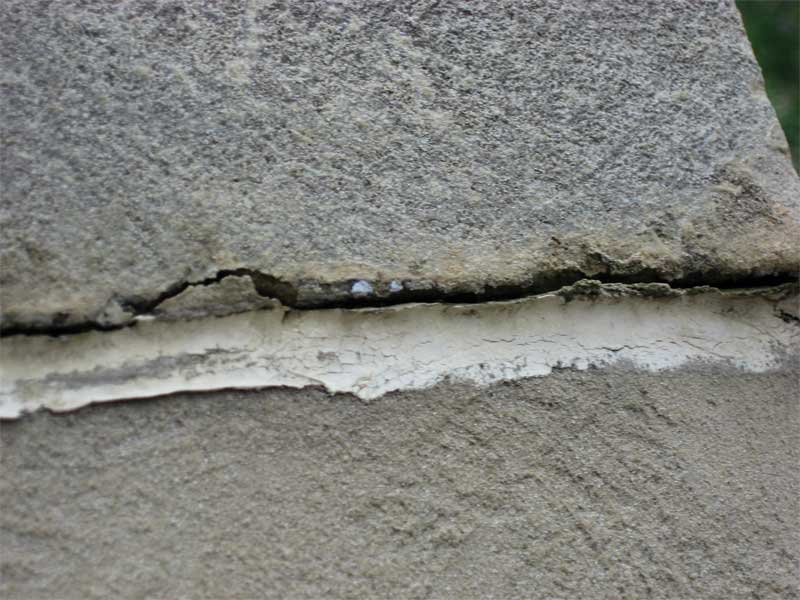
Sealant types and properties
For residential and commercial applications, the six most common types of sealants are:
- water-based latex;
- solvent-based acrylic latex (acrylics);
- butyl;
- polysulfide;
- silicone; and
- polyurethane.
No one sealant type is universally better or worse than another; some are better-suited to a given application than others due to their physical and chemical properties.
Latex sealants
These sealants are popular for residential use because they are easy to apply, adhere well to most substrates, and are generally paintable. For low-movement applications, they are an economical option that gets the job done. Where they fall short is in situations where a high movement capability is necessary, such as for high-rise buildings and moving joints. Latex is also prone to shrink, pulling away from the substrate and leaving open gaps where water can penetrate.
Acrylics
Acrylics are mainly used in exterior applications, where their ultraviolet (UV) stability puts them at an advantage over water-based latex. They are also less likely to shrink over time. On the downside, acrylics can be difficult to tool, and they do not perform well in high-movement areas.
Butyls
Adhering well to a wide variety of substrates, butyls can be difficult to apply due to their stringy consistency. These sealants also have poor resistance to abrasion and shear forces, which limits their performance in demanding building applications.
Polysulfides
Polysulfides can accommodate submerged applications, such as in a fountain or pool. They have excellent flexibility, even at low temperatures, and they exhibit little shrinkage or UV degradation. However, they are expensive, and tend to have high levels of volatile organic compounds (VOCs). At 10 to 20 years, the long life expectancy for polysulfides may help compensate for the upfront costs, particularly considering the difficulty of re-sealing an underwater surface.
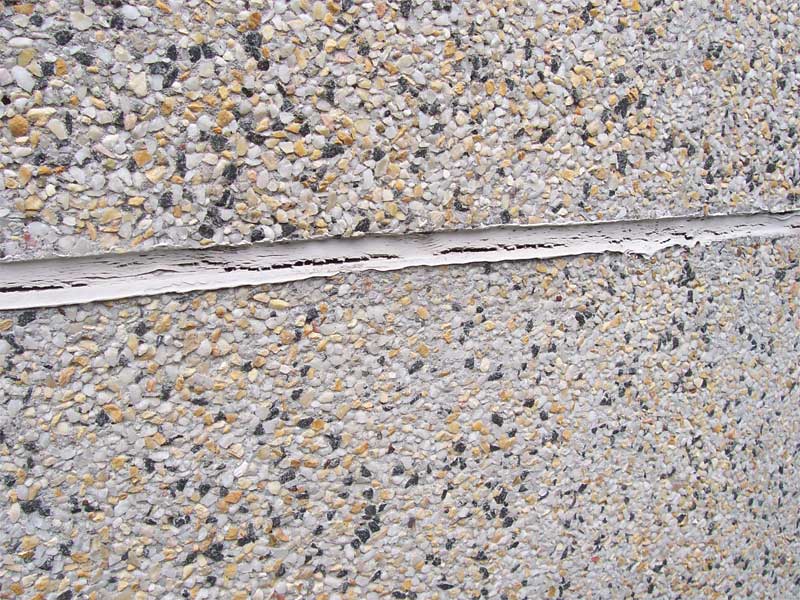
Polyisobutylenes
With similar properties to natural rubber yet significantly better aging characteristics, polyisobutylene resins are used in sealant formulations because they resist degradation due to aging and chemical attack, and they have low permeability. Often the primary seal in insulating glazing unit (IGU) window applications, they resist vapor transmission and prevent the inert gas between glass panes from leaking. Typically, a silicone secondary seal is employed in conjunction with the polyisobutylene for durability and long-term adhesion. Usually formulated as hot-melt sealants, polyisobutylenes melt mix with ease.
Silicones
Silicones have excellent thermal resistance, dynamic movement capability, and good adhesion, but silicones are easily vandalized and tend to collect dirt. For some substrates, staining may be an issue. In addition to general sealant applications, silicones are also commonly used as structural glazing sealants, securing sheets of glass to framing elements. Of all the common sealant types, silicones tend to be the most expensive—however, they also have the longest service life.
Polyurethanes
These sealants adhere well to most surfaces with little substrate preparation, making them the go-to sealant of many contractors. Their excellent resistance to abrasion and shear forces, along with strong adhesion and movement capability, make them a good choice for applications such as plazas, which demand durability and resilience.
PCBs IN SEALANTS |
Polychlorinated biphenyls (PCBs) were a common additive to sealants from the 1950s until they were banned in the United States in 1979. Thanks to their elasticity and chemical stability, they were added as plasticizers to building sealant used for windows and masonry. Exposure to PCBs can cause cancer, as well as endocrine disruption, immune suppression, liver damage, reproductive system failure, and neurotoxicity.
PCBs are regulated under the Toxic Substances Control Act, but state and regional regulations vary as to their safe disposal. Since PCBs can leach into the surrounding substrate or soil, abatement may involve demolition and/or excavation, adding substantial time and expense to a sealant replacement project. At a minimum, containment measures must be put in place during rehabilitation to prevent PCB-containing dust from becoming airborne. Site access should be limited, and workers must wear appropriate protective clothing and respiratory equipment. Removal methods should minimize heat generation, as PCB gases may be released into the air in response to high temperature. Also avoid grinding, which produces dust and may lead to aspiration of PCBs. PCBs can be a formidable obstacle to sealant joint rehabilitation. However, the potential health consequences of negligence outweigh the inconvenience and expense of proper abatement. |