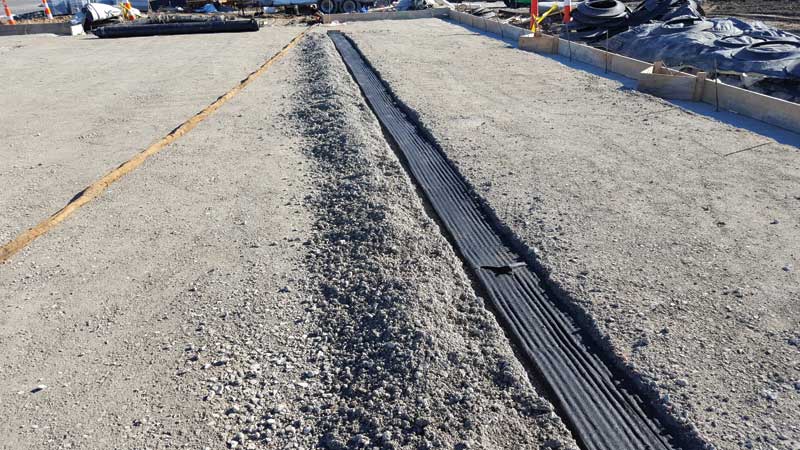
Inspection and plan
An experienced installer and personnel familiar with the building must be tasked with identifying and detailing aspects of the structure’s characteristics affecting its risk for vapor intrusion. Is there something unique about the building’s sub-slab? In some situations, elements may only get discovered when reviewing the building’s blueprints. It is imperative to know these characteristics to properly design an effective mitigation system.
Various parts of the building could have been built at different times, and therefore, have different physical characteristics as a result of this time lapse. For these reasons, finding an individual with first-hand knowledge of the structure and perhaps insight into its construction can be very valuable. Building additions often have very different soil than the rest of the structure. Over time, soil is compacted, and as building additions are made at a later time, the soil’s integrity can be drastically different and must be accounted for when designing a system. To draw up an effective plan, layouts of the building’s suction points, pipes and blowers, electrical work, and mechanical details must be included. This also allows for a more accurate cost estimate and scope of work.
Installing the system
The first step should be to seal all openings in the foundation floor and walls through which vapor can easily make its way up. By sealing off these potential pathways, the bulk of the vapor mitigation system does a more effective job. This practice cannot be thought of as sufficient, but it is very helpful in improving the system’s overall performance.
The next step is to install the mitigation system itself. A couple of options are available, but the most commonly employed one is sub-slab depressurization (SSD) system. It is most frequently used as a result of a few competitive factors. SSDs are generally regarded as the most robust solution to mitigate the risk of vapor intrusion. They are designed to control the upward migration of chemical vapors from the soil by creating a negative pressure beneath the sub-slab, as well as venting and piping away the chemical vapors from the interior breathing zone.
SSD systems have been widely employed to mitigate vapor intrusion for existing buildings. Some of the drawbacks to this system are they can be difficult to design and consume electricity. The systems do have to be switched on, and because of their mechanical nature, require a level of maintenance. Although the negative pressure created below the slab can greatly reduce the vapor intrusion risk, it does not limit it fully as adsorption and penetration of these chemicals can still occur through the concrete slab and openings.
SSDs are often specified because they are well-known and similar to the radon mitigation assemblies that have been installed for many years. They also have the advantage of being active systems which, through the use of fans, pumps vapors accumulating below a building’s slab out from under the building and away into the open air. This means they may be particularly suitable for heavily contaminated sites.
An alternative system is a retrofit coating available for the purpose of blocking vapor intrusion in existing structures. This material can be applied directly to the concrete slab, basement walls, and around penetrating uprights. This is frequently very cost-effective when compared to SSD systems as it does not require the deconstruction and replacement of the basement slab. However, some retro-coatings are non-loadbearing so it is important to select the proper type for the specific traffic load.
Non-loadbearing coatings may provide a perfect solution for areas such as crawlspaces or when a protective concrete application is placed on top. Both loadbearing and non-loadbearing types have the advantage of low maintenance over SSD systems. Unlike the SSD system, the product is always ‘on,’ requires no electricity, and has no ventilation fan needing upkeep or replacement.
In order to ensure maximum protection from vapor intrusion, some projects may require both an SSD system and a retrofit coating.
As more scientific data regarding vapor intrusion comes out, and building owners become aware of the health risk to their occupants and the potential long-term liability associated with vapor intrusion in their buildings, interest in mitigations systems for existing buildings will only increase. This is especially true in high-risk locations, such as urban areas, densely developed for a century or more.
Wesley Robb is the director of technical strategies and applications at Vapor Mitigation Strategies, a Wellington Environmental Company. He has 23 years of environmental field and laboratory experience, including several years of soil vapor sampling and analyses. Since joining Wellington in 2004, Robb has managed onsite activities of various kinds, including underground storage tank removals, soil remediation, Phase I investigations, and vapor/soil/groundwater sampling. He can be reached at wes@vapormitigationstrategies.com.