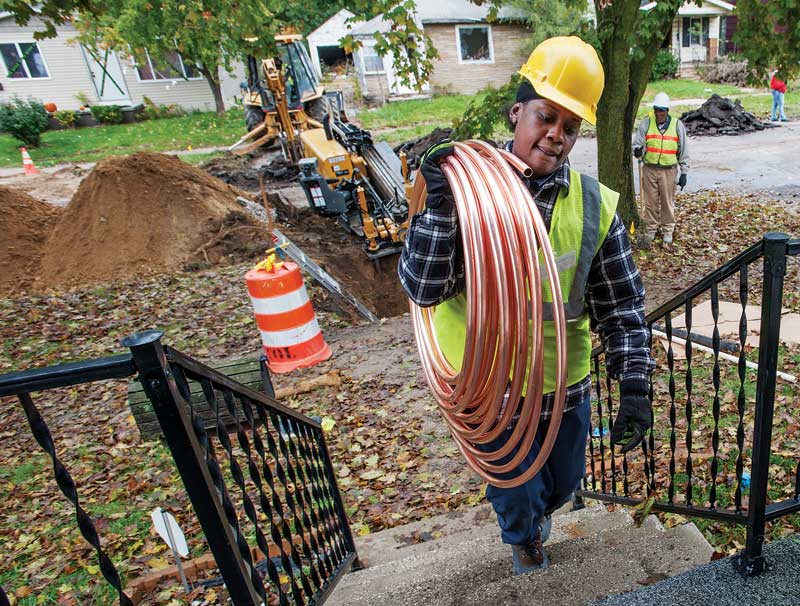
On the other hand, copper service lines are completely impermeable, preventing outside chemicals that may be spilled on nearby streets or insecticides and fertilizers intentionally spread on yards from contaminating the water system. There has been no evidence copper can leach anything through the joints in the system. Flared, mechanical, and soldered/brazed joints create strong, durable, metal-to-metal seals.
The metal can also be exposed to ultraviolet (UV) rays and oxidizing disinfectants (e.g. chlorine, chloramines, and chlorine dioxide) without risk of cracking or failure. Meanwhile, plastic pipes have exhibited an above-average risk of premature failure due to oxidative degradation in underground potable water systems treated with an oxidizing disinfectant like chlorine.
Copper is also highly corrosion-resistant in most underground environments. The exception occurs in soils containing high concentrations of chlorides (from de-icing salts), sulfates, or ammonia that collect around the copper tube without draining. This is generally caused when the tube is installed in an unsealed sleeve or other conduit preventing drainage. Soils with high levels of sulfate or cinders can create sulfuric acid, which can attack copper and other metals.
Plastics can eliminate the risks of some types of corrosion, but they also introduce other risks such as oxidative degradation. Fortunately, copper corrosion can be prevented by proper system design, installation, and—in cases where water chemistry might be an issue—water treatment. Most causes of underground copper system failure stem from improper system installation, which is why the Copper Development Association (CDA) goes to great lengths to educate on proper installation and joining methods. (To learn more about copper piping and installation best practices, visit www.copper.org. The Copper Tube Handbook can be accessed at www.copper.org/applications/plumbing/cth.)
Copper can also withstand high pressures and stresses without failures, while other materials crack, rupture, and leak, such as when used in underground applications where freeze-thaw and other natural occurrences cause the ground to settle and move.
Copper and plastic can both withstand freezing to a point, but both can also break if the line freezes because the ice plug in the line continues to grow in diameter, physically expanding the tube wall until it stretches beyond its elastic limit. Copper has a higher strength than plastic and can withstand a higher level of this stress before breaking. Plastics have shown to be less robust when exposed to freeze-thaw shifting—in other words, they crack.
INSTALLATION BEST PRACTICES |
No matter what the material, poor installations can lead to poor performance. When installing copper underground service lines, here are some tips to keep in mind:
|