing the progressive and efficient release of resin inhibitors throughout the life cycle of the concrete.
Corrosion inhibitors are one of the most efficient methods to prevent corrosion in concrete, but historically they have been plagued by high cost as well as the contaminant nature of some of the compounds themselves. This upcoming technology is attractive because unlike concrete corrosion prevention from the 1960s the micro-encapsulation in the natural resin coating makes it environmentally sustainable as well as effective. The corrosion inhibitors consist of a core-shell structure containing combinations of hydroxides and nitrites from different metals, forming a microcapsule. The inhibitor releases according to the pH of the surrounding matrix and the presence of aggressive agents like chlorides and carbonates. This could mean substantially less “plastic” in many reinforced concrete structures while still enjoying the benefits of inhibitors. Since the pine resin is not soluble in water (it has a hydrophobic nature) it will only react with corrosion agents and not simply in the presence of moisture. (A more in-depth overview of this technology will be presented later this year at the concrete symposium at University of Akron’s NCERCAMP. Visit www.uakron.edu/ncercamp for details.)
Conclusion
Concrete production makes up six to eight percent of total manmade greenhouse gasses (GHG). (For more, click here.) Further, many of the raw materials for several epoxies and resins used in coatings and patch material are largely derived from petroleum. The carbon footprint is substantial. The effect after 50 years of employing The Graduate-era concrete methods is bridges are falling apart and buildings are cracking. Building professionals understand replacing the elements creating C-S-H (water, aggregates, and cement) has a cost.
It is not to say plastics are not useful or do not have their place, for they have, of course, been helpful in many ways. When building a waste water treatment plant and designing spaces to house fluoride tanks, one must have epoxy coatings on the concrete floor or soon the facility will not have any concrete at all. The author is not questioning the function of plastic, rather if its use is necessary at all times, given the high stakes regarding construction costs and the environment and with successful alternative technologies being readily available. For example, the concrete in the lobby of the waste water treatment plant does not need the same coatings as the tank room.
All of us would like to see concrete last longer, enjoy a smaller carbon footprint, and require less material waste. This will not happen by maintaining the same 50-year-old benchmarks in construction documents. It will not happen by avoiding hard conversations or repeating mistakes of the past. However, it can happen by exploring new possibilities, beginning new conversations, and learning from each other. To paraphrase Mr. McGuire, there is a great future in concrete.
Chris Bennett, CSI, is a construction consultant specializing in contractor training, specification writing, and building technology development for MasterFormat Divisions 03, 07, and 09. Bennett can be reached via e-mail at chris@BennettBuild.US or via Twitter @BennettBuild.