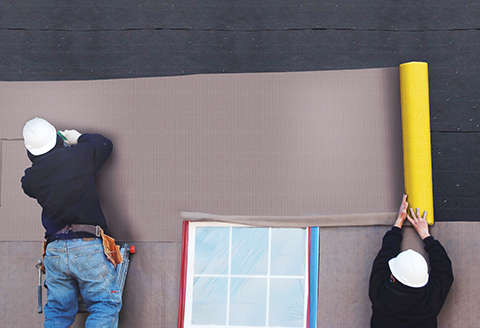
by George Caruso
When addressing moisture management it is important to recognize and accept one simple and indisputable reality: water gets into buildings. No matter how tightly a building is constructed or how well it is insulated, and no matter what type of cladding is chosen and how expertly it is installed, moisture will inevitably find a way into the building.
Moisture infiltration can undermine structural integrity, cause exterior surfaces to deteriorate, and shorten the life of paints and stains. It can also foster mold and rot that not only cause structural damage, but also pose serious health hazards. Ridding a stucco wall assembly of liquid water and water vapor as quickly as possible—before it can damage structural components—is what moisture management is all about.
Stucco builds a following
During the upturn in U.S. construction from 1992 to 2006, stucco cladding material gained extreme popularity. Valued for its versatility and relatively low maintenance schedule, stucco offered builders a product with the potential to last for the structure’s life. However, buildings were constructed faster than good oversight could keep up with. As a result, water management was often overlooked.
“Builders were opting for a quicker, cheaper, and faster method over quality, proven systems and solutions,” said Kevin Thompson, president of The Green Valley Group, which provides inspections for moisture-related problems, thermal imaging, and building envelope forensic services.
Like many cladding solutions, stucco can have its challenges. However, the majority of issues are moisture related. These issues are incredibly problematic as they are hidden from view and often build up within the wall cavity for years before they are detected.
“The awareness of the issues with stucco has led owners of facilities both young and old to become more cautious of stucco applications,” Thompson noted. “All types of buildings have problems. It is just that stucco, though aesthetically beautiful, is one of the least forgiving products on the market when it comes to bulk water intrusion.”
For successful wall systems, an effective drainage and drying system is required. In stucco, when only minimum standards are followed, there is little room for drainage, and the system readily absorbs water—a combination making the product unforgiving of installation errors and lack of attention to detail.

Improving WRBs
Water resistive barriers (WRBs), used as part of an exterior wall system, are designed to prevent air and water from entering the stud wall cavity from the outside. They also allow the free passage of water vapor to the outside of the building so the framing and wall cavity can dry, reducing the threat of mold and rot.
In an effort to minimize the problems surrounding stucco, builders have started integrating improved moisture management solutions. There are numerous options currently on the market, including traditional building paper, rainscreen systems, sealants, and self-adhered flashing membranes. Choices are expanding, driven by advances in technology, evolving building codes, and growing customer concern with mold prevention and other factors. Each of the aforementioned moisture management products has its place, depending on local environmental conditions and project details.
“Regardless of the product, drainage and drying are the top two concerns,” explained Thompson. “You cannot stop 100 percent of bulk water. So when the water gets behind the cladding, project teams must ensure continuity within the wall system making every effort to get it out from behind the system as quickly as possible—through both drainage and drying.”
Traditionally used as an element to resisting initial moisture infiltration, building wraps go a step farther by helping to remove trapped moisture from the building enclosure. Building wraps provide a vapor-permeable layer that resists liquid water from the outside, while also allowing water vapor to escape the assembly, enabling the wall to “breathe.” (For example, if water vapor is driven from the interior to the exterior during a heating season, the building wrap will allow the vapor to escape.)
An alternative to the traditional WRB is a high-performance drainable building wrap. Offering all features of a building wrap or building paper, drainable building wraps also include a drainage system. Drainable building wraps are designed to promote bulk water removal by channeling moisture to the outside through spacers or channels or manufactured into the building wrap sheet. The building wrap’s structure is engineered to maintain a more constant drain rate despite the repeated wetting and drying cycles observed in wet or humid climates.
These enhanced products provide a much higher and more constant drain rate than standard building wraps. Compared to standard versions, the newest drainable building wraps—especially those providing a minimum of a 1-mm (0.03-in.) gap—can be as much as 100 times more effective at removing bulk water from the wall.