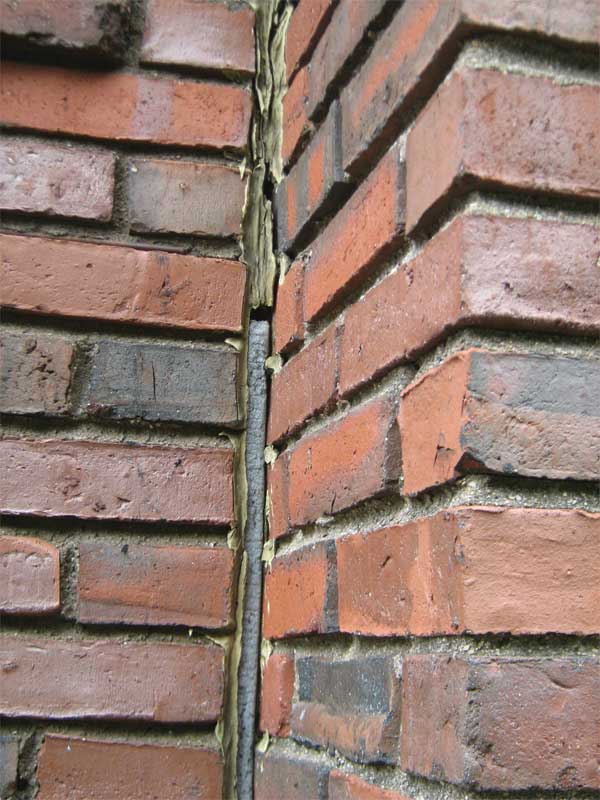
Properties of sealants
When selecting a sealant, one must consider the properties most impacting the specific application at hand. Here are the key sealant properties building professionals must evaluate.
Consistency
Sealants are available in pourable or non-sag formulations. Pourable sealants have a fluid consistency for use in horizontal joints, where they are self-leveling. Non-sag sealants are thicker and will not run down sloped or vertical joints.
Durability
The expected service life of a sealant under ideal conditions may not be the same as the actual field lifespan, especially if the sealant was misapplied or incompatible with the substrate. Generally speaking, silicones have the longest service life, estimated at 20 years or more, while some acrylics and butyls last little more than five.
Hardness
The harder a sealant, the greater its resistance to traffic and vandalism. However, as hardness increases, flexibility decreases, so the trick is to find the right balance of damage resistance and movement capability for a given situation.
Exposure resistance
The best exterior-grade sealants perform well in response to sun, temperature extremes, and moisture. Measures of exposure resistance include flexibility at low temperatures, freeze-thaw resistance, UV stability, and susceptibility to heat aging.
Movement capability
The higher a sealant’s movement capability, the more elongation or compression it can withstand without failure. Movement capability is expressed as a percentage of the joint width. For example, a sealant with ±10 percent movement capability in a 25-mm (1-in.) joint can stretch to 28 mm (1.10 in.) or contract to 23 mm (0.90 in.), and recover.
Modulus
Short for “modulus of elasticity,” modulus refers to sealant stress at a given elongation. Low-modulus sealants usually have high movement capability, and vice versa, although this is not always the case. Low-modulus sealants are generally employed for delicate substrates, for which it is desirable to have low stress at the joint edge. High-modulus sealants are best used for static, non-moving joints, because they exert a very high force on the substrate when stretched. Medium-modulus sealants are general-purpose products balancing stress at the adhesion surface with stiffness of the sealant.
Adhesion
The ability of a sealant to adhere to construction materials is an essential property to consider. Test methods such as ASTM C794, Standard Test Method for Adhesion-in-Peel of Elastomeric Joint Sealants, can evaluate the adhesion of elastomeric sealants. Manufacturers also provide data on sealant adhesion for various substrates.
Staining
The components of some sealants may leach into porous substrates, particularly natural stone, leaving a visible stain. To evaluate compatibility with the substrate, even sealants rated as non-staining should be tested in an unobtrusive area before use.
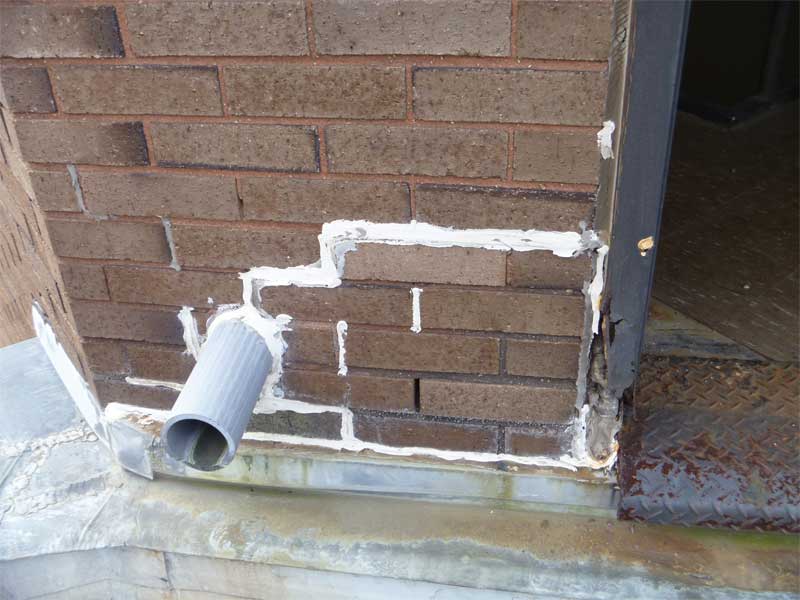
VOC content
Emission of volatile organic compounds from building products is regulated at the state and regional level. For occupied buildings, VOCs are a particularly important consideration. While most manufacturers have developed low-VOC sealants, some types have lower levels than others. Solvent-based sealants tend to have higher levels of respiratory irritants and environmental toxins, but VOC content varies widely by product.
Ease of application
Curing characteristics and toolability are the two major factors affecting a sealant’s ease of application. Toolability refers to the ease of achieving a smooth surface of correct geometry. Curing properties vary widely, from fast-curing sealants to those, such as polyisobutylene, that are designed to remain uncured.
Cost
As is the case with most building products, cheapest is not usually the best. In general, higher cost means higher performance. However, opting for a high-performance sealant when a less expensive alternative would do the job may mean one is overspending. Scrimping on sealants is not likely to do the prudent building owner any favors, though, as replacing failed sealants is nearly always more expensive than selecting the right sealant in the first place.
Causes of sealant failure
One of the most common causes of sealant failure stems not from the sealant itself, but from the size and spacing of the joints, which must be sufficient in number and in spacing to allow for seismic forces, thermal cycling, and differential movement of substrate materials. Different sealants have differing abilities to accommodate shear stress, caused by the faces of the joint sliding past one another, along with expansion and contraction as fluctuating temperatures cause the joint to widen or narrow.
Joints spaced too narrow or widely may force sealant to stretch beyond its capacity, which can cause the sealant to pull away from the substrate (adhesive failure) or to tear within itself (cohesive failure). Expansion of the substrate may compress the sealant beyond its tolerance, causing it to extrude out of the joint. An excessively wide joint may not be able to accept sealant at all, as it is likely to slough out of the large gap.
Properly designed sealant joints generally have a 2:1 width-to-depth ratio, a configuration allowing the joint to accommodate movement most effectively. Additionally, many manufacturers stipulate maximum and minimum dimensions in order for the sealant bead to perform within its movement capability.