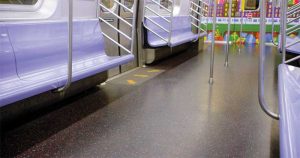
Proper selection and specification of interior materials, especially flooring, have a direct impact on air quality in two important ways: their basic composition and in the maintenance protocol throughout the product life cycle (including finishing, coating, stripping, and recoating). Premium rubber floors are low in emissions and pollutants. It is made from mostly natural materials and does not contain polyvinyl chloride (PVC), phthalates, or other plasticizers.
Additionally, the cleaning protocol of premium rubber is also low-emission since it requires little more than water. Being uncoated, basic cleaning agents high in alkaline are unnecessary for surface restoration. Flooring products endorsed by third-party organizations, including Greenguard Gold, contribute to a safer, healthier travel.
A more comfortable commute
Long commutes can keep passengers on their feet for great lengths of time, ultimately resulting in musculoskeletal disorders and loss of time from work. While many flooring materials are hard and unforgiving, some products, such as premium rubber, have a crosslinking of materials to provide superior ergonomics and comfort underfoot. Unlike most floorcoverings, premium rubber is made of materials with the ability to ease the stress of walking and standing.
Riders also need to be able to move across floors with confidence. Coating-free premium rubber offers verified nonslip properties to improve the safety of its passengers. It also helps reduce confusion and disorientation from reflective or overly smooth surfaces delivering a ‘perception of slipperiness’.
Using public transportation can also be quite noisy. The World Health Organization (WHO) establishes a limit of continuous background noise in a room at 35 A-weighted decibels [dB(A)] during the day and 30 dB(A) at night. In a third-party study for in-room impact noise reduction, a premium rubber floor reduced sound by 21 dB(A), dampening unwanted sound more effectively than other resilient floors ranging from 3 to 7 dB(A).
As the foundation of the built environment, flooring plays a primary role in transferring sound. The noise level emanating from a floor depends largely on the type of floorcovering. Rubber flooring’s sound-absorption properties can help reduce noise level up to 20 dB.
Designed with purpose
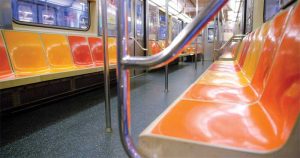
Flooring in public transportation should be more than just durable, it should also provide guidance and information to passengers. Wayfinding techniques, such as directional flooring lines, help riders safely navigate to their intended destination. Clear symbols for wheelchairs, bicycles, suitcases, or baby carriages offer passengers a quick overview of designated areas. Safety symbols also make it easier for passengers to find their way around quickly, regardless of language.
Modern ultrasonic cutting machines allow premium rubber flooring to be produced in any shape, symbol, or wayfinding system design, down to the millimeter. The exceptional dimensional stability of premium rubber means each inlay can be installed seamlessly. Symbols are firmly anchored in the floor to protect against vandalism or damage from wear and tear. Thanks to precision cutting and incorporation into the floorcovering, indicators last significantly longer than signs or stickers.
Premium rubber floors allow inlays to retain its shape permanently. Joints or cracks staining and disturbing the image will not form. This also means premium rubber floors with inlays can be cleaned easily and economically. The seamless installation is even suitable for areas where high standards for hygiene are required. The installation method can include heat or chemical welding, if it is wanted, but it is not required.
Rubber flooring stands up to New York City subways
The New York City subway system has more than 1.75 billion riders each year, so it needed a high-durability, low-maintenance flooring to handle the traffic. It has been relying on premium rubber flooring for its rail cars since the early 1990s. Today, every one of its 6418 subway cars (approximately 371,612 m2 [4 million sf] of floor space) is covered by rubber flooring. This rubber floor meets or exceeds all transit standards developed by the Federal Railroad Administration for fire and slip resistance. Its low-maintenance regimen also means the floor cleans up quickly.
Future of transportation
According to a 2014 United Nations Report, 54 percent of the world’s population resides in urban areas. By the year 2050, the number is expected to rise to 66 percent. This, in turn, will further foster the need for additional mass transit to help avoid traffic congestion, rising commuter times, and the impact of emissions and greenhouse gases (GHGs) on global warming.
Fortunately, premium rubber flooring systems are up for the challenge. It can be found in public transit systems around the world from subways and trains to buses and beyond.
The primary standards relating to fire safety govern the use of rubber flooring. Additionally, specifiers should be aware of slip-resistant properties, durability over time, ease of the installation, and maintenance requirements when specifying rubber flooring for transit stations.
Not all rubber is created equal
Virtually all rubber floorcoverings share the same basic ingredients and are manufactured via similar processes. However, there is an infinite number of variables in the types, qualities, and quantities of raw materials. Additionally, there are many variables in the production process itself. They include:
- homogeneous: consistent construction through the thickness of the materials;
- heterogeneous: multiple layers of different types and qualities of rubber and/or other materials;
- continuous vulcanization: lighter pressure, lower temperatures, longer process to create continuous sheet goods; and
- press vulcanization: high heat and pressure to create higher density tile goods.
Rubber flooring that is both heterogeneous and press vulcanized eliminates the need to ever coat the flooring. While many rubber floorcoverings may appear to be the same, the materials and production variables referenced above produce floors differing significantly in terms of durability, stain resistance, maintenance, and reparability.
Tasha Hughes is a public relations and marketing specialist for nora systems, by Interface, an international rubber flooring manufacturer developing flooring solutions for a variety of commercial markets, including healthcare, education, industry and life science labs, and public buildings. She can be reached at tasha.hughes@nora.com.