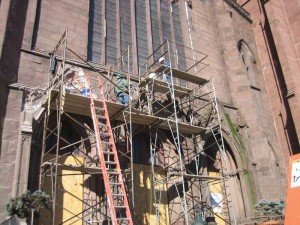
Photo courtesy Allegrone Masonry
Deterioration and early cathedral repairs
For the Cathedral of the Immaculate Conception, major stone repairs were required in 1938—less than 50 years after construction had completed. The parapets were removed and the engineer recommended recladding the building in granite. While this was not done, retooling of the sandstone surface was completed on at least two occasions. They removed 25 to 50 mm (1 to 2 in.) of the surface each time as it was delaminating. The vulnerable brick backup was exposed in some areas.
The issue of deterioration came to a head in October 1995 when a piece of stone fell from the north tower during a wedding ceremony. Three restoration studies had been completed prior to this event, but this near-catastrophe set the wheels in motion to tackle the big project.
In 1999, Bishop Howard J. Hubbard announced the cathedral’s restoration, committing the money to completing the first phase. The 64-m (210-ft) tall north tower was stripped of its stone and reclad with St Bees sandstone from Cumbria, England. At the time, there was not enough portland brownstone available to complete the work. St Bees sandstone was chosen due to its color, availability in large quantities and high bedding plane dimensions, price, and durability in a northern climate. The stone met or exceeded all ASTM dimension stone requirements (See “ASTM Standards,” at the end of this article). The first exterior phase of the project was completed in 2004.
The project
In October 2009, project documents for the next phase of the exterior restoration were issued. Three highly carved Gothic portals and the staircase leading to the front entrances were to be replaced. Invited bidders were asked to submit their pricing. Surprisingly, the base bid called for portland brownstone as the replacement material for the carved portals.
This author was part of the team qualifying its stone supply quote with the proviso “Subject to availability of suitable quarried stone.” It was extremely unlikely enough quality material would be available. The estimated quantity of stone was net 20 m3 (700 cf). With a waste factor in excess of 50 percent, the raw quarry block requirements were over 120 tonnes.
The sub-contract to supply stone was signed in November of 2010 with the masonry contractor, Allegrone Masonry. The process of field dimensions, templates, and shop drawings began in earnest before winter. Along with the project restoration architect from Mesick Cohen Wilson Baker Architects (Larry Wilson, restoration architect) and the cathedral’s rector (the Very Reverend William Pape), the stone suppliers visited Portland Brownstone Quarries, the only operational brownstone quarry in North America. They selected the best of the available quarry blocks.
Five blocks were shipped from Connecticut to the stone-cutting shop in Ontario, Canada, arriving in late December. A few quick cuts on the 1.8-m (6-ft)-diameter saw confirmed expectations—the blocks had cracks and seams running along weak bedding planes. The maximum available course height was 609 mm (24 in.). The project required 138 stones with bed heights 380 to 1140 mm (15 to 45 in.). The available stone represented just 20 percent of the total volume needed, and only 50 of those stones smaller than 609 mm could be cut. There was no material available for the higher stones.
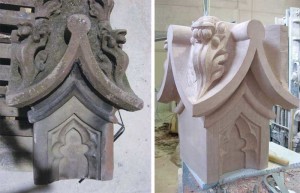
With little hope of obtaining enough quality material in a timely manner, the alternate of St Bees sandstone, as it would match the newly re-clad north tower. There was enough material in stock to get the job rolling through the winter and the remainder could be shipped from England in the spring when the risk of frost on the open seas was over. In other words, the material would be slightly less expensive, readily available in the required dimensions, and in sufficient quantities to complete the job within the construction schedule.
Meanwhile, shop drawings were completed by mid-January 2010, and approved shortly thereafter. This allowed the mason contractor to begin dismantling the portico and salvaging samples of the ornately carved details. A full tractor-trailer load of “sculpted debris” soon arrived at the stone-cutting shop. These ‘models’ would help guide the carvers and sculptors as they replicated the ornate detail. The cathedral was planning a re-dedication ceremony in the sanctuary to celebrate the interior restoration as part of its Easter services. The stonework around the entranceway and the scaffold had to be gone by March 26—a goal successfully met.
Carving and sculpting began in earnest through the winter and additional quarry blocks arrived from England in the spring. The first delivery was scheduled for June 18, with everything on track until May, when the supplier for the podium and stairs (under separate contract to the mason) was unable to complete its contract. Shop drawings had begun, but were left unfinished. The mason contractor and the architect conferred and asked the stone supplier to pick up the slack.
Granite and marble are traditionally supplied by fabricators specializing in the hard stone industry. In this case, the stone provider completed the shop drawings and contacted some of its associates to find a sub-supplier for the granite—a Swedish Bohus material. Unfortunately, the price and schedule were unacceptable and two substitutes were offered: a domestic Wausau Red Granite and an Indian version of Wausau. The price difference was almost $80,000 between domestic and offshore varieties. On June 3, the approval to proceed with the Indian material was given.
Delivery of the stone was 10 weeks from approved shop drawings, putting the project schedule in jeopardy. The mason contractor needed to start the installation of the carved sandstone in advance of the podium, but the design and schedule called for the podium stones to be in place and the sandstone to bear upon it. In a coordinated effort between stone supplier and site masons, the base course was supported on poured concrete pedestals. The profiles were recessed such that the granite could be notched, installed later, and tucked under the sandstone to conceal the concrete.