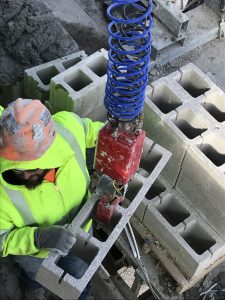
Zuidemas elaborated on the two-fold advantage.
“We were able to plan for fewer pieces being put in the wall. The robotic lift-assist devices gave us the ability to decrease labor while ensuring our people were not getting as fatigued or strained,” he said.
He explained the ingenuity of the design.
“The gripper is on a cable suspended overhead. It clamps onto the middle of the CMU, and the block becomes weightless. The masons can then manipulate it without the strain of supporting the weight,” he said.
Although new technology always meets with some resistance, the contractor was pleased with how quickly most of the masons took to the user-friendly equipment. Zuidemas recalled, “Once they stepped back and looked at the benefits, even our reluctant workers warmed up to the idea.”
He emphasized, “The use of robotic devices does not change the need for the skill of the masons. It puts a lot of strain on a body to lay heavy blocks all day. A lot of our veteran workers have had shoulder replacements, back problems, or injuries. This system extends career longevity for everyone.”
Maximizing production
During construction of the barracks foundation, the masons were able to maximize production by utilizing several scaffolds at a time. With a 7-m (22-ft) arm reach, the robotic lift-assists could pull 813-mm CMUs directly from the shipping pallet, thus eliminating the need for messy and space-stealing pre-stocking piles. At peak productivity, the Zuidemas had 12 robotic lift-assists moving block on the NSGL site.
Matt Oklevitch, marketing director for a construction tech firm, noted, “Robotic technology assists masons by taking the added strain of balancing and positioning material out of the equation. The lift assists make the block weightless in the worker’s hands and allow the mason to focus on the precision and craft of laying or installing the material.”
The teaming of large CMUs with robotic lift-assist devices resulted in minimizing labor costs, time savings, and reduced physical wear and tear on workers. However, the partnership did not stop there.
The barrack’s brick façade design included the overlay of a pre-finished anchored stone veneer that emulates natural cut stone.
A construction tech firm designed and created a stone veneer gripper for those 12 x 24 x 4 veneers that weighed in at approximately 41 kg (90 lb) each. This interchangeable arm could be easily swapped out with the standard gripper on the robotic lift-assist device, meaning Zuidemas’ team could use the identical base for two applications.
Conclusion
Over the years, the building industry has undergone significant changes, most notably in the area of recruitment. According to the Chicago Tribune, “In a 2016-2017 U.S. talent shortage survey, the global staffing firm Manpower Group reported skilled-trade vacancies are the hardest jobs to fill in the country. Skilled trades (electricians, carpenters, welders, bricklayers, plasterers, plumbers, masons and more) have maintained the No. 1 position in vacancies from 2010 to the present.”
This challenging trend has been offset by structural and technological advances in materials and equipment. Such innovative industry advancements are sure to make the building industry more attractive to a wider demographic.
For now, contractors hoping to win bids on major projects will continue to encounter stringent cost limitations and demanding time-lines. Large stone products decrease the number of units required for a job, and robotic assisters take the burden of lifting off the mason—a symbiotic process resulting in reductions in labor costs.
The forward-thinking Zuidemas have been able to overcome industry hurdles such as labor shortages, growing real-estate costs, and complex bidding processes to emerge as viable contenders in an extremely competitive industry. Clearly, they saw the writing on the wall.
Dave Jackson is the senior brand manager for Echelon Masonry & Dry Mix at Oldcastle APG, a CRH Company. Coming from an ad agency background with a specialization in building products, Jackson melds creativity and industry intelligence to help the Echelon team remain the premier provider of modern masonry solutions to architects and builders across the United States. He can be reached at dave.jackson@oldcastle.com.